लोखंड व पोलाद उद्योग : लोखंड हे धातुरूप मूलद्रव्यांपैकी सर्वांत उपयुक्त असून त्याची विपुलता ॲल्युमिनियमाच्या खालोखाल म्हणजे दुसऱ्या क्रमांकाची आहे. अशनींचा (बाह्य अवकाशातून पृथ्वीवर येऊन पोहोचलेल्या पृथ्वीबाहेरील पदार्थांचा) अपवाद सोडल्यास ते मूलद्रव्यरूपात विरळाच आढळते पण भूकवचात रासयनिक संयुगांच्या रूपात ते विपुल प्रमाणात आढळते. लोखंडाची सापेक्षत: कमी किंमत व ते मूलभूत घटक असलेल्या अनेक मिश्रधातू (मुख्यत्वे पोलादे) यांमुळे व्यवहारात वापरण्यात येणाऱ्या सर्व धातूंमये लोखंड ही सर्वांत विस्तृत प्रमाणात वापरण्यात येणारी धातू आहे. मूलद्रव्य वा पोलाद यारूपात लोखंडाचा हत्यारे, यंत्रसामग्री, वाहने, अनेक प्रकारच्या वस्तू व मोठ्या प्रमाणावरील बांधकामातील अधिकांश सांरचनिक घटक म्हणून मानवी संस्कृतीत उपयोग झालेला आहे. एखाद्या देशातील लोखंड व पोलाद यांच्या उत्पादनाचे प्रमाण हे त्याच्या औद्योगिकीरणाचे द्योतक समजले जाते. जागतिक धातू उत्पादनातील लोखंड व पोलाद यांचा वाटा सु. ९५.७% आहे. उच्च जीवनमान प्राप्त करून घेण्यासाठी प्रयत्न करणाऱ्या कोणत्याही देशात उच्च उत्पादमक्षम पोलाद उद्योग वाढत्या प्रमाणात आवश्यक झालेला आहे. प्रगत अर्थव्यवस्था टिकविण्यासाठी लागणाऱ्या पोलादाच्या हजारो वस्तू पुरविण्याकरिता आणि संरक्षणासाठी जहाजे, विमाने, जमिनीवरील वाहने, शस्त्रास्त्रे व इतर सामग्री पुरविण्याकरिता या उद्योगाची अत्यंत गरज आहे.
प्रस्तुत नोंदीत लोखंड व पोलाद उद्योगाचा इतिहास, लोह धातुकांचे (कच्च्या रूपातील धातूचे) जगातील साठे व वितरण, धातुकांचे खाणकाम व त्यांवरील प्रक्रिया, लोखंडाचे विविध धातुवैज्ञानिक प्रकार व त्यांची निर्मिती, लोखंड व पोलाद यांचा जागतिक व भारतीय उद्योग यांविषयी माहिती दिलेली आहे. लोखंडाची मूलद्रव्य या दृष्टीने माहिती (भौतिक व रासायनिक गुणधर्म. धातुकांचे प्रकार व त्यांची उत्पत्ती, संयुगे, मिश्रधातू व उपयोग) ‘लोखंड’ या नोंदीत दिलेली असून पोलादाचे विविध प्रका र व त्यांच्या निर्मितीच्या पद्धती, गुणधर्म व उपयोग, विविध वस्तू तयार करण्यासाठी त्यांवर करण्यात येणाऱ्या प्रक्रिया यांची माहिती ‘पोलाद’ या नोंदीत दिलेली आहे.
इतिहास : तांबे व सोने या धातू शुद्ध धातुरूपात भूकवचात अनेक ठिकाणी आढळतात आणि त्या इ.स.पू. ७००० च्या सुमारास उपयोगात आल्या होत्या. शुद्ध धातुरूपातील लोखंड फक्त ग्रीनलंडच्या काही मर्यादित क्षेत्रात आढळते पण लोहयुक्त अशनींपासून इतिहासपूर्व काळात शोभिवंत वस्तू व हत्यारे बनविण्यात आली होती, असे दिसून आले आहे. अशनीतील लोखंडात ४ ते १८% निकेल असते व त्यामुळे एखाद्या मानवनिर्मित जुन्या लोखंडी वस्तूतील निकेलाचे उच्च प्रमाण ती अशनीपासून बनविलेली असावी असे दर्शविते. उत्तर व दक्षिण अमेरिका व ऑस्ट्रेलिया यांच्याशी तुलना करता नैऋत्य आशियात व यूरोपात इतिहासपूर्व कालातील धातुयुक्त अशनी फार कमी प्रमाणात आढळले आहेत. याचे कारण कदाचित इतिहासपूर्व काळात तेथील लोकांनी बहुतेक अशनी अगोदरच उपयोगात आणले असावेत. तथापि अशनी हा लोखंडाचा अगदीच मर्यादित उद्गम होता व लोखंड त्याच्या धातुकांचे प्रगलन करून (वितळवून) मिळविण्याच्या पद्धती समजून येईपर्यंत त्याचा विस्तृत प्रमाणात उपयोग होऊ शकला नाही.
लोखंडाचा शोध ब्राँझयुगाच्या अखेरच्या काळात आकस्मिकपणे लागला असावा. जमिनीवर उघड्या पडलेल्या तांबड्या लोह धातुकावर (आयर्न ऑक्साइडावर) शेकोटी पेटविल्यावर नंतर तिच्या राखेत धातवीय लोखंड प्रथम आढळले असावे. लोखंडाचे उपयुक्त गुणधर्म समजून आल्यावर व तांबडे लोह दातुक हा त्याचा उद्गम असल्याचे कळल्यावर लोखंडाच्या उत्पादनास प्रारंभ झाला. प्रचलित वाऱ्यांमुळे उघड्या पडलेल्या धातुकांच्या कडांसमोरील खड्ड्यांत आगी पेटवून आणि पुढे खडकाच्या ओबडधोबड भट्ट्या बनवून व त्यांतील अग्नी भात्याने फुलवून आयर्न ऑक्साइडाच्या ⇨क्षपणाने धातवीय लोखंड मिळविण्यात आले. लोखंडाची हत्यारे व शस्त्रे यांमुळे निकटपूर्व व अतिपूर्व देशांत नवीन युग सुरू झाले. ईजिप्तमध्ये अनेक प्राचीन अवशेषस्थळी लोखंड आढळले आहे. गीझा येथील इ.स.पू. २९०० च्या सुमारास बांधलेल्या कूफू पिरॅमिडामध्ये दोन लोखंडी तुकडे मिळाले आहेत. हिटाइट लोकांच्या इ.स.पू. १९०० ते १२०० या काळातील वस्तूंत ओतीव लोखंडाचे कडे सापडले आहे. इ.स.पू. १३०० पासूनच्या लोखंडाच्या अनेक प्रगलन भट्ट्या इझ्राएलमध्ये आढळलेल्या आहेत.
लोह धातुके तांब्याच्या व कथिलाच्या धातुकांपेक्षा पुष्कळ विपुल प्रमाणावर आढळतात पण त्यांचे प्रगलन करणे अधिक अवघड असते. धातुकापासून तांबे इ.स.पू. ३५०० च्या सुमारास मिळविण्यात आले. प्रगलन केलेले लोखंड त्यानंतर सु. १,५०० वर्षांनी दक्षिण ॲनातोलियातील (आशिया मायनर) हिटाइट व कालबीझ लोकांनी तयार केलेल्या वस्तूंत आढळते. लोखंड दुष्प्राप्य असल्याने व त्याचे गुणधर्म ब्राँझशी तुलना करता कमी प्रतीचे असल्याने प्रारंभी लोखंड अलंकारांत व समारंभ प्रसंगी शस्त्रांकरिता वापरती असत. प्रगलन प्रक्रियेचा अधिक अनुभव आल्यावर लोहार कार्बनाचे पुरेसे प्रमाण असलेले व ब्राँझपेक्षा अधिक बळकट असलेले लोखंड तयार करण्यास शिकले. इ.स.पू.सु. १००० पर्यंत पॅलेस्टाइन व ईजिप्तमध्ये लोखंड व ब्राँझ यांचा मोठ्या प्रमाणावर उपयोग होऊ लागल्याचा पुरावा उपलब्ध आहे. नैर्ऋत्य आशियातून लोह प्रगलन पद्धतीचा इतरत्र प्रसार झाला. ती इ.स.पू. ९०० पर्यंत ग्रीसमध्ये, इ.स.पू. ८०० पावेतो मध्य यूरोपात, इ.स.पू. ५०० पर्यंत ब्रिटन व चीनमध्ये आणि इ.स.पू. ४०० पर्यंत पश्चिम आफ्रिकेत पोहोचली.
इतिहासपूर्व काळात लोखंडाचे प्रगलन लोहखंड (ब्लूम) तयार करण्याच्या भट्टीत करीत. या पद्धतीत बंदिस्त चुल्यात लोणारी कोळसा जाळून त्यापासून तयार होणाऱ्या कार्बन मोनॉक्साइडाने लोह धातुकातील आयर्न ऑक्साइडाचे क्षपण करीत. धातवीय लोखंड धातुकातील अधातवीय भागापासून अलग करण्यासाठी या भागाची काही आयर्न ऑक्साइडाबरोबर विक्रिया होऊ देऊन धातुमळी तयार करीत. या भट्टीचे कार्य १,२००°– १,४००° से. तापमानाला चालत असे. धातुमळी १,२००° सें.ला व शुद्ध लोखंड धातू १,५३४०° से.ला वितळत असल्याने लोखंड घनरूपात, तर मळी द्रवरूपात तयार होई. बहुतेक द्रव मळी वेगळी होई व मळीचा काही अंश असलेला लोहखंड तयार होई. या प्रगलनास शेवटी गरम लोहखंड हातोड्याने ठोकून शक्य तितकी मळी काढून टाकीत. काही नळी अपरिहार्यपणे मागे राहत असल्याने लहान तंतुमय मळीचे कण हे घडीव लोखंडाचे वैशिष्ट्य असते.
लोहखंड प्रगलनाला धातुक व इंधन तयार करणे, भट्टी चालू ठेवणे व लोहखंडापासून अंतिम संस्कारित वस्तू घडविणे या सर्व बाबतींत बरेच कौशल्य लागत असे. तयार होणाऱ्या लोखंडाची गुणवत्ता लोहाराच्या कौशल्यावर अवलंबून असे. यामुहे कुशल प्रगलन करणारे व कुशल लोहार लोखंड तयार करण्यातील आपला लौकिक प्रस्थापित करू शकत आणि आपल्या कलेद्वारे आश्रयदात्यांना व्यापारी वा लष्करी वर्चस्व मिळवून देत.
इ.स.पू. ५०० पावेतो लोह प्रगलनाच्या तंत्रविद्येचा प्रसार नैर्ऋत्य आशियातून चीनपर्यंत झाला. हा प्रसार कदाचित भारतमार्गे झाला असावा; तथापि मध्ययुगातील काळाच्या पूर्वीच्या भारतीय लोह उद्योगाची फारच अल्प माहिती उपलब्ध आहे (भारतीय लोह उद्योगाचा इतिहास पुढे दिला आहे). चीनमध्ये लोह धातुविज्ञानाचा विकास भिन्न मार्गाने झाला. प्रथमतः लोहखंड पद्धतीने तेथे लोखंड बनविण्यात येत होते पण बीड (ओतीव लोखंड) हे उपयुक्त असल्याचे चिनी लोकांना इतर लोकांपेक्षा किती तरी अगोदर समजले होते. इ.स.पू. चौथ्या शतकापासूनच्या बिडाच्या तलवारी व शेतीची अवजारे तेथे सापडली आहेत. त्यानंतर चिनी लोह धातुविज्ञानात बिडाचेच वर्चस्व होते.
बिडाची भट्टी लोहखंड पद्धतीच्या भट्टीपेक्षा मोठी असते व तीत अधिक उच्च तापमान मिळते. या भट्टीत लोह-कार्बन-सिलिकॉन मिश्रधातू वितळण्याइतपत उच्च तापमान आवश्यक असल्याने जळणाऱ्या कोळशातून हवेचा तीव्र झोत सोडावा लागतो आणि यामुळे तिच्यातील विक्रिया पात्राला ‘झोतभट्टी’ म्हणतात. झोपभट्टीचे सर्वांत ज्ञात पुरातन अवशेष हान काळातील (इ.स.पू.सु. १३०) सापडले आहेत. या भट्टीला हवेचा झोत बहुधा मानवी बळाने दट्ट्याच्या भात्याने पुरविला जात असावा. इ.स. पहिल्या शतकापावेतो झोतभट्ट्या चालविण्यासाठी जलशक्तीचा उपयोग करण्यात येऊ लागला होता व लोखंडाच्या उत्पादनाचे प्रमाणही पुष्कळ वाढले होते. इ.स. पाचव्या शतकापसून चीनमध्ये लोखंड विपुल प्रमाणात मिळू लागले लोणारी कोळशाच्या जागी दगडी कोळसा वापरात आला आणि अवजारे व शस्त्रे तयार करण्यासाठी मोठ्या प्रमाणावर लोखंडाचा उपयोग होऊ लागला होता. बिडाच्या मोठ्या घंटा बनविण्यात आल्या. पोलाद तयार करण्याच्याही कित्येक प्रक्रिया प्रचलित होत्या. त्यांतील सर्वांत उत्तम पद्धतीत बिडातील कार्बन पृष्ठीय निरास पद्धतीने काढून टाकून पोलाद बनविले जाई. या पद्धतीत उत्कृष्ट दर्जाच्या पोलादाचे उत्पादन करण्याची क्षमता होती.
सातव्या शतकापावेतो चिनी पोलादनिर्मिती पद्धती जपानपर्यंत पोहोचली. तेथे तीत पुष्कळ सुधारणा झाली आणि जपानी लष्करी विधीचा प्रमुख भाग असलेल्या समुराई तलवारीत वापरण्यात येणाऱ्या लोखंड व पोलाद यांच्या निर्मितीस ती आधारभूत झाली.
इ.स.पू. ३५० पावेतो लोह प्रगलनाची तंत्रविद्या नैर्ऋत्य आशियातून त्या काळी वृक्षमय असलेल्या सहाराद्वारे पश्चिम आफ्रिकेत गेली. तेथून लोहखंड प्रगलन पद्धती मध्य व दक्षिण आफ्रिकेत पसरली. लोखंडाचे मोठ्या प्रमाणावर उत्पादन करणारी केंद्रे कित्येक ठिकाणी निघाली. टोगोमध्ये प्रगलनाकरिता लाकूड फार मोठ्या प्रमाणावर वापरले गेल्याने तेथील वने जवळजवळ पूर्णपणे नाहीशी झाली. शोभिवंत लोखंडी काम करण्यात येई पण बहुतांश लोखंड चाकू, भाल्यांची टोके व बहुतेक सर्व आफ्रिकेत आढळणाऱ्या कठीण शेतजमिनीची मशागत करण्यासाठी लागणारी कुदळीसारखी अवजारे यांकरिता वापरले जात होते. मध्य व दक्षिण आफ्रिकेत सर्वत्र लोहखंड पद्धतीने लोखंड तयार करणे हा कृषिचक्राचा एक आवश्यक भाग बनला आणि विसाव्या शतकातही तो तसाच चालू राहिला.
रोमन लोकांना ग्रीक लोकांकडून लोहकामाच्या तंत्राचा वारसा मिळाला. त्यांनी या तंत्राचा दर्जा बराच सुधारला व त्याचा उत्तर यूरोपात प्रसार केला. मध्य यूरोपातील पुरातत्त्वीय उत्खननांत हत्यारे, शस्त्रे, चिलखते यांसारख्या वस्तू मिळाल्या असून त्यांवरून इ.स.पू. ८०० नंतरचे तेथील घडाईकामाचे कौशल्य दिसून येते. रोमन साम्राज्याच्या काळापूर्वी बहुतांश उत्तर यूरोपात लोखंडाच्या वस्तू दैनंदिन आयुष्याचा भाग बनलेल्या होत्या. तेथे सापडलेल्या लोखंडी वस्तूंत साखळ्या, वस्तरे, रथाच्या धावा, शेकोटीची साधने, कुऱ्हाडी, चाकू, घोड्याच्या सरंजामाची जोडसाधने वगैरेंचा समावेश आहे. रोमन वर्चस्वामुळे लोखंडाच्या उत्पादनात खूप मोठ्या प्रमाणात वाढ झाली पण तांत्रिक बदल फारसे झाले नाहीत. रोमन काळातील ओतीव वस्तू चेकोस्लोव्हाकिया, फ्रान्स व ब्रिटन येथे सापल्या आहेत. थोरले प्लिनी (इ.स. २३-७०) यांनी आपल्या Historia Naturalis या ग्रंथात लोखंडाचे उत्पादन व उपयोग या विषयाला दोन प्रकरणे दिली होती.
जरी ⇨लोहयुगाची सुरुवात इ.स.पू. १२०० च्या सुमारास झाली असे पुरातत्त्ववेत्ते साधारणपणे मानत असले, तरी यूरोपीय मध्ययुगात लोखंडी तोफा प्रचारात आल्यावरच लोखंडाने तांबे व ब्राँझ यांना मागे टाकून त्या काळी उपयोगात असलेल्या धातूंमध्ये प्रथम स्थान मिळविले. रोमन काळाच्या नंतरच्या लगेचच्या काळात लोखंडाच्या उत्पादनात घट झाली परंतु इ.स. २०० च्या सुमारास उत्तर यूरोपात नवीन सुविकसित घडाई तंत्र (आकृतिबंधीय वितळजोडकाम) प्रचारात आले. या तंत्राने लोखंड व पोलाद यांच्या शोभिवंत आकृतिबंधात संयोग तयार होत असे. तलवारीच्या पात्याकरिता हे तंत्र वापरल्यास संमिश्रणाने (याला स्तरित पोलाद असेही म्हणतात) उत्कृष्ट बलाचे शस्त्र तयार होत असे. पोलाद लोखंडापेक्षा कठीण आणि द्रुतशीतनाने व अनुशीतनाने अधिक कठीण करता येई पण पोलादात लोखंडाचा चिवटपणा नसे. लढाईत लोखंडाची तलवार वाकेल, तर पोलादाच्या तलवारीचा कटकन तुकडा मोडेल. लोखंड व पोलाद यांचा संयोग करून कठीण, धारदार कडा व चिवट अंतर्भाग असलेले संमिश्र पाते तयार करणे शक्य झाले. त्या काळात लोहाराचे तांत्रिक व कलात्मक कौशल्य काही आख्यायिकांना आधारभूत झाले (उदा., ब्रिटनचे राजे आर्थर यांची एक्सकॅलिबर तलवार).
इ. स. सु. १००० पासून तयार करण्यात येणाऱ्या दमास्कस तलवारीला सुद्धा आकृतिबंधित पोलादी पाते होते पण ते आकृतिबंधीय वितळजोडकामाने केलेले नव्हते. दमास्कस पाती भारतीय ओतीव पोलादापासून (याला ‘वुट्स पोलाद’ म्हणत) तयार करीत. या पोलादात विशेष संरचना असून ती पोलादाच्या घनीभवनामध्ये तयार होत असे व घडाईनंतरही ती कायम राहात असे. दमास्कस पोलादी पाती कित्येकदा सुरेख पोताची व अतिशय तीक्ष्ण कडांची आढळतात; पण आकृतिबंधीय वितळजोड केलेल्या पात्यांचा चिवटपणा त्यांत नसतो.
मध्ययुगाच्या प्रारंभीच्या काळात यूरोपातील धातुवैज्ञानिक तंत्रविद्या आशियातील व आफ्रिकेतील अनेक ठिकाणी प्रचलित असलेल्या तंत्रविद्येपेक्षा जास्त प्रगत अवस्थेत नव्हती. तथापि तेराव्या शतकापासून उत्तर यूरोपात झालेल्या तांत्रिक विकासामुळे लवकरच यूरोपीय धातुविज्ञान जगाच्या इतर भागांत वापरात असलेल्या धातुविज्ञानापेक्षा भिन्न मार्गाने जाऊ लागले. भाता चालविणे व लोखंड घडविणे या क्रिया कष्टदायक आहेत. हे कठीण काम करणाऱ्या माणसांच्या व जनावरांच्या मर्यादित क्षमतेमुळे लोखंडाच्या उत्पादनाचे प्रमाणही मर्यादित राहिले. गुलाम कामकरी कदाचित वापरीत असलेल्या चीनचा मात्र याला अपवाद होता. प्राचीन काळी मुख्यत्वे धान्य दळण्यासाठी वापरण्यात येत असलेल्या जलचक्कीचा यूरोपात सर्वत्र प्रसार झालेला होता. ⇨कॅम या साधनाचा शोध लागल्यावर जलचक्कीच्या दंडापासून पश्च-अग्र (पुढे-मागे होणारी) गती मिळू लागून तीद्वारे भाता वरखाली करणे व घडाईचे हातोडे वर उचलणे शक्य होऊ लागले. यामुळे लोहखंड घडाईशाला (ब्लूमरी) मोठ्या करता येऊ लागल्या. चौदाव्या शतकापावेतो जर्मनी व ऑस्ट्रिया येथील उंच घडाईशाला दर दिवशी ४०० किग्रॅ. लोखंड तयार करीत होत्या. दक्षिण फ्रान्स व उत्तर स्पेन येथे तेराव्या शतकात प्रचारात आलेल्या व जलशक्तीवर चालणाऱ्या कॅटॅलान घडाईशालांत यापेक्षाही जास्त प्रमाणात लोखंड तयार होई. अशा घडाईशाला तेथे एकोणिसाव्या शतकातही प्रचलित होत्या. कॅटॅलान भट्टी ही आधुनिक झोतभट्टीची स्पष्टपणे पूर्वज होती. या भट्टीत पडणाऱ्या पाण्याच्या उभ्या स्तंभाचा उपयोग एका संग्राहक पेटीत हवा शोषून घेण्यासाठी केला होता आणि लोह धातुक व लोणारी कोळसा यांचे मिश्रण तापविण्यासाठी या पेटीतून सतत, खात्रीशीर आणि सापेक्षतः तीव्र हवेचा झोत पुरविला जाई. कॅटॅलान भट्टीपासून मिळणारे लोखंड जवळजवळ पूर्वीच्या चुल्याच्या भट्ट्यांपासून मिळणाऱ्या लोखंडासारखेच असे परंतु तिच्या उच्च कार्यकारी तापमानामुळे तयार होणारे कच्चे लोखंड सापेक्षतः मळीपासून मुक्त असे व तिचा उत्पादन वेगही जास्त होता. कॅटॅलान भट्टीपासून चुला प्रकारच्या भट्ट्यांचे कित्येक प्रकार विकसित झाले. या प्रत्येक भट्टीत धातुक व कोळसा भरण्यासाठी चुल्यावरती आखूड नळासारखी रचना (स्टॅक) असे. या प्रकारच्या स्ट्यूकोफेन या सर्वांत प्रारंभीच्या भट्टीचा आता स्टीरिया (आग्नेय ऑस्ट्रिया) या नावाने ओळखण्यात येणाऱ्या प्रदेशात मध्ययुगात उदय झाला. ही भट्टी ३ ते ५ मी. उंच होती. स्ट्यूकोफेन भट्टीची उंची जास्त असल्याने धातुक नळातून खाली जात असताना त्याचे लवकर क्षपण होत असे. जळणाऱ्या कोळशाची अधिक काळ संपर्क आल्याने तयार होणाऱ्या लोखंडाच्या गोळ्यात चलायुक्त भट्ट्यांपेक्षा अधिक कार्बनाचे शोषण होई. उच्चतर कार्बनाचा अंश असलेल्या लोखंडाचा वितळबिंदू कमी होऊन स्ट्यूकोफेन भट्टीत काही वेळा द्रवरूप लोखंड तयार होत असे. यानंतरच्या विकासाच्या टप्प्यातील स्ट्यूकोफेनपेक्षा अधिक उंच नळ असलेल्या फ्ल्यूझोफेन या भट्टीत वितळलेले उच्च कार्बनयुक्त लोखंड अखंड क्रियेने तयार होत असे. भट्टीच्या वरच्या भागात धातुक, लोणारी कोळसा व चुनखडी भरल्यावर वितळलेले लोखंड चुल्याच्या तळभागातून बाहेर काढण्यात येई. चुल्याच्या भट्टीपासून खऱ्या झोतभट्टीपर्यंत सावकाश झालेल्या उत्क्रांतीत इतरही कित्येक थोड्याशा भिन्न असलेल्या भट्ट्यांचा सहभाग होता.
जलशक्तीवर चालणारे भाते वापरणारी लोहखंड घडाईशाला झोतभट्टीप्रमाणे वापरून बीड तयार करणे शक्य आहे. स्वीडनमध्ये तेराव्या शतकात असा उपयोग केल्याचे दिसून आले आहे. यानंतर यूरोपातील नोंदीतून झोतभट्टी नाहीशी झालेली दिसते व तिचा इतिहास अद्यापही अस्पष्टच आहे. सध्या उपलब्ध असलेले पहिले वर्णन उत्तर इटलीतील झोतभट्टीचे असून ते १४६५ मध्ये लिहिलेले आहे. तथापि पश्चिम यूरोपात सोळाव्या शतकाच्या प्रारंभी झोतभट्ट्या सर्वत्र उपयोगात होत्या. इ.स. १५०० च्या सुमारास इंग्लंडमध्ये पहिली झोतभट्टी उभारण्यात आली. झोतभट्टीत तयार झालेल्या बिडाचे घडाईकामाच्या चुल्यात घडीव लोखंडात रूपांतर करता येत असे. हा चुला लोहखंड घडाईशालेतील चुल्यासारखाच होता. झोतभट्टीत घनरूपाऐवजी द्रवरूप लोखंड मिळत असल्याने भांडी व तोफा यांसरख्या वस्तू ओतकामाने तयार करण्यासाठी त्याचा उपयोग होत असे. अशा वस्तू घडीव लोखंडापासून घडाईने व वितळजोडकामाने तयार करणे अवघड असे. मध्ययुगात ओतीव वस्तूंची यूरोपात मागणी वाढल्याने लोहखंड घडाईशालेची जागा हळूहळू झोतभट्टीने घेतली.
प्रबोधनकालीन यूरोपातील युद्धावस्थेमुळे लोखंड उद्योगाच्या वाढीस जोरदार उत्तेजन मिळाले. तटबंदी व तोफखाना यांतील सुधारणांमुळे लोखंडापासून तयार केलेल्या शस्त्रांची मागणी एकसारखी वाढती राहिली. इंग्लंडचे राजे आठवे हेन्री (१४९१ -१५४७) यांना माफक खर्चात दीर्घ सागरी किनाऱ्यांचे संरक्षण करण्याचा प्रश्न पडला होता. त्यामुळे त्यांनी यूरोपातील झोतभट्टीचा व ओतकाम तंत्राचा इंग्लंडात वापर करण्यास प्रोत्साहन दिले. लष्करी मागणीत मंदी आल्यावर लोखंड कारखानदारांनी नागरी बाजारपेठेच्या गरजा भागविण्याकडे लक्ष पुरविले. १५८५-१६८५ या काळात इंग्लंडमधील १,००० व्यक्तींमागील लोखंडाचे उत्पादन ४.५ टनांवरून ९ टनांपर्यंत गेले व १७३० मध्ये ते ११.४ टनांपर्यंत पोचले.
इंग्लंडात वने विपुल प्रमाणात कधीच नव्हती आणि त्यांच्यावर बांधकाम व जहाज बांधणी यांसारख्या स्पर्धात्मक उपयोगांमुळे वाढता ताण पडत होता. सोळाव्या शतकाच्या मध्यापासून लोखंड कारखानदारांना कोळसा बनविण्यासाठी लाकडाचा वापर परवडणे अधिकाधिक अवघड झाले. यावर उपाय म्हणून लाकडाचा अविरत पुरवठा मिळविण्यासाठी पुरेशी जंगलाची जमीन संपादन करणे आवश्यक होते. लाकूड कापून घेतलेली झाडे साधारणपणे २० वर्षांत पुष्कळशा लाकडाचे पुनर्जनन करू शकतात. एका वर्षात जेवढी जमीन लागेल त्याच्या २० पट जमीन संपादन करून इंधनाच्या सतत पुरवठ्याची खात्री करणे शक्य आहे. सतराव्या शतकातील झोतभट्टी व घडाईशाला यांकरिता सु. ५,२०० हेक्टर जमीन लागत असे. ही पद्धत म्हणजे वन साधनसंपत्तीच्या व्यवस्थापनाचे एक प्रारंभीचे उदाहरण होते व त्यामुळे लोखंड उद्योगातील इंधन तुटवड्याला प्रतिबंध झाला. तथापि सतराव्या शतकाच्या मध्यपावेतो झोतभट्टीसाठी लोणारी कोळशाऐवजी दगडी कोळसा इंधन म्हणून वापरणे अधिक काटकसरीचे होईल, हे स्पष्ट झाले. दगडी कोळसा वापरण्याचे प्रयोग १६२२ मध्ये सुरू झाले होते पण बहुतेक कोळशात गंधकाचे प्रमाण उच्च असल्याने तयार होणारे लोखंड सामान्य प्रतीचे होई. कोलब्रुकडेल येथे अब्राहम डर्बी यांना १७०९ मध्ये या दृष्टीने व्यावहारिक यश मिळाले. डर्बी यांनी कमी प्रमाणात गंधक असलेला कोळसा उघड्या खड्ड्यांत अंशतः जाळून त्याचे ⇨कोकमध्ये रूपांतर केले. भांडी व इतर पातळ भित्ती असलेल्या वस्तू तयार करण्यास योग्य असे लोखंड मिळविण्यात त्यांना यश मिळाले. डर्बी कुटुंबाचा हा उपक्रम पुढे वाढून १७७७ पावेतो पहिल्या बिडाच्या पुलाकरिता कमानी बनविणे त्यांना शक्य झाले. हा पूल व डर्बी लोखंड कारखान्याची जागा यांचे आता औद्योगिक संग्रहालय बनविण्यात आले आहे.
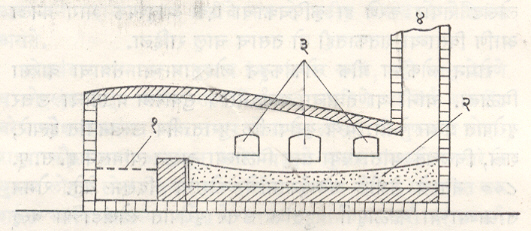
हेन्री कोर्ट यांनी १७८४ मध्ये पिग (कच्च्या) लोखंडाचे (या लोखंडाला पिग लोखंड असे नाव पडण्याचे कारण पुढे दिले आहे) वर्धनशील (ठोकून आकार देता येण्यासारख्या) घडीव लोखंडात रूपांतर करण्याची ढवळणी (पडलिंग) प्रक्रिया शोधून काढल्यावर दगडी कोळसा लोखंडाच्या निर्मितीत वापरण्यातील अखेरची पायरी गाठली गेली. कोर्ट यांनी पिग लोखंड वितळविण्यासाठी परावर्तन भट्टीचा उपयोग केला. यात भट्टीच्या एका टोकापाशी कोळसा जाळून उष्ण वायू दुसऱ्या टोकाकडील लोखंडावरून जातात. लोखंडाचा कोळशाशी प्रत्यक्ष संपर्क येत नसल्याने ते कोळशातील गंधकाने दूषित होत नाही. एकदा वितळल्यावर पिग लोखंड हवेच्या उपस्थितीत ढवळल्याने त्यातील कार्बन व सिलिकॉन यांचे ⇨ऑक्सिडीभवन होते. लोखंड जसजसे शुद्ध होत जाते, तसतसे त्याचे लोखंडाच्या गोळ्यात व मळीमध्ये (पुष्कळसे लोहखंडासारखे) रूपांतर होते आणि त्या गोळ्याचे पुढे हातोड्याने ठोकून व लाटून घडीव लोखंडात रूपांतर करता येते. ढवळणी भट्टी चालविण्याचे काम एक ढवळणारा माणूस व त्याच्या मदतीला एक शिकाऊ उमेदवार असे दोघे मिळून करू शकत. ते १२ तासांच्या पाळीत दर दोन तासांना सु. २२५ किग्रॅ. लोखंड तयार करू शकत. हे काम कष्टाचे व आरोग्याला हानीकारक असले, तरी १८७० पर्यंतच्या काळात रेल्वे, पूल व जहाजे यांना लागणाऱ्या मोठ्या प्रमाणावरील लोखंडाची निर्मिती याच पद्धतीने केली जात असे.
पोलादनिर्मितीतही मध्ययुगानंतरच्या काळात महत्त्वाचा विकास घडून आला. प्राचीन पद्धतीत लोहखंडातील कार्बनसंपन्न भाग निवडले जात. धातूतील कार्बनाच्या प्रमाणावर समाधानकारकपणे नियंत्रण ठेवणे शक्य नसल्याने हे भाग निवडण्याचे काम अनिश्चित स्वरूपाचे असे. चेकोस्लोव्हाकियातील प्राग येथे साधारण १५७४ च्या अगोदरच्या काळात कार्बन प्रमाणावर अधिक बारीक नियंत्रण ठेवण्याची पद्धती उपयोगात आली. कार्बनमुक्त घडीव लोखंडाच्या कांबी लोणारी कोळशाची पूड भरलेल्या बंदिस्त पेटीत ठेवल्या जात आणि एक आठवडाभर तांबड्या लाल तापविलेल्या स्थितीत ठेवीत. कोळशातील कार्बन लोखंडात अंतः प्रविष्ट होऊन लोखंडाचे पोलादात रूपांतर होत असे. हे रूपांतर करणारी भट्टी चालू ठेवण्याच्या काळावर कार्बनाच्या अंत:प्रवष्टिनाचे प्रमाण अवलंबून असे. या पद्धतीत लोखंडाच्या अंतर्भागात तयार होणाऱ्या कार्बन मोनॉक्साइडामुळे पोलादाचा पृष्ठभाग फोड आल्यासारखा दिसतो म्हणून अशा पोलादाला पुळीदार (ब्लिस्टर) पोलाद म्हणतात. या पोलादाचे लहान तुकडे करून वितळजोडकामाने जोडल्यास कर्तन पोलाद हा अधिक एकजिनसी प्रकार तयार करता ये तो. उच्च दर्जाची कटलरी (चाकू, कातऱ्या, शस्त्रक्रियेची हत्यारे इ.) तयार करण्यासाठी या पोलादाचा विस्तृत प्रमाणात उपयोग केला जात होता. सतराव्या शतकाच्या प्रारंभापावेतो जर्मनीतील न्यूरेंबर्ग हे कर्तन पोलाद तयार करण्याचे महत्त्वाचे केंद्र बनले. अठराव्या शतकात इंग्लंडमधील शेफील्ड पोलाद व कटलरी उद्योगाचे प्रमुख केंद्र झाले. शेफील्ड येथे पोलादनिर्मितीतील एक पुढची महत्त्वाची पायरी १७४७ च्या सुमारास गाठली होती. घडीव लोखंडापासून पोलाद तयार करण्यात येत असल्याने त्यात लोखंडामध्ये अंतर्भूत असलेली मळीही राहात असे. या मलद्रव्यांमुळे पोलादाचे बल कमी होत असे व घड्याळाच्या स्प्रिंगांसारख्या लहान भागांच्या बाबतीत ही गोष्ट महत्त्वाची ठरते. बेंजामीन हंट्समन (१७०४–७६) यांनी पोलाद वितळविता येईल इतकी मजबूत मूस तयार केली. वितळल्यावर मळी पृष्ठावर तरंगते व ओतीव पोलादाचा निर्दोष पिंड ओतता येतो. शेफील्डच्या ओतीव पोलादाच्या गुणवत्तेची कीर्ती यूरोपात व अमेरिकेत दूरवर पसरली आणि एकोणिसाच्या शतकाच्या अखेरपर्यंत ते तीक्ष्ण हत्यारे व कटलरी यांकरिता अधिक पसंत केले जात होते.
अमेरिकेतील मूळचे लोक अशनींपासून मिळणऱ्या व ग्रीनलंडमध्ये आढळणाऱ्या शुद्ध धातुरूपातील लोखंडाचा काही प्रमाणात वापर करीत असत; पण अन्यथा अमेरिका खंडात यूरोपीयनांचे आगमन होण्यापूर्वी लोखंडाची निर्मिती वा उपयोग केला जात नव्हता. व्हर्जिनियातील वसाहतवाल्यांनी स्वतःचे लोखंड तयार करण्याचे उद्दिष्ट ठेवलेले होते. निर्यातीकरिता लोखंड तयार करण्याच्या व्हर्जिनियातील फॉलिंग क्रिक येथे प्रयत्न करण्यात आला; पण तेथील कर्मशाळा रेड इंडियन लोकांनी केलेल्या कत्तलीत १६२२ मध्ये नष्ट झाली. त्यानंतरचा प्रयत्न १६४० मध्ये जॉन विन्थ्रप यांनी मॅसॅचूसेट्समधील सॉगस येथे केला. इंग्लंडमध्ये भरती केलेल्या कामगारांनी तेथे १६४७ पावेतो झोतभट्टी, बिडाचे घडीव लोखंडात रूपांतर करण्याचा चुला व लोखंड कापणारे यंत्र चालू केलेले होते. तेथे बिडाच्या वस्तू व खिळे तयार करण्यासाठी कांबी यशस्वीपणे बनविण्यात आल्या परंतु दूरच्या बाजारपेठेसाठी उत्पादन करण्यातील अडचणी वसाहतवाले सोडवू शकले नाहीत. त्यामुहे पाच वर्षांतच उपक्रम बंद पडला व तेथील कर्मशाळा उजाड झाली. १९५० नंतरच्या दशकात या जागेची पुन्हा बांधणी करून ते ऐतिहासिक राष्ट्रीय स्थळ म्हणून जतन करण्यात आलेले आहे.
इ.स. १७२० च्या सुमारास निर्यातीसाठी व अंतर्गत उपयोगासाठी लोखंड तयार करण्याच्या उद्योगाला पुन्हा चालना मिळाली. नंतरच्या काही दशकांत व्हर्जिनिया व मॅसॅचूसेट्स यांच्या दरम्यानच्या बहुतेक वसाहतीत लोह कर्मशाळा उभारण्यात आल्या. त्यां तील घडीव लोखंड तयार करणाऱ्या लोहखंड घडाईशाळांची संख्या सर्वांत जास्त होती पण काही झोतभट्ट्याही सर्व वसाहतींत होत्या. बीड हे भांडी व शेगड्या यांसारख्या वस्तू तयार करण्यासाठी किंवा घडाईशाळांना दंडरूप लोखंडात रूपांतर करण्यासाठी पाठविले जाई. या उद्योगाने अमेरिकन क्रांतीला (१७७५–८३) युद्धसाहित्य पुरविले, तसेच औद्योगिकीकरणाच्या प्रारंभीच्या टप्प्यांत लागलेले लोखंड पुरविले.
अमेरिकेतील वनांपासून लोहनिर्मितीला विपुल इंधन मिळाले; पण लाकूड तोडणे, गोळा करणे व ते जाळून कोळसा बनविणे यांसाठी पुष्कळ मजूर लागत. पेनसिल्व्हेनियात कालवे बांधले गेल्यांनतर त्यांतून शहरी बाजारपेठांत पाठविता येईल अशी अँथ्रॅसाइट ही दगडी कोळशाची जाती पर्यायी इंधन म्हणून उपलब्ध झाली. यांपैकी कित्येक कालवे लोखंडाच्या खाणींजवळून जात असल्याचे कमी खर्चात इंधन व धातुक एकत्र वाहून आणण्याची शक्यता निर्माण झाली. तथापि लोखंड तयार करण्यासाठी आवश्यक असलेली तंत्रविद्या यूरोपातून सरळ उसनी घेणे शक्य नव्हते, कारण तेथे अँथ्रॅसाइटाऐवजी कोक वापरण्यात येत होता. १८३० पावेतो पेनसिल्व्हेनियात ढवळणी प्रक्रिया व अँथ्रॅसाइट यांचा वापर करणारी एक भट्टी उपयोगात होती. दहा वर्षानंतर पेनसिल्व्हेनियात व न्यू जर्सीत कालव्यांच्या बाजूने अँथ्रॅसाइट इंधन वापरणाऱ्या झोतभट्ट्या उभारण्यात आल्या. या भट्ट्यांना पुरवायच्या हवेच्या झोताच्या पूर्वतापनासाठी शेगड्या जोडण्यात आलेल्या होत्या. अँथ्रॅसाइट इंधन वापरणाऱ्या भट्ट्यांनी लोखंड तयार करण्याच्या मजुरीचा खर्च लोणारी कोळसा वापरणाऱ्या भट्ट्यांपेक्षा फक्तएक पंचमांश होता. लोखंडाच्या उपलब्धतेमुळे उत्तर अमेरिकेतील अंतर्गत वाहतुकीचे रूप बदलण्यास सुरुवात करणारे रेल्वेचे जाळे बांधणे सुकर झाले. पिट्सबर्गजवळ कोक तयार करण्यास योग्य अशा बिट्युमेनयुक्त कोळशाचे साठे सापडल्याने लोखंड तयार करण्याचा खर्च आणखी कमी होण्यास मदत झाली. ट्रान्सॲपालॅचिअन रेल्वे प्रणाली वापरात आल्यावर लोहनिर्मितीचे केंद्र पश्चिमेकडे सरकले. नवीन धातुकाचे आणि कोळशाचे साठे सापडल्याने पेनसिल्व्हेनिया बरोबरच ओहायओ, इंडियाना व इलिनॉय या राज्यांत पुष्कळ लोह प्रगलन संयंत्रे प्रस्थापित झाली. १८५० मध्ये पिग लोखंडाचे उत्पादन सु. ५,६४,००० टनापर्यंत वाढले व ३७५ प्रगलन भट्ट्या कार्यान्वित होत्या. १८७४ मध्ये भट्ट्यांची संख्या ६८० पर्यंत वाढली आणि त्यांपैकी बहुसंख्य कोकचा वापर करीत होत्या पण २०० भट्ट्या १८७५ नंतरही अँथ्रॅसाइट कोळशाचा वापर करीत होत्या. १९४१ मध्ये चार अमेरिकन भट्ट्या खास उपयोगासाठी लागणारे अतिशय शुद्ध व गुधकमुक्त लोखंड मिळवण्यासाठी लोणारी कोळशाचा वापर करीत होत्या.
भट्टीत धातुक व कोळसा भरण्यासाठी यांत्रिक वाहकांचा उपयोग, पाण्याऐवजी वाफेचा व झोतभट्टीतील निरुपयोगी वायूचा हवाझोतनिर्मिती करणाऱ्या यंत्राला शक्ती पुरविण्यासाठी उपयोग, वाळूच्या साच्यात पिग लोखंड तयार करण्याच्या पद्धतीच्या जागी पिग लोखंडाचे ओतकाम करणाऱ्या यंत्रांचा उपयोग व कार्यक्षम नियंत्रण पद्धतींचा प्रारंभ यांमुळे मूळ स्ट्यूकोफेन भट्टीपासून आधुनिक झोतभट्टीपर्यंत झालेले संक्रमण पूर्ण झाले. १९१७ मध्ये अमेरिकेतील सर्वांत मोठी चालू झोतभट्टी दररोज ६४४ टन पिग लोखंड तयार करीत होती. तुलना करता १९४१ मध्ये १,३५० टन, तर १९६० नंतरच्या दशकाच्या अखेरच्या काळात १,५०० टनांहून अधिक पिग लोखंडाचे सर्वांत मोठ्या चालू भट्ट्या उत्पादन करीत होत्या.
पोलाद तयार करण्याच्या विविध पद्धतींचा तपशील व विकास ‘पोलाद’ या नोंदीत दिलेला आहे. येथे फक्त काही महत्त्वाच्या पद्धतींचा थोडक्यात ऐतिहासिक आढावा घेतलेला आहे. १८६० सालाच्या अगोदर पोलाद हे खर्चिक उत्पादन होते व ते अल्पप्रमाणातच तयार करीत. त्याचा उपयोग बहुशः हत्यारे व कटलरी तयार करण्यासाठी करीत असत. सर्व मोठ्या धातवीय संरचना घडीव लोखंडाच्या वा बिडाच्या बनविल्या जात. पोलादनिर्मिती शेफील्डमध्ये केंद्रित झालेली होती आणि तेथील उत्पादन यूरोपीय व अमेरिकन बाजारपेठांना पुरवठा करीत असत.
बेसेमर पद्धत व खुल्या चुल्याची पद्धत या इंग्लंडमध्ये झालेल्या दोन तांत्रिक प्रगतींमुळे १८६० नंतरच्या काळात उद्योगधंद्यांतील पोलादाच्या स्थानात खूप फरक पडला. बेसेमर पद्धतीत वितळलेले पिग लोखंड भट्टीतून बाहेर काढल्यावर त्यातून हवा फुंकून त्याचे पोलादात रूपांतर केले जाते. हवेच्या झोतामुळे पिग लोखंडातील कार्बन व सिलिकॉन जळून जातात आणि त्यामुळे वितळलेल्या धातूचे तापमान वाढते. हेन्री बेसेमर यांनी १८५६ मध्ये या पद्धतीचे प्रात्यक्षिक करून दाखविले व १८६४ पावेतो ती यशस्वीपणे कार्यान्वित केली. १८७० पावेतो बेसेमर पद्धतीने तयार केलेले पोलाद जहाजांच्या पत्र्यांसाठी व रेल्वेच्या रूळांसाठी विस्तृतपणे वापरात आले. साधारण १८९० नंतरच्या काळात बेसेमर पद्धतीची जागा हळूहळू सीमेन्स यांच्या खुल्या चुल्याच्या पद्धतीने घेतली आणि विसाव्या शतकाच्या मध्याच्या सुमारास बेसेमर पद्धत वापरात राहिली नाही.
बेसेमर पद्धतीत एका नासपतीच्या आकाराच्या पात्रात (परिवर्तकात) प्रक्रिया केली जाते. या पात्राला आतून उच्चतापसह (उच्च तापमान सहन करू शकणाऱ्या) विटांचे अस्तर असून त्याच्या तळात हवा फुंकण्यासाठी छिद्रे ठेवलेली असतात. प्रक्रिया करताना परिवर्तक कलंडवून त्यात कित्येक टन द्रवरूप पिग लोखंड भरतात. नंतर परिवर्तक उभा करून तळातून हवेचा झोत सुरू करतात.पिग लोखंडातील सिलीकॉनाचे ऑक्सिडीभवन होत असताना परिवर्तकाच्या तोंडाशी आखूड, सापेक्षतः मंद ज्योत दिसते व त्यानंतर कार्बनाचे ऑक्सिडीभवन होत असताना मोठी व तेजस्वी पिवळी ज्योत दिसते. या ज्योतीचे संकोचन प्रक्रिया जवळजवळ पूर्ण झाल्याचे दर्शविते. हवेचा झोत बंद करतात व परिवर्तक कलंडवून वितळलेले पोलाद बाहेर काढतात. या संपूर्ण प्रक्रियेला सु. १५ ते २० मिनिटे लागतात. चालकाला तिच्या प्रगतीचा अंदाज ज्योतीचा रंग व परिवर्तकात होणारे आवाज यांवरून करावा लागे. बेसेमर परिवर्तकातूत ओतल्या गेलेल्या पोलादात कार्बन अल्प प्रमाणात असे पण जोराने हवा फुंकल्यामुळे विरघळलेला बराच ऑक्सिजनही असे. घनीभवन होताना ऑक्सिजनाचे बुडबुडे बाहेर पडल्याने सदोष धातुपिंड तयार होण्याची शक्यता असे. याखेरीज इष्ट संघटन मिळविण्यासाठी सामान्यत: कार्बनाची भर घालावी लागे परंतु कार्बनाचे ऑक्सिडीभवन होऊ नये यासाठी विरघळलेला ऑक्सिजन काढून टाकल्याशिवाय कार्बनाची भर टाकणे शक्य होत नसे. बेसेमर पोलादातून ऑक्सिजन काढून टाकण्याची समस्या आर्.एफ् . मशेट यांनी सोडविली. यात परितर्वकातून ओतलेल्या पोलादात मँगॅनीज घालीत. विरघळलेल्या ऑक्सिजनाबरोबर त्याची विक्रिया होऊन अक्रिय मँगॅनीज ऑक्साइड बनते.
खुल्या चुल्याच्या पद्धतीचा प्रांरभ जर्मनीत सीमेन्स बंधूंनी भट्टीतून बाहेर पडणाऱ्या निरुपयोगी वायूतील उष्णतेचा उपयोग भट्टीत शिरणाऱ्या इंधनाच्या व हवेच्या पूर्वतापनासाठी केला तेव्हा झाला. १८६१ पावेतो सीमेन्स यांच्या पुनर्जनक भट्ट्या ब्रिटिश काच कारखान्यांत वापरात आल्या आणि विल्यम सीमेन्स यांनी पोलादनिर्मितीसाठी वायूच्या ज्वालेने तापविलेला खुला चुला उपयोगात आणण्याच्या दृष्टीने प्रयोग करण्यास प्रांरभ केला. १८६७ पर्यंत खुल्या चुल्यात पिग लोखंडापासून व लोह धातुकापासून पोलाद मिळविण्यात त्यांना यश मिळाले. त्याच वर्षी एमील व प्येअर मार् तँ यांनी फ्रान्समध्ये सीमेन्स भट्टी वापरून खुल्या चुल्यात घडीव लोखंड व लोखंडी मोड (भंगार) यांपासून चांगल्या दर्जाचे पोलाद तयार केले. सर्वसामान्य रूपातील खुल्या चुल्याच्या पद्धतीत पिग लोखंड, धातुक व मोड वापरण्यात येतात आणि ती सीमेन्स-मार्तँ पद्धती या नावाने ओळखण्यात येऊ लागली. या पद्धतीमुळे पोलादाच्या संघटनावर अधिक चांगले नियंत्रण ठेवता येऊ लागले व भट्टीत भरावयाच्या मालात भरपूर प्रमाणात मोडीचा समावेश करता येऊ लागाल. एस्.जी. टॉमस व पी. गिलख्रिस्ट यांनी १८७७ मध्ये चुनखडीच्या चूर्णाचा अस्तराकिरता उपयोग केल्यास पोलादातील फॉस्फरस काढून टाकता येतो, असा शोध लावला. या शोधामुळे वरील दोन्ही पद्धतींचा फायदा झाला आणि फॉस्फरसाचे उच्च प्रमाण असलेल्या धातुकांचाही पोलादनिर्मितीसाठी उपयोग करता येऊ लागला.
वरील शोधांमुळे स्वस्त पोलाद मोठ्या प्रमाणावर तयार करण्याकरिता आवश्यक असणारी तंत्रविद्या निर्माण झाली व ती जवळजवळ एका शतकाकरिता पोलाद उद्योगासाठी आधारभूत ठरली. उच्च गुणवत्तेची मिश्र पोलादे तयार करण्यासाठी विसाव्या शतकातही मूस प्रक्रिया महत्त्वाची राहिली. फ्रान्समध्ये पी.एल्.टी. एरू व स्वीडनमध्ये फेड्रिक केलीन यांनी १९०० साली पोलादनिर्मितीसाठी विद्युत् प्रज्योत भट्टीचा [⟶ पोलाद] उपयोग केला. त्यानंतरच्या वीस वर्षांतच खास प्रकारच्या पोलादांसाठी मूस प्रक्रियेच्या जागी विद्युत् भट्टीचा मोठ्या प्रमाणावर वापर होऊ लागला.
जगातील लोह धातुकांचे साठे : लोखंडाच्या धातुकांचे जागातील एकूण साठे बहुधा २०० अब्ज टनांहून जास्त असावेत. यात लोखंडाचे प्रमाण ३५ ते ६५ टक्क्यांपर्यंत (सरासरी ५०%) असून या धातुकांचा सध्याचा खप पहाता हे साठे २०० वर्षे पुरतील असा अंदाज करण्यात आलेला आहे. मात्र दुसऱ्या महायुद्धानंतर ज्या वेगाने हा खप वाढत आला तसाच तो वाढत राहिल्यास हेच साठे सु. १६० वर्षेच पुरू शकतील, असा अंदाज आहे. अर्थात खाणकाम, धातुकांवरील प्रक्रिया आणि वाहतूक यांची तंत्रे सुधारल्यास आता आर्थिक दृष्ट्या व्यवहार्य न वाटणारे साठेही फायदेशीर ठरू शकतील. मोठ्या मालवाहू जाहाजांमुळे धातुकांची वाहतूक कमी खर्चात होऊ लागल्याने पूर्वी दुर्लक्षित असलेले चीन, ब्राझील, लायबीरिया, पश्चिम ऑस्ट्रे लिया व रशिया येथील साठे काढणे शक्य झाले आहे.
जगातील लोह धातुकांच्या ज्ञात साठ्यांपैकी सु. २५% साठे रशियात, १५% ब्राझीलमध्ये, १३% भारतात, सु. १२% अमेरिकेच्या संयुक्त संस्थानांत आणि ७% कॅनडात आहेत. यांशिवाय ऑस्ट्रेलिया चीन, फ्रान्स, दक्षिण कोरिया, जर्मनी व आफ्रिकेतील काही देशही या दृष्टीने महत्त्वाचे आहेत.
जगात दरवर्षी विविध प्रकारची सु. ५५ कोटी टन लोह धातुके काढण्यात येतात. १९८५ च्या सुमारास यांपैकी २५% धातुके रशियात, १४% अमेरिकेत, ९.६% फ्रान्समध्ये, ६.४% चीनमध्ये व ६% कॅनडात काढण्यात येत असत. यांशिवाय स्वीडन, भारत, ब्राझील, व्हेनेझुएला, लायबीरिया,
कोष्टक क्र. १ लोह धातुकांचे विविध देशांतील उत्पादन (हजार टनांत)
आणि अंदाजित साठे (कोटी टनांत). |
||||
देश | उत्पादन | साठे | ||
१९७० | १९७५ | १९८० | (१९७०) | |
अमेरिकेची संयुक्त संस्थाने | ५३,३०८ | ४९,०४१ | ४४,५९२ | ४,१९२.५ |
ऑस्ट्रेलिया | २८,६७६ | ६०,८६० | ६१,३१९ | ७०५.७ |
कॅनडा | २९,१८७ | २७,६०९ | ३१,२८३ | १,०९७.० |
चीन | २४,००० | ३०,००० | ३७,५०० | २१३.० |
फ्रान्स | १७,७५९ | १५,३०९ | ९,१०० | ८०१.७ |
ब्राझील | २४,७३९ | ७३,५५० | ६०,५२८ | ३,७७५.७ |
भारत | १९,६५४ | २६,१४७ | २५,७४२ | १९१.६६ |
रशिया | १,०६,०५८ | १,२७,९३६ | १,३२,८८५ | — |
लायबीरिया | १४,४१८ | १३,५४३ | ११,९७२ | — |
व्हेनेझुएला | १४,०८० | १५,३५९ | १०,०५७ | २००.० |
स्वीडन | १९,८०४ | २०,८५६ | १७,३७१ | ३३७.० |
एकूण जागतिक | ४,२०,१२१ | ५,२०,६३५ | ५,०२,७४० | २०,०००.० |
ब्रिटन व ऑस्ट्रेलिया हे देशही लोह धातुकांच्या उत्पादनाच्या दृष्टीने महत्त्वाचे आहेत. लोह धातुकांची आयात करणारे प्रमुख देश व तेथे आयात करण्यात येणाऱ्या धातुकांचे शेकडा प्रमाण असे आहे : फ्रान्स १५, अमेरिका ३६, ब्रिटन ५६, जर्मनी ८४, जपान ९२ आणि इटली ९३. कोष्टक क्र.१ मध्ये विविध देशांतील धातुकांचे उत्पादन व साठे दिलेले असून त्यानंतर जगातील प्रमुख देशांतील धातुकांच्या साठ्यांची थोडक्यात माहिती दिली आहे.
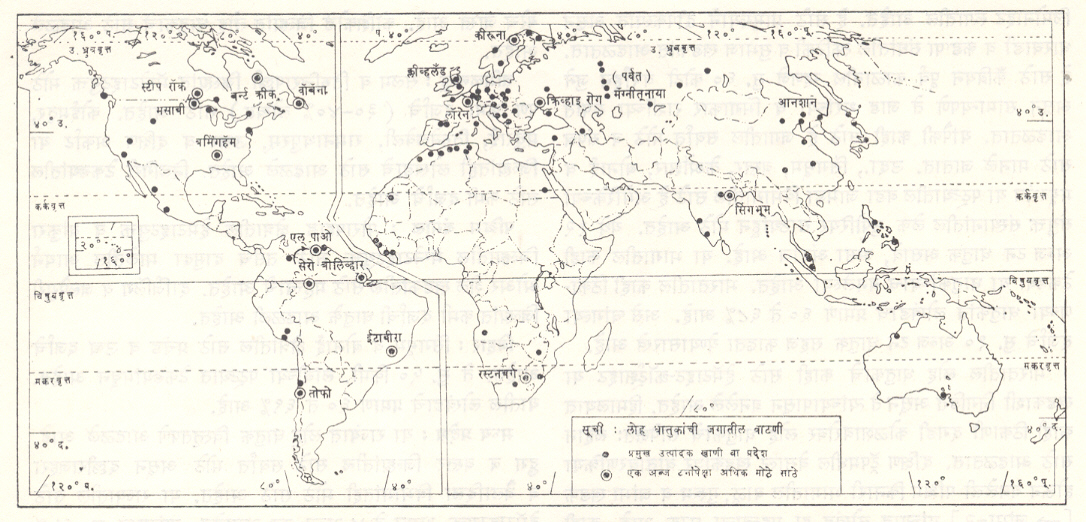
आ.२ मध्ये जगातील लोह धातुकाचे १ अब्ज टनांपेक्षा जास्त साठे असलेले प्रदेश व प्रमुख लोह धातुक उत्पादक खाणी व प्रदेश दाखविलेले आहेत.
अमेरिकेची संयुक्त संस्थाने : या देशातील सर्व राज्यांत लोखंडाची धातुके आढळतात. येथील साठे पुढील चार प्रमुख विभागांत आहेत : लेक सुपीरिअर सरोवर प्रदेश (७०%), ईशान्य भाग (८%), आग्नेय भाग (५%) आणि पश्चिमेकडील राज्ये (४.५%).
कॅनडा : १९४० च्या सुमारास येथील लोह धातुकांचे उतपादन नगण्य होते. १९८५ च्या सुमारास मात्र ते ४.६२ कोटी टनांइतके वाढले.
ब्राझील : येथील साठे दुर्गम भागात आहेत. १९४० पासून येथील उत्पादनात वाढ होत आहे. येथील एका पर्वताकडे वीज आकर्षिली जाते व तेथील धातुकात ५८% लोखंड आढळते. येथील बहुतेक धातुक पूर्वी अमेरिकेची संयुक्त संस्थाने व पश्चिम जर्मनीला निर्यात होई. आता या देशाने स्वतःचा लोखंड व पोलाद उद्योगही सुरू केला आहे.
व्हेनेझुएला : येथे काढण्यात येणाऱ्या धातुकांपैकी ९६% धातुकांची निर्यात होते व त्यांपैकी ७३% निर्यात अमेरिकेच्या संयुक्त संस्थानांना होते.
पेरू : येथील लोह धातुकांच्या खाणी किनारी भागात असून तेथे धातुकाच्या गुलिका (लहान गोलाकार व दंडगोलाकार गोळ्या) बनवितात. या संयंत्राची गुलिका बनविण्याची वार्षिक क्षमता २० लाख टन आहे.
चिली : येथील लोह धातुकांचे साठे सु. ५२.५ कोटी टन आहेत. धातुकांचे शुद्धीकरण व गुलिकांत रूपांतर करून मग ते मुख्यत्वे (सु. ६५%) जपानला पाठवितात.
रशिया : कुर्स्क (मॅग्नेटाइट), दक्षिण भाग (हेमॅटाइट), उरल प्रदेश, मध्य रशिया, कॉकेशस प्रदेश व पोलंडलगतचा भाग येथे लोह धातुकांचे मुख्य साठे आहेत. १९४५ पासून येथील धातुकांच्या उत्पादनात वाढ होत आहे. आता येथे कमी दर्जाच्या (२७% लोखंड) धातुकाचे शुद्धीकरण करून त्यातील लोखंडाचे प्रमाण ६० टक्क्यांपर्यंत वाढविण्यात येते. १९८५ पासून येथे दरवर्षी १६ कोटी टन धातुके काढण्यात येत आहेत.
फ्रान्स : येथे अंदुकी लोह धातुकांचे अनेक थर आहेत. लॉरेन जिल्ह्यातील साठे महत्त्वाचे आहेत.
स्वीडन : येथे १३०० सालापासून लोह धातुक खणून काढण्यात येत असून १९६५ च्या सुमारास येथील उत्पादन २.९ कोटी टन होते. येथील धातुकात फॉस्फरसाचे प्रमाण जास्त आहे. काही प्रमाणात हा देश लोह धातुक आयातही करतो.
ब्रिटन : आता येथे कमी दर्जाची (२७% लोखंड) धातुके उरली आहेत व उत्पादनही घटले आहे. यामुळे येथे दरवर्षी १.८ कोटी टन धातुकांची आयात केली जाते.
चीन : येथे दरवर्षी ३.५ ते ४ कोटी टन लोह धातुके काढली जातात. येथील धातुकांत लोखंडाचे प्रमाण २६ ते ६५% (सरासरी ५०%) आहे.
ऑस्ट्रेलिया : १९६५ साली येथील धातुकांचे उत्पादन ६७ टन एवढे नाममात्र होते. नंतर हे उत्पादन वाढत जाऊन १९९२ पर्यंत धातुकांचे उत्पादन करणारा हा एक प्रमुख देश बनला आहे. येथील धातुकांत ५४ ते ५९% लोखंड आढळते.
पश्चिम आफ्रिका : येथील उच्च दर्जाच्या धातुकांचे उत्पादन १९५० नंतर वाढत गेलेले आढळते. लायबीरिया व मॉरिटेनिया हे या भागातील प्रमुख उत्पादक देश असून तेथे १९६३ पासून धातुके काढण्यास सुरुवात झाली. येथे दरवर्षी सु. ६० लाख टन धातुके काढण्यात येतात. ती मुख्यत्वे अमेरिकेची संयुक्त संस्थाने, फ्रान्स, ब्रिटन व इटली या देशांना निर्यात होतात.
जपान : येथे दरवर्षी फक्त १० लाख टन लोह धातुके काढण्यात येतात आणि देशाची बहुतेक गरज आयातीचे (दरवर्षी ४ कोटी टन) भागविली जाते. पोलादनिर्मितीच्या बाबतीत या देशाचा जगात तिसरा क्रमांक आहे.
भारतातील लोहधातुकांचे साठे : भारतात लोह धातुकांचे साठे सु. १९.१६६ अब्ज टन असून ते मुख्यत्वे हेमॅटाइट (१३.०६६ अब्ज टन) आणि मॅग्नेटाइट (६ अब्ज टन) व थोडे लिमोनाइट रूपातील आहेत. हे साठे प्रामुख्याने द्वीपकल्पात असून धारवाडी व कडप्पा संघांतील स्फटिकी व सुभाज खडकांत आढळतात. हे साठे कँब्रियन पूर्व काळातील म्हणजे सु. ६० कोटी वर्षांहून जुने असून सामान्यपणे ते जाड थरांच्या व भिंगाकार राशींच्या रूपांत आढळतात. यांपैकी काही साठे हे जगातील सर्वांत मोठे व संपन्न साठे मानले जातात. उदा., सिंगभूम, बस्तर, केओंझार, बोनाई व मयूरभंज या पट्ट्यातील बडा जाभडा विभागातील साठे हे अमेरिकेच्या संयुक्त संस्थानांतील लेक, सुपीरियर साठ्यांहून मोठे आहेत. येथे १२ अब्ज टन धातुक असावे, असा अंदाज आहे. या भागातील काही टेकड्या या धातुकांच्याच बनलेल्या आहेत. भारतातील काही ठिकाणच्या धातुकांत लोखंडाचे प्रमाण ६० ते ६८% आहे. असे चांगल्या दर्जाचे सु. १० अब्ज टन धातुक सहज काढता येण्यासारखे आहे.
भारतातील लोह धातुकाचे काही साठे हेमॅटाइट-क्वॉर्ट्झाइट या खडकाशी निगडित असून ते त्यांच्यापासून बनलेले आहेत. हिमालयात काही ठिकाणी दगडी कोळशाबरोबर लोह धातुकांचे सापेक्षतः लहान साठे आढळतात. दक्षिण ट्रॅपमधील बेसाल्ट खडकावर वातावरणक्रिया होऊन बनलेली पश्चिम किनारी भागातील वाळू, मुरूम व जांभा खडक [⟶ जांभा -२] यांच्यात लोखंड हा महत्त्वाचा घटक आहे. काही मुरुमांतील लिमोनाइटाचे वा हेमॅटाइटाचे प्रमाण बरेच जास्त असलेले आढळते. आयर्न ओअर माला ही चांगल्या दर्जाचे लोह धातुक असून प. बंगालमधील दामुदा मालेच्या आयर्न स्टोन शेल खडकांतही मोलाचे धातुक साठे आहेत. राणीगंज क्षेत्रातील आयर्न स्टोन शेल खडकांतील लोह धातुक कमी दर्जाचे (४० ते ४५% लोखंड) असून त्याचा उपयोग गौण धातुक म्हणून होतो. भारतातील लोह धातुकांच्या काही महत्त्वाच्या साठ्यांची माहिती पुढे राज्यानुसार दिली आहे.
आंध्र प्रदेश : या राज्यात धारवाडी क्वॉर्ट्झाइट तसेच कडप्पा संघातील वालुकाश्म व क्वॉर्ट्झाइट व खडकांत हेमॅटाइटयुक्त धातुक आढळते. मुख्यत: खम्मामेट. कडप्पा व अनंतपूर या जिल्ह्यात धातुक काढण्यात येते. हे धातुक कमी दर्जाचे असल्याने ते समृद्धीकरणानंतर वापरतात. चित्तूर, नेल्लोर, करीमनगर, वरंगळ व अदिलाबाद जिल्ह्यांतील धारवाडी संघाच्या खडकांतही अशा प्रकारचे हेमॅटाइट व मॅग्नेटाइटयुक्त साठे आढळले आहेत.
ओरिसा : येथील साठे हेमॅटाइटयुक्त व उच्च दर्जाचे (५५ ते ६८% लोखंड) व २.२५ अब्ज टनांहून जास्त असावेत. सुंदरगढ, मयूरभंज, कटक, संबळपूर व कोरापुट हे जिल्हे तसेच केओंझार क्षेत्र येथील साठे सर्वाधिक महत्त्वाचे आहेत. येथील धातुक पारादीप बंदरातून जपानला पाठविण्यात येते.
कर्नाटक : या राज्यात लोह धातुक विस्तृत क्षेत्रात आढळते. मंगलोरजवळच्या किनारी भागातून उच्च दर्जाचे धातुक जपानला निर्यात होते. बाबाबुढण टेकड्या (केमेनगुडी व चिकमंगळून जिल्हे), कुद्रेमुख व बळ्ळारी-होपसेट क्षेत्रांतील साठे उच्च दर्जाचे आहेत. बाबाबुढण टेकड्यांतील साठे जवळजवळ हेमॅटाइटाचे बनलेले असून त्यात थोडे मॅग्नेटाइट आहे. यातील लोखंडाचे प्रमाण ५०-६०% आहे. बळ्ळारी – होसपेट विभागातील साठेही मुख्यत्वे हेमॅटाइटयुक्त असून काही ठिकाणी त्यांच्यात ६० ते ६५% लोखंड आढळते. ४० ते ५०% लोखंड असलेले मॅग्नेटाइट-क्वॉर्ट्झाइटाचे साठे मंड्या जिल्ह्यात आढळले आहेत तर सारगळ, कुनीगळ, हरियुर व शंकरगुड्डा या जिल्ह्यांत कमी दर्जाची धातुके आढळली आहेत.
केरळ : एर्नाकुलम (५५% लाहयुक्त), त्रिचू र (३० ते ४०% लोहयुक्त) व कन्नानोर या जिल्ह्यांतील मुरुमांत लोखंडाचे प्रमाण बरेच जास्त आहे. कोझिकोडे जिल्ह्यांत लोह धातुकाचे साठे आढळले आहेत.
तमिळनाडू : सेलम व तिरुचिरापल्ली जिल्ह्यांत मॅग्नेटाइटयुक्त मोठे पण कमी दर्जाचे (३०–४०% लोखंड) साठे आहेत. कोईमतूर, मदुराई, तिरुनेलवेली, रामनाथपुरम्, उत्तर व दक्षिण अर्काट या जिल्ह्यांतही लोखंडाचे साठे आढळले आहेत. निलगिरी टेकड्यांतील साठे कमी दर्जाचे आहेत.
पश्चिम बंगाल : पोरापहाड क्षेत्रातील हेमॅटाइटयुक्त व बांकुरा जिल्ह्यातील मॅग्नेटाइटयुक्त साठे तसेच दामुदा मालेतील आयर्न ओअर शेल खडकांतील साठे महत्त्वाचे आहेत. दार्जिलिंग व जलपैगुरी जिल्ह्यांत कमी दर्जाची धातुके आढळली आहेत.
बिहार : सिंगभूम व बोनाई क्षेत्रांतील साठे प्रचंड व उच्च दर्जाचे आहेत. ते सु. ५० किमी. लांबीच्या पट्ट्या त टेकड्यांमधून आहेत. यातील लोखंडाचे प्रमाण ६० ते ६९% आहे.
मध्य प्रदेश : या राज्यात लोह धातुक विस्तृतपणे आढळले आहे. द्रुग व बस्तर जिल्ह्यांतील साठे सर्वांत मोठे असून दल्लीराजहरा व बैलादिला विभागांतही मोठे साठे आहेत. या राज्यातील साठे हेमॅटाइटयुक्त असून ते ४ अब्ज टन असावेत. त्यांच्यात सु. ६५% लोखंड आढळते. हेमॅटाइटयुक्त साठे निमाड व हुशंगाबाद जिल्ह्यांत, तर हेमॅटाइट व मॅग्नेटाइटयुक्त साठे नरसिंगपूर जिल्ह्यात सापडले आहेत. यांशिवाय सागर, ग्वाल्हेर, घार, मंदसोर व रायगड जिल्ह्यांतही ही धातुके सापडली असून कटनी, बिजोरी व जबलपूर जिल्ह्यांत मुरुमाच्या रूपातील धातुके आहेत.
महाराष्ट्र : चंद्रपूर व गडचिरोली (लोहारा, मसोली, देवळगाव, पिंपळगाव, रतनपूर व बिस्सी), रत्नागिरी आणि सिंधुदुर्ग (रेडी, सातेली, आरोस, तेंडोली व खानोली) आणि भंडारा (खुरसियार) जिल्ह्यांत लोह धातुकांचे साठे असून महाराष्ट्रात चांगल्या दर्जाच्या धातुकांचे साठे सु. ५ कोटी टन असावेत. गौण धातुके विस्तृतपणे पसरलेली आहेत. चंद्रपूर व गडचिरोली जिल्ह्यांतील धातुकांत लोखंडाचे प्रमाण ६१ ते ७१% आहे. यांशिवाय नागपूर जिल्ह्यांत हेमॅटाइटयुक्त साठे ओत. तसेच रत्नागिरी, सिंधुदुर्ग, रायगड, कोल्हापूर व सातारा या जिल्ह्यांत लोखंडाचे जास्त प्रमाण असलेला मुरूम व जांभाही आढळतो. अर्थात सध्या हे साठे फायदेशीर ठरू शकणार नाहीत.
वरील राज्यांव्यतिरिक्त भारतात आसाम (खांसी टेकड्यांतील हेमॅटाइट-क्वॉर्ट्झाइट), उत्तर प्रदेश (गढवाल व मिर्झापूर जिल्हे), गोवा, पंजाब (कमी दर्जाचे छोटे साठे), राजस्थान (अल्वर, बुंदी, जयपूर व उदयपूर जिल्ह्यांतील मध्यम आकारमानाचे साठे), हिमाचल प्रदेश (कुमाऊँ, रियासी जिल्ह्यांतील लहान साठे) इ. प्रदेशांतही लोहधातुके सापडली आहेत.
भारतात मुख्यत्वे बिहार, गोवा, कर्नाटक, मध्य प्रदेश, महाराष्ट्र व ओरिसा येथे लोह धातुकांचे खाणकाम चालते. आंध्र प्रदेश व राजस्थान येथे थोडे धातुक काढतात. भारतातील लोह धातुकांचे १९७०, १९७५ व १९८० सालचे उत्पादन कोष्टक क्र.१ मध्ये दिले आहे. १९८४ साली हे उत्पादन ४२,३१०; १९८६ साली ५१,६१० आणि १९८८ साली ५२,३२२ हजार टन झाले होते. गोवा, विशाखापटनम् व पारादीप या बंदरांतून लोह धातुकांची मोठ्या प्रमाणावर सु. २० देशांना निर्यात होते. १९८१ – ८२ साली ३४.३४ कोटी टन धातुकाची निर्यात झाली होती.
कर्नाटकातील कुद्रेमुख येथील साठा ६१ कोटी टन असून ही धातुके मॅग्नेटाइट-हेमॅटाइटयुक्त आहेत. येथील धातुके मुख्यत्वे इराणला निर्यात करण्याचा करार झाला होता. मात्र १९७९ साली इराणमधील राजकीय सत्तेत बदल झाल्याने हा करार प्रत्यक्षास येऊ शकला नाही. त्यामुळे येथील काही धातुक बहारीन, रूमानिया इ. अन्य देशांना निर्यात होते. इराणमधील प्रकल्प पूर्ण झाल्यावर कदाचित या कराराला परत उजाळा मिळण्याची शक्यता आहे. येथील धातुके समृद्धीकरणासाठी राळ्याच्या रूपात ६७ किमी. अंतरावरील मंगळूर बंदरात नळांतून पाठविण्यात येतात. येथे त्यांचे गुलिकांत रूपांतर करण्यात येते. येथील संयंत्रात दरवर्षी ३० लाख टन गुलिका बनविण्याची सोय आहे.
धातुकाचे खाणकाम : लोह धातुक (मुख्यत्वे ऑक्साइड रूपात) बऱ्याचदा भूपृष्ठाच्या पुरेसे लगत व मलद्रव्यांबरोबर सैलसर संयोग झालेले आढळत असल्याने ते उघड्या खाणकाम पद्धतीने काढता येते. दुसरे टोक म्हणजे धातुक भूपृष्ठाखाली कित्येक मीटर खोलीवरील खडकांत पुरलेले आढळते. एखाद्या धातुक निक्षेपाचे (साठ्याचे) आकारमान, त्याची सापेक्ष शुद्धता व लोहाचा अंश, त्याचे भौगोलिक स्थान व अनेक आर्थिक बाबी यांवर त्याच्या खाणकामाची सुसाध्यता ठरते. प्रारंभीचे लोह प्रगलन भूपृष्ठालगत सापडणाऱ्या धातुकावर अवलंबून होते आणि प्रगलन क्रिया असंस्कारित धातुकाच्या जवळपास करण्यात येत असल्याने त्याचे उपयुक्त लोखंडात प्रगलन करणे सापेक्षतः सोपे होते. आता धातुक हजारो किमी. अंतरावर वाहून नेले जात असल्याने व पुष्कळच स्पर्धात्मक परिस्थिती निर्माण झालेली असल्याने खाणकामात व प्रगलन क्रियेत अतिशय जटिल तंत्रांचा उपयोग करणे आवश्यक झाले आहे.
पूर्वेक्षण : प्रारंभीच्या पूर्वेक्षणाच्या काळात धातुक राशीचा ठावठिकाणा लावण्याच्या पद्धती भूप्रदेशाच्या भौतिक बाह्य स्वरूपाशी निगडित होत्या. तांबड्या मातीचा खनिज निक्षेप सापडण्याच्या शक्यतेशी संबंध जोडला जाऊ लागला. निळा शैलसमूह हाही सराईत पूर्वेक्षकाला एक खनिज निर्देशक होता. अमेरिकेतील सुपीरिअर सरोवराजवळील विस्तीर्ण धातुकस्तराचा शोध जमिनीच्या वर आलेल्या धातुक निक्षेपाच्या दृश्य थरामुळे लागला. ॲलबॅमातील सुप्रसिद्ध तांबड्या धुळीमुळे तेथील हेमॅटाइटयुक्त मातीचा शोध लागला.
भूमिगत निक्षेपातील लोहाच्या अंशामुळे भूचुंबकीय क्षेत्रात बदल होतात. या आविष्कारामुळे विविध प्रकारच्या नतिसूचींचा (उभ्या प्रतलात फिरू शकणारी चुंबकीय सूची असलेल्या चुंबकीय क्षेत्रमापकांचा) मॅग्नेटाइट निक्षेपांच्या स्थान-निर्धारणासाठी विकास झाला. सामान्य दिक्सूचकासारख्याच (होयकायंत्रासारख्याच) असलेल्या या नतिसूचींचा धातुकस्तरांचे स्थान आणि विस्तार ठरविण्यासाठी उपयोग करण्यात आला. पूर्वेक्षण पद्धती अधिक सुविकसित झाल्यावर आणि अधिक सहजपणे स्थान-निर्धारण करता येणाऱ्या स्तरांचे सर्वेक्षण करून नकाशे तयार करीत असतानाच नवीन स्थान-निर्धारक प्रयुक्ती विकसित करण्यात आल्या. ⇨चुंबकीय क्षेत्रमापक ही अतिशय अचूक चुंबकीय प्रणाली असून तिच्या साहाय्याने भूचुंबकीय क्षेत्राच्या उभ्या घटकाची तीव्रता व चुंबकीय द्रव्यांच्या स्थानिक संकेद्रणांचा तीवर होणारा परिणाम हे मोजता येतात. विमानातून चुंबकीय क्षेत्रमापकाच्या साहाय्याने जमिनीवरील सर्वेक्षणापेक्षा खूप मोठ्या क्षेत्राचे अत्यल्प काळात सर्वेक्षण करता येते. [⟶ खनिज पूर्वेक्षण].
चुंबकीय सर्वेक्षणानंतर भूभौतिकीय गणनक्रियेने निक्षेपाचा विस्तार, नती व सापेक्ष धातुक प्रमाण निर्धारित करतात. त्यानंतर चाचणी छिद्रणाने खडकांचे वरवंट्यासारखे आंतरक नमुने मिळवितात. या नमुन्यांवरून मिळालेल्या माहितीच्या आधारे धातुक राशीचा सुनिश्चित आकार, आकारमान व दर्जा निर्धारित करतात.
सुसाध्यता : प्राथमिक सर्वेक्षणे पूर्ण केल्यावर धातुकाचे खाणकाम आर्थिक दृष्ट्या परवडेल की नाही हे निर्धारित करण्यासाठी सुसाध्यता अभ्यास करतात. यात अनेक बाबी विचारात घ्याव्या लागतात. निक्षेपाची भौगोलिक व भूवैज्ञानिक स्थाने महत्त्वाची असतात. उदा., सुपीरिअर सरोवरानजीकच्या धातुक निक्षेपांची यशस्वीपणे समुपयोजन करता आले, कारण सरोवरावरील स्वस्त वाहतूक प्रणाली व उघड्या खाणकाम पद्धती वापरणे शक्य झाले. याउलट दक्षिण अमेरिकेतील समृद्ध धातुक निक्षेप फार दूरच्या स्थानी आहेत. धातुकातील लोखंडाचे प्रमाण निष्कर्षण खात्रीने करता येईल इतके पुरेसे उच्च असले पाहिजे. धातुकातील लोखंडाचे प्रमाण कमी असल्याच्या कारणास्तव अनेक कमी दर्जाचे निक्षेप सर्वेक्षण व अभ्यास केल्यावर खाणकाम न करताच सोडून देण्यात आलेले आहे. धातुकातील मलद्रव्यांचे प्रमाण निरुपयोगी मालाची अत्याधिक हाताळणी टाळकण्याइतके व प्रगलन क्रियेत अतिभार येणार नाही इतके कमी असले पाहिजे. बहुतेक यूरोपीय धातुकांत फॉस्फरसाचे प्रमाण उच्च असते व त्याचे धातुकाबरोबर क्षपण होत असल्याने अमेरिकेतील भट्ट्यांत ही धातुके वापरता येत नाहीत. तांबे व कथिल यांची फॉस्फरसाप्रमाणे विक्रिया होते. मॅग्नेशिया व ॲल्युमिना यांचे झोतभट्टीत क्षपण होत नाही. सिलिकेचे फक्त अंशतः क्षपण होते. धातुकाची भौतिक स्थिती मऊ माती ते ग्रॅनाइटासारखी कठीण असण शक्य असते व तिच्यामुळे प्रगलन क्रियेत बऱ्याच अडचणी निर्माण होण्याची शक्यता असते. जर धातुक फार मऊ असेल, तर झोतभट्टी चोंदून राहू नये म्हणून धातुकाच्या गुलिका तयार कराव्या लागतात अथवा त्याचे तापपिंडन (न वितळविता तापवून गोळे तयार करणे) करावे लागते. जर धातुक फार घट्ट असेल, तर झोतभट्टीत त्याची क्षपणक वायूंशी चांगल्या प्रकारे विक्रिया होऊ शकत नाही. आणि सजल धातुकांत अत्यधिक उच्च जलांश असल्यामुळे वाहतूक खर्च वाढतो आणि प्रगलन क्रियेत जादा ऊर्जा खर्च करावी लागते.
खाणकाम पद्धती : सुसाध्यता अभ्यास पूर्ण केल्यावर धातुक काढून घेण्याच्या पद्धती ठरवाव्या लागतात. उघड्या खाणकामाची पद्धत सर्वांत काटकसरीची असून ती जगातील बहुतेक खाणींत वापरतात. जर निक्षेप सापेक्षतः सपाट व भूपृष्ठालगत नसतील, तर पुष्कळच अधिक खर्चिक अशी भूमिगत खाणकाम पद्धत वापरावी लागते.
उघड्या खाणकामात निक्षेपावरील दगडगोटे व माती शक्तिशाली फावड्यांनी काढून टाकली जातात. नंतर रूळ घातले जातात व धातुक गाड्यांमध्ये भरून मध्यवर्ती ठिकाणी गोळा करतात आणि रूळमार्गे व जलमार्गे अन्यत्र पाठवितात. जसजसे खाणकाम अधिकाधिक खोल जाऊ लागते तसतसे रूळ खालच्या पातळीत पुन्हा घातले जातात आणि ही क्रिया उघडे खाणकाम करण्यास अवघड होईल इतकी खड्ड्याची खोली पोहोचेपर्यंत चालू ठेवतात. त्या स्थितीत जर अद्यापही धातुक निक्षेप खणून काढणे आर्थिक दृष्ट्या परवडण्यासारखे असेल, तर भूमिगत खाणकामाच्या पद्धती वापरतात.
भूमिगत खाणकामात धातुक निक्षेपांच्या लगत उभे कूपक तयार करतात. या कूपकांतून निक्षेपाच्या निरनिराळ्या पातळ्यांमध्ये पोहोचतील असे आडवे बोगदे तयार करतात. छिद्रण, उत्स्फोटन, पाणी काढून टाकणे, मुक्तपणे हालचाल करण्यावरील मर्यादा यांसारख्या विविध समस्यांमुळे भूमिगत खाणकामाचा खर्च उघड्या खाणकामापेक्षा अनेक पट असतो. [⟶ खाणकाम].
धातुकांचे समृद्धीकरण : यात खाणीतून काढलेल्या मालातील शुद्ध धातुकाचे प्रमाण वाढविण्यासाठी त्यावर चुरडणे, प्रतवारीकरण, धुलाई, संकेंद्रण, संमिश्रण व संपिंडीकरण ही संस्करणे करण्यात येतात. धातुक उत्पादनाच्या प्रारंभीच्या काळात अशा संस्करणांची आवश्यकता नव्हती, कारण बहुतेक धातुके सरळ उपयोग करण्याच्या प्रकाराची होती आणि कमी इष्ट वाटणारी धातुके वर्ज्य करीत; परंतु नंतर धातुकावरील समृद्धीकरण हा वाढत्या महत्त्वाचा टप्पा झालेला आहे. धातुकांच्या भौतिक व रासायनिक गुणधर्मानुसार (या गुणधर्मांत खाणक्षेत्रामध्ये सर्वत्र पुष्कळच फरक असण्याची शक्यता असते) व ग्राहकाच्या विशिष्ट गरजांनुसार धातुकांचे खाणीजवळ वा ते गोळा करण्याच्या केंद्रांत समृद्धीकरण करण्यात येते.
धातुक निक्षेपांच्या स्थानापासून निरुपयोगी माल वाहून नेण्याचा खर्च कमीत कमी ठेवला जातो. कच्च्या धातुकाचे जवळजवळ एक तृतीयांशापर्यंत वजन प्रतवारीकरणात व इतर संस्करणात कमी होण्याची शक्यता असते. मलद्रव्ये प्रगलन क्रियेत काढून टाकण्यापेक्षा यांत्रिक पद्धतींनी काढून टाकणे पुष्कळच सुलभ व खूप कमी खर्चाचे असते.
एकसारख्या भौतिक व रासायनिक संघटनांची खात्री करण्यासाठी निरनिराळ्या गुणधर्मांची धातुके एकत्र मिसळतात. यामुळे मलद्रव्यांवर सतत नियंत्रण राहते व भौतिक पद्धतींनी काढून टाकण्यात अवघड असलेल्या मलद्रव्यांचे परिणाम किमान राहते. संमिश्रण क्रियेमुळे गंधक, फॉस्फरस, सिलिकॉन, क्रोमियम व मँगॅनीज संयुगे यांसारख्या मलद्रव्यांचे प्रमाण सह्य पातळीवर राहते. पूर्वी प्रगलन समस्यांमुळे निरूपयोगी ठरविण्यात आलेल्या सूक्ष्मकणी द्रव्यांचे मूल्य वाढविण्यासाठी त्यांचे तापपिंडन करतात अथवा ठोकळे वा गुलिका बनवितात.
आकारमान लघुकरण : लोह धातुकाच्या समृद्धीकरणातील ही पहिली पायरी असून तीत विविध चुरडण्याच्या व दलनाच्या क्रियांचा समावेश होतो. खाणीतून काढलेले धातुक प्रचंड ठोकळ्यांपासून सूक्ष्मकणांपर्यंतच्या निरनिराळ्या आकारमानांचे असते आणि त्यात खडक व लोखंडाचे अल्प प्रमाण असलेली इतर द्रव्ये असतात. दृक् परीक्षण व अलगीकरण केल्यावर क्रमाक्रमाने चाळणक्रिया करून मलद्रव्यांचे प्रमाण कमी करतात आणि त्यामुळे धातुकाचे आकारमान प्रमाणभूत विनिर्देशाइतके (काही धातुक प्रकारांच्या बाबतीत सूक्ष्म चूर्णापर्यंत) कमी होते.
संमिश्रण : निरनिराळ्या गुणधर्मांची धातुके वेगवेगळ्या खाणीतून काढून आणल्यावर किंवा चुरडण्याच्या व चाळण्याच्या क्रिया केल्यावर संमिश्रण करता येते. या दोन्ही पद्धतींत धातुकांच्या राशी आडव्या स्तरांत रचतात. प्रत्येक स्तराला स्वतः चे वेगळे गुणधर्म असतात. नंतर स्तरित राशीतून धातुक काढून घेण्यासाठी एका दाताळ्याने राशीचा उभा छेद करतात व त्याने धातुक वाहक पट्ट्यावर काढून घेतले जाते. यामुळे अनेक स्तरांचे जवळजवळ पूर्णतः संमिश्रण होते.
धुलाई : ही एक संकेंद्रण क्रिया असून तीत पाण्याचा उपयोग करून धातुकातील वाळूचे व मातीचे कण पाण्यात संघारित करतात (लोंबकळत्या स्थितीत ठेवतात) व धुलाई यंत्रातून बाहेर वाहून नेले जातात. जड धातुक तळाशी बसते व मग ते तेथून काढून घेतले जाते. या क्रियेत लोह धातुक व मलद्रव्ये यांच्या विशिष्ट गुरुत्वांतील फरकाचा फायदा घेण्यात येतो. कमी दर्जाच्या धातुकाचे संकेंद्रण करण्यासाठी धुलाई क्रिया विशेष उपयोगी पडते. धातुकाच्या प्रकारानुसार व स्थानिक बाबींनुसार निराळ्या प्रकारात स्पंदनशील (वरखाली हालचाल होणारी) जल प्रणाली वापरून धातुकातील घटक स्तर रूपात अलग केले जातात. या प्रक्रियेत मलद्रव्ये सर्वांत वरच्या थरात जातात व धुलाई प्रयुक्तीतून (जिगमधून) ओसंडून बाहेर जाऊ देतात. जड लोह संपन्न घटक जिगच्या तळावर बसतात व ते काढून घेतले जातात.
जड माध्यमाद्वारे विलगीकरण : धातुकातील घटकांच्या विशिष्ट गुरुत्वातील सापेक्ष फरकांचा उपयोग करणारी एक अधिक सुविकसित पद्धत १९३७ च्या सुमारास वापरात आली आहे. या पद्धतीत आयर्न ऑक्साइड व सर्वांत सामान्य मलद्रव्य खनिज (सिलिका) यांच्या दरम्यान विशिष्ट गुरुत्व असलेला जड द्रव वापरतात. हलकी मलद्रव्ये द्रवाच्या वर तरंगतात, तर जड असलेले धातुक बुडते. कार्यक्षमता सुधारण्यासाठी माध्यमात चुंबकीय द्रव्य (सामान्यतः फेरोसिलिकॉन) वापरल्यास ही पद्धती विशेषत्वाने धुलाई यंत्रात निरुपयोगी मलद्रव्यांमध्ये पूर्वी वाया जात असलेली वा इतर कोणत्याही प्रकारे उपयोगात आणण्यात न येणारी अतिशय सूक्ष्मकणी ऑक्साइडे परत मिळविण्यासाठी उपयुक्त ठरते.
प्लवन क्रिया : संकेंद्रणाची ही क्रिया धुलाई व जिगिंग यांपेक्षा अधिक खर्चिक आहे. कारण तीत धातुक बारीक दळणे आवश्यक असते. बारीक दळलेले धातुक संधारित केलेल्या द्रवात योग्य रसायने घालून बुडबुडयांची एक प्रणाली (फेन) तयार करण्यात येते. धातुकातील मलद्रव्ये किंवा खनिज बुडबुड्यांकडे निवडकपणे आकर्षित होतात व प्रणालीतून काढून घेतले जातात. [⟶ प्लवन].
चुंबकीय विलगीकरण : मॅगनेटाइटाचे मलद्रव्यांपासून चुंबकीय विलगीकरण करण्याची पद्धत तत्त्वतः समृद्धकीरणाची सर्वांत सोपी पद्धत आहे. निरनिराळ्या द्रव्यांची चुंबकीय प्रवणता [⟶ चुंबकत्व] निरनिराळ्या मूल्यांची असते, या वस्तुस्थितीचा आधार घेऊन बारीक दळलेल्या मॅग्नेटाइट धातुकाचे द्रवातील (पाण्यातील) संधारण चुंबकाच्या एका प्रणालीच्या प्रभावाखाली आणण्यात येते. विलगक यंत्राच्या अभिकल्पानुसार (आराखड्यानुसार) पट्टे वा फिरते दंडगोल वापरण्यात येतात आणि विद्युत् चुंबकीय व चिरचुंबकीय अशा दोन्ही प्रणाली विलगक यंत्राचे क्रियाशील भाग असतात.
चुंबकीय विलगक यंत्र वापरण्यातील मुख्य अडचण म्हणजे द्रवातील संधारणातील चुंबकीय धातुकाच्या बारीक सूक्ष्म कणांमध्ये अडकले गेलेले अचुंबकीय कण काढून टाकण्याची आहे. चुंबकीय विलगकाच्या नंतर विकसित झालेल्या प्रकारात शुष्क प्रणाली वापरतात व तीत अचुंबकीय कण अडकण्याची समस्या कमी करण्यासाठी प्रत्यावर्ती (ठराविक कालावधीने पुन्हा पुन्हा दिशा बदलणाऱ्या) चुंबकीय प्रणालीचा उपयोग करून चूर्णरूप राशी वरखाली हलविण्यात येते.
चुंबकीय विलगीकरण मूलतः चुंबकीय धातुकांचे समृद्धीकरण करण्यासाठी विकसित केलेले होते पण आता उच्चतर तीव्रतेचे चुंबकीय विलगीकरण अचुंबकीय हेमॅटाइटाची प्रवणता व त्यापेक्षा कमी चुंबकीय प्रवणता असलेली द्रव्ये यांत भेद करू शकतात. [⟶ धातुकांचे शुद्धीकरण].
भाजणे : ही क्रिया सजल ऑक्साइड धातुके (लिमोनाइट) व कार्बोनेट धातुके (सिडेराइट) यांचे गुणधर्म बदलण्यासाठी वापरतात. भाजण्याच्या क्रियेचा उपयोग धातुकातील पाणी (यात काही सजल धातुकांतील रासायनिक रीत्या संयोगित झालेल्या पाण्याचाही अंतर्भाव होतो) काढून टाकण्यासाठी करतात. अगदी अल्प पातळीच्या वर धातुकातील गंधकाचे प्रमाण राहू देणे इष्ट नसते. हे गंधक प्रगलनाने काढून टाकता येत नाही पण भाजण्याने त्याचे क्षपण होते. सिडेराइट सामान्यतः त्यातील कार्बन डाय-ऑक्साइड काढून टाकण्याकरिता भाजतात. पट्टित धातुकांना चिकटून राहिलेली आणि त्यांत मिसळलेली वाळू व माती चुरडण्याच्या व चाळण्याच्या क्रियांत पुरेशी काढून टाकली जात नाही. अशी वाळू व माती काढून टाकण्यास भाजण्याच्या क्रियेची मदत होते. हेमॅटाइटे (विशेषतः टॅकोनाइटातील हेमॅटाइट अंश-अचुंबकीय, Fe2O3) चुंबकीय विलगीकरणाला प्रतिसाद देत नाहीत. भाजल्याने हेमॅटाइटात (Fe3 O4 ) क्षपण होते व ऑक्साइड अधिक चांगल्या प्रकारे मिळविणे शक्य होते.
संपिडीकरण : झोतभट्टीकरिता धातुक तयार करण्यातील ही अंतिम पायरी आहे. सूक्ष्मकणी द्रव्यापासून नियंत्रित राशी तयार करण्याच्या प्रक्रियांना मिळून ही सर्वसाधारण संज्ञा वापरतात. तापपिंडन, गुलिका वा गुठळ्या अथवा ठोकळे तयार करणे या प्रक्रिया विशिष्ट झोतभट्टीकरिता आवश्यक असलेल्या मालानुसार (भारानुसार) करण्यात येतात. संपिंडीकरणामुळे झोतभट्ट्यांची कार्यक्षमता वाढते व त्यांत भरावयाच्या मालातील कणांचे आकारमान एकविध (एकसारखे) असण्याची खात्री झाल्याने भट्ट्या चालविण्याचा खर्च कमी होतो. जेव्हा भट्टीत सरळ भरावयाची धातुके वापरण्यात येतात तेव्हा मालाची पार्यता व उष्ण वायूंना क्षपणासाठी उघडे राहणारे मालाचे क्षेत्रफळ यांत फार मोठा बदल होत राहतो. यामुळे बरेचसे सूक्ष्मकणी द्रव्य धूममार्गाने जाणाऱ्या धुळीच्या रूपात गमावले जाते. संपिंड वापरल्यास अशी परिस्थिती उद्भवण्याची शक्यता किमान ठेवता येते.
तापपिंडन : या क्रियेत बारीक दळलेले वा संहत (इष्ट घटकाचे प्रमाण वाढविलेले) धातुक इंधनाबरोबर मिसळतात व मुद्दाम निर्माण केलेल्या हवेच्या झोतात जाळतात. या क्रियेने मिळणाऱ्या पदार्थाला तापपिंड म्हणतात आणि तो कठीण, सच्छिद्र व कोशमय असून त्याच्या संरचनेत लक्षणीय बिघाड न होता हाताळणी व प्रगलन करता येईल इतका तो मजबूत असतो. तापपिंडनाच्या यंत्राची मूलभूत रचना सापेक्षतः साधी असते. बारीक दळलेले धातुक, चुनखडी व कोक किंवा अँथ्रॅसाइट ठेवलेली नरसाळी पात्रे प्रत्येक घटक योग्य प्रमाणात मिश्रकात भरतात. मग मिश्रण पूर्णतः होईल व त्याची सच्छिद्रता इष्टतम राहील इतके पुरेसे पाणी घालतात. मिश्रकातून तांदळाच्या दाण्यांच्या आकारमानाचे मिश्रणाचे गोलक सतत फिरणाऱ्या पट्ट्यावर सोडले जातात. वाहक पट्ट्याच्या गतीमुळे हे गोलक आडव्या दिशेने सरकून यंत्राच्या प्रज्वलन कक्षेत शिरतात व तेथे मिश्रणातील कोक जळू लागतो. चोषण पंख्यांनी पुरविलेल्या हवेच्या झोतामुळे तापपिंडाचे तापमान लवकरच १,३००° ते १,५००° से.पर्यंत वाढते व तापपिंड पट्ट्याच्या थंड टोकाकडे सरकविला जात असताना तो वरच्या टोकापासून खालपर्यंत जळत जातो. तापपिंडाची जाडी क्रिया करण्यात येत असलेल्या धातुकाच्या प्रकारानुसार १८ ते ४६ सेंमी. असते. ज्वलन अवस्थेतील तापपिंडनाचा काळ ४ ते १८ मिनिटे असतो. त्यानंतर तापपिंड हवेने थंड केला जातो. तापपिंडनाचे तापमान एकेका कणाची प्रारंभिक वितळणक्रिया होण्यास पुरेसे असते आणि शेवटी मिळणारा पदार्थ सच्छिद्र व गुठळ्यांसारख्या कणांचा घातलेला असतो व तो मग झोतभट्टीकडे पाठविला जातो. तापपिंडात घातलेल्या चुनखडीमुळे झोतभट्टीतील माल स्वयं-अभिवाही [⟶अभिवाह] बनतो व त्यामुळे भट्टीला लागणाऱ्या कोकचे प्रमाण पुष्कळ कमी होते.
गुलिका करणे : टॅकोनाइट व इतर कमी दर्जाची धातुके आर्थिक दृष्ट्या सुसाध्य झाल्यावर गुलिका करण्याच्या क्रियेला प्रथम महत्त्व आले. चुंबकीय विलगीकरणासाठी मॅग्नेटाइट त्याच्या आधारद्रव्यातून सोडविण्याकरिता विशेषतःटॅकोनाइट जवळजवळ चूर्णरूप करावे लागते. यापासून मिळणाऱ्या उपयुक्त धातुकाच्या कणांचे आकारमान तापपिंडन क्रिया परिणामकारकपणे वापरण्याच्या दृष्टीने फार बारीक समजण्यात येते. गुलिका करण्यासाठी बारीक दळलेले धातुक (सामान्यतः मॅग्नेटाइट) त्याच्या सच्छिद्रतेनुसार ८ ते १५% जलांश होईल इतके ओले करतात. पाण्याबरोबर बंधकद्रव्य म्हणून बेंटोनाइट मृत्तिका घालता येते. योग्य प्रकारे मिश्रण केल्यावर उंच बाजू असलेल्या चकतीच्या आकाराचे पात्र असलेल्या यंत्रात धातुकापासून गुलिका तयार करतात. चकती एका कोनात कलंडलेली व फिरती असल्याने धातुक मिश्रण घरंगळते आणि त्याचे ९.५ ते २५.५ मिमी. आकारमानांच्या गुलिकांमध्ये संपिंडीकरण होते.
अपक्व (न भाजलेल्या) स्थितीतील गुलिकांवर कोळशाच्या चूर्णाचा थर देतात. नंतर या गुलिका शुष्क आच्छादनातून नेतात व मग एक सारख्या जाळीवर नेऊन तेथे गुलिकांवरील कोळशाचा थर पेटविण्यात येतो. यात भाजण्याचे तापमान तापपिंडन क्रियेपेक्षा काहीसे कमी, पण प्रारंभिक वितळणक्रियेला चालना देणाऱ्या तापमानापेक्षा जरा कमी असते. ज्वलन क्रियेत कण-संरचनेत होणाऱ्या बदलामुळे बंधनबल मिळते. गुलिका भाजण्याच्या कूपक भट्टी पद्धतीत अपक्व गुलिकांवर कोळशाच्या चूर्णचा थर देण्याऐवजी ते गुलिकांत मिसळतात. कूपक भट्टीतून गुलिका खाली उतरत असताना जळणाऱ्या कोळशामुळे तापमान सु. १,३००° से.पर्यंत वाढून मॅग्नेटाइटाचे हेमॅटाइटात ऑक्सिडीभवन होते व त्यामुळे कणांमध्ये बंध निर्माण होतात. गुलिकांचे कठिनीकरण करण्याच्या तिसऱ्या पद्धतीत सरकत्या जाळीवर गुलिका कोरड्या केल्या जातात व मग बाह्य उष्णतेचा उपयोग करून तिरप्या परिभ्रमी भट्टीत भाजल्या जातात. वर वर्णन केलेल्या इतर पद्धतीतही कोळशापासून मिळणाऱ्या उष्णतेखेरीज बाह्य उष्णता द्यावी लागते. गुलिका करण्याच्या क्रिया तापपिंडनासारख्याच असल्या, तरी त्यांत धातुकाच्या कण आकारमानाखेरीज एक मुख्य फरक प्राप्त होणाऱ्या बंध प्रकारात आहे. तापपिंडनात धातुकातील खनिज अंश काही विशिष्ट प्रमाणात वितळतो आणि अतिशय अचूक नियंत्रण ठेवले नाही, तर तापपिंडाची क्षपणीयता कमी करणारे आयर्न सिलिकेट तयार होण्याची शक्यता असते. गुलिका करण्याच्या क्रियेत वितळबिंदूइतके तापमान पोहचत नसल्याने बंध विसरण (कण एकमेकांत मिसळणे), ऑक्सिडीभवन आणि काही प्रमाणात पुनर्स्फटिकीभवन यांनी तयार होतात.
ठोकळे बनविणे : धातुकाच्या सूक्ष्म कणांपासून ठोकळे बनविण्याकरिता निरनिराळ्या प्रकारची बंधकद्रव्ये व दाबयंत्रे अथवा लाटण यंत्रे शीत अवस्थेत वापरतात. धातुकाचे शीत अवस्थेत बनविलेले ठोकळे प्रारंभी झोतभट्टीत भरावयाचा माल म्हणून समाधानकारक आढळले पण त्यांची उपयुक्तता कधीच सिद्ध झाली नाही. अलीकडे विकसित झालेल्या ठोकळेनिर्मित क्रियेत बंधक द्रव्याशिवाय ठोकळे तयार करून ते ८००° ते १,०००° से.पर्यंत तापवितात. तापपिंडनाकरिता लागणाऱ्या इंधनाच्या निम्मे इंधन वापरून तयार केलेले ठोकळे झोतभट्टीत वापरण्यायोग्य असण्याची शक्यता दिसून आली आहे.
गुठळीकरण : या संपिंडीकरण क्रियेत सूक्ष्मकणी धातुक प्रारंभिक वितळण क्रिया होईल इतके परिभ्रमी भट्टीत तापविण्यात येते. भट्टीच्या फिरण्याच्या क्रियेने धातुकाच्या गुठळ्या बनतात. तयार होणाऱ्या गुठळ्यांचे आकार व आकारमान एकविध नसतात आणि त्या तयार होण्यासाठी उच्च तापमान लागत असल्याने त्यांची क्षपणशीलता कमी असते. गुठळीकरणाचे स्थान अधिक स्वस्त व खात्रीलायक तापपिंडनाने मोठ्या प्रमाणावर घेतलेले आहे.
प्रत्यक्ष वापरावयाची संपिंडीकरणाची पद्धती सामान्यतः तापपिंडन व गुलिकाकरण यांच्यात निवड करून ठरविली जाते. पद्धतीची अंतिम निवड धातुकाचा प्रकार, उपलब्ध इंधन, उत्पादित पदार्थ स्वयं-अभिवाही असलेला वा अभिवाही नसलेला, उत्पादित पदार्थाची क्षपणशीलता यांसारख्या अनेक बाबींवर तसेच संयंत्राचे स्थान, धातुकाची की संपिंडांची वाहतूक व सर्वांत महत्त्वाचे म्हणजे ग्राहकाच्या गरजा यांसारख्या स्थानिक गोष्टींवरही अवलंबून असते.
इंधन : लोखंडाप्रमाणे दगडी कोळसा विपुल आहे; पण त्याचे जगामध्ये एकविधतेने वितरण झालेले नाही. जगातील ज्ञात कोळशाच्या साठ्यांपैकी दक्षिण गोलार्धात फक्त सु. ३% साठे आहेत. सर्वांत मोठे साठे उत्तर अमेरिकेत व उत्तर आशियात आहेत. यांखेरीज सर्वच कोळसा लोहनिर्मितीसाठी योग्य आहे असे नाही. धातू उद्योगात वापरावयाचा कोक तयार करण्यासाठी लागणाऱ्या कोळशाचा जगातील अनेक भागांत तुटवडा आहे. कोक तयार करण्यासाठी सु. २०% बाष्पनशील (बाष्परूपाने उडून जाणारे) द्रव्य असणारा कोळसा (बिट्युमेनयुक्त कोळशात ४०% पर्यंत, तर अँथ्रॅसाइटात फक्त ५% बाष्पनशील द्रव्य असते) मर्यादित हवेच्या पुरवठ्यात सु. १,०००° से. तापमानाला तापवितात. बाष्पनशील घटक बाहेर काढून टाकतात व ते उत्पादित प्रदीपन वायूत मुख्य घटक म्हणून वापरतात. भट्टीत जवळजवळ शुद्ध कार्बनाच्या बनलेल्या, कठीण पण सच्छिद्र असलेल्या कोकचे गोळे उरतात. कोकच्या रासायनिक शुद्धतेइतकेच त्याचे बल महत्त्वाचे असते. झोतभट्टीत भरल्यावर कोकला त्याचा स्वतःचा चुराडा न होता त्याच्या वरील धातुकाच्या वजनाला आधार देता आला पाहिजे नाही तर भट्टीमधून हवेच्या प्रवाहाला अडथळा निर्माण होतो. आधुनिक झोतभट्टीची उंची मुख्यत्वे उपलब्ध कोकच्या बलावर अवलंबून असते. [⟶कोक; कोळसा, दगडी].
लोहनिर्मिती : लोखंडाचा अंतिम उपयोग शुद्ध वा पोलाद अथवा बीड यांपैकी कोणत्याही रूपात करावयाचा असला, तरी प्रथम लोखंड त्याच्या धातुकाचे क्षपण करून मिळवावे लागते. लोहनिर्मिती ही संज्ञा कच्च्या मालाचे लोखंडात रूपांतर करण्याच्या सर्व औद्योगिक प्रक्रियांना लावण्यात येते. लोखंडाच्या उत्पादनाची मुख्य प्रक्रिया झोतभट्टी प्रक्रिया हीच आहे. तथापि १९७० नंतर पर्यायी सरळ-क्षपण प्रक्रियांची झालेली वाढ महत्त्वाची आहे. झोतभट्टी प्रक्रिया व सरळ-क्षपण प्रक्रिया यांतील मुख्य घटक फरक त्यांच्या कार्य तापमानांत आहे. झोतभट्टीच्या उच्च कार्य तापमानाला वितळलेल्या लोखंडाचे घन वा स्पंजी लोखंड तयार होते. जगात उत्पादित होणाऱ्या बहुतांश लोखंडाचा उपयोग पोलादाच्या उत्पादनाकरिता करण्यात येतो. उरलेल्या लोखंडाचा उपयोग ओतिवांत, मिश्रधातूंत व लोह चूर्णरूपात करण्यात येतो.
झोतभट्टी : झोतभट्टीत पिग लोखंड तयार करणे हा लोखंड उद्योगाचा मूलभूत भाग आहे. झोतभट्टीचा उपयोग करण्यासाठी धातुक, इंधन, चुनखडी व शीतनासाठी पाणी यांचा विपुल पुरवठा आवश्यक असतो.
पुरेशा उच्च तापमानाला आयर्न ऑक्साइडाची कार्बन मोनॉक्साइड (CO) वायूबरोबर विक्रिया हाते आणि कार्बन डाय-ऑक्साइड (CO2) वायू व लोह धातू तयार होतात. ही विक्रिया सातत्याने चालू राहावी असा झोतभट्टीचा अभिकल्प केलेला असतो. हे साधण्यासाठी प्रतिप्रवाहाचा उपयोग केला जातो. कार्बन व आयर्न ऑक्साइड झोतभट्टीच्या कूपकातून स्थिर वेगाने खाली उतरतात, तर हवा खालून वर प्रवाहित होते. कोकच्या रूपातील कार्बन दोन प्रकारे कार्य करतो; तो भट्टी तापवितो व त्याचबरोबर त्यापासून तयार होणाऱ्या कार्बन मोनॉक्साइड वायूने आयर्न ऑक्साइडाचे क्षपण होऊन धातू मिळते. कार्बन डाय-ऑक्साइड वायू भट्टीच्या वरच्या भागातून बाहेर काढतात व द्रवरूप लोखंड तळाशी काढून घेतात. अंतर्गत विटकामाची दुरुस्ती करण्यासाठी बंद करावी लागेपर्यंत भट्टी सतत चालू ठेवता येते.
झोतभट्टीत घडून येणाऱ्या रासायनिक विक्रिया पुढीलप्रमाणे असतात. हवेचा झोत व कोक परस्परांच्या संपर्कात आल्यावर कोक जळू लागतो व कार्बन मोनॉक्साइड वायू तयार होतो.
C + ½ O2 ⟶ CO
हा वायू आयर्न ऑक्साइडाचे क्षपण करणारा प्रमुख कारक असतो. क्षपण खालील तीन पायऱ्यांत घडून येते.
3 Fe2O3 + CO ⟶ 2 Fe3O4 + CO2
2 Fe3 O4 + 2CO ⟶ 6FeO + 2CO2
FeO + CO ⟶ Fe + CO2
हे क्षपण खाली उतरणाऱ्या धातुक व कोक मिश्रणाचे तापमान ६००°—७००° से. पोहोचल्यावर घडून येते. यामुळे घन पण सच्छिद्र असलेले स्पंजी लोखंड तयार होते आणि ते झोतभट्टीच्या खालच्या अधिक उष्ण भागात वितळते.
झोतभट्टीत शुद्ध आयर्न ऑक्साइड, कार्बन व ऑक्सिजन वापरणे शक्य झाले असते, तर भट्टीचे रसायनशास्त्र वर वर्णन केल्याइतके सोपे झाले असते. प्रत्यक्षात हवेच्या झोतात ऑक्सिजनापेक्षा नायट्रोजन अधिक असतो व धातुकात ५०% वा त्यापेक्षाही जास्त मूलद्रव्ये (प्रामुख्याने सिलिकेटे) असतात. नायट्रोजन विक्रिया न होताच भट्टीतून निघून जातो; परंतु सिलिकेटांमुळे समस्या उद्भवतात. लोखंडापासून सिलिकेटे अलग करण्यासाठी व ती भट्टीतून काढून टाकण्याकरिता वितळविणे आवश्यक असते. लोखंडातील सिलिकेट खनिजे झोतभट्टीत वितळत नाही; पण चुनकळीबरोबर(CaO) विक्रिया करून वितळलेली मळी बनवितात. याकरिता धातुकाबरोबर योग्य प्रमाणावर चुनखडी (CaCO3) भट्टीत घालतात. चुनखडीचे (किंवा अभिवाहाचे) भट्टीच्या वरच्या भागात खालील विक्रियेनुसार अपघटन (घटक द्रव्यांत विलगीकरण) होते.
CaCO3⟶ CaO + CO2
तीत तयार झालेल्या चुनकळीची सिलिकेटांबरोबर विक्रिया होऊन द्रवरूप मळी तयार होते. झोतभट्टीत जवळजवळ लोखंडाइतकीच मळी तयार होते. तिचे घनीभवन झाल्यावर गर्द रंगाचे काचमय द्रव्य तयार होते.
वरील वर्णनावरून झोतभट्टीच्या अभिकल्पातील मुख्य बाबी लक्षात येतील. भट्टीत वरच्या भागात इंधन, धातुक व अभिवाह (चुनखडी) आणि तळाशी हवा सतत सोडण्याची सोय करणे आवश्यक असते. भट्टीची उंची आवश्यक रासायनिक विक्रिया घडून येण्याइतकी पुरेशी असली पाहिजे. भट्टीच्या वरच्या भागात घनरूप द्रव्ये भरण्याची व तळाशी द्रवरूप उत्पादने काढून घेण्याची सोय असली पाहिजे आणि त्याच वेळी वायूचा वरच्या दिशेनेसतत प्रवाह चालू ठेवला पाहिजे. भट्टीच्या तळाजवळ असलेल्या छिद्रयुक्त प्रोथांतून (निमुळत्या नळ्यांतून) हवा फुंकली जाते. क्षपणाने मिळणारे स्पंजी लोखंड व मळी भट्टीच्या खालील शंक्काकार भागात (‘बॉश’ मध्ये) वितळतात आणि प्रोथांच्या खालील तळ भागात द्रव साठतात. तळ भागाच्या भित्तीतील एका भोकातून ठराविक काळाने धातू व त्याच्या वरच्या खाचेसारख्या दुसऱ्या भोकातून मळी काढून घेतात. ही दोन्ही भोके धातू वा मळी काढून घ्यावयाची नसेल तेव्हा मृत्तिकेने बंद करतात.
भट्टीत भरलेली द्रव्ये हळूहळू खाली उतरत असताना आयर्न ऑक्साइडाचे स्पंजी लोखंडात होणारे क्षपण व चुनखडी अभिवाहाचे अपघटन भट्टीच्या मुख्य भागात (‘स्टॅक’ मध्ये) घडून येते. प्राथमिक तापन या भागाच्या वरच्या टोकापाशी असलेल्या गळ्यासारख्या भागात हाते. कार्बन डाय-ऑक्साइड व नायट्रोजन वरच्या टोकापाशी असलेल्या मोठ्या नळांतून सतत बाहेर काढले जातात. भट्टीच्या गळ्यातील वायुदाब वातावरणीय दाबापेक्षा जास्त असलेल्या स्थितीत भट्टी चालवावी लागते. त्यामुळे वायुदाबाची हानी न होता व भट्टीत अगोदरच असलेला सूक्ष्म कणरूपी घटक बाहेर उडवून घालविल्याशिवाय माल भरण्यासाठी भट्टीचा वरचा भाग उघडणे शक्य होत नाही. ही समस्या सोडविण्यासाठी दुहेरी घंटाकृती भरण प्रणाली वापरण्यात येते. भट्टीत मालाचा प्रवेश होण्यासाठी वरची घंटा खाली आणल्यावर खालची घंटा वर ओढून घेऊन वाताभेद्य झीरपपरोध (सील) तयार होतो. मग वरची घंटा बंद करून भट्टी बंदिस्त करतात व माल भट्टीच्या गळ्यातून जाण्यासाठी खालची घंटा उघडतात.
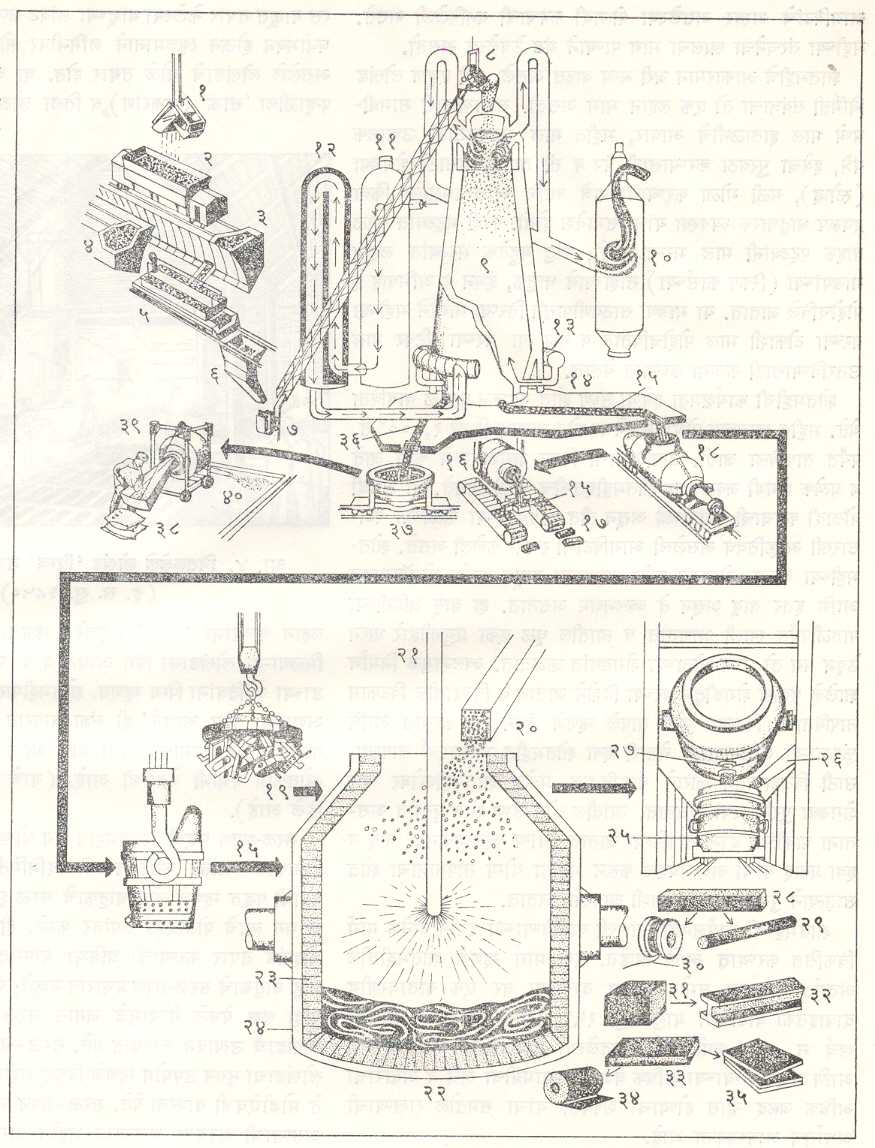
आधुनिक झोतभट्टीची संरचना खूप मोठ्या आकारमानाची असते. दर दिवशी १,००० टन लोखंड तयार करणारी भट्टी सु. ३० मी. उंच व बॉश या भागापाशी सु. ८ मी. व्यासाची असते. ही भट्टी आतून आगविटांचे अस्तर असलेल्या पोलादी कवचाची बनविलेली असते. भट्टीच्या संरचनेच्या खालचा भाग पाण्याने थंड ठेवलेला असतो.
झोतभट्टीचे आकारमान जरी भव्य वाटत असले, तरी एकूण लोखंड निर्मिती संयंत्राचा तो एक लहान भाग असतो. साहाय्यकारी सामग्रीमध्ये माल हाताळणीचे आवार, भट्टीत माल भरण्यासाठी उच्चालक यंत्रे, हवेचा पुरवठा करण्यासाठी पंप व ती तापविण्यासाठी शेगड्या (स्टोव्ह), मळी गोळा करण्याची पात्रे आणि ओतकामशाला किंवा द्रवरूप धातुधारक व्यवस्था यांचा समावेश होतो. काही भट्ट्यांत सरळ वाहक पट्ट्यांनी माल भरला जातो; परंतु बहुतेक भट्ट्यांत लहान गाड्यांच्या (स्किप कार्सच्या) साहाय्याने धातुक, इंधन व अभिवाह हे पोहोचविले जातात. या गाड्या साठवणीपासून तिरप्या मार्गाने भट्टीच्या वरच्या टोकाशी माल पोहोचवितात व तेथे त्या वरच्या घंटेवर माल उतरविण्यासाठी कलत्या करण्यात येतात.
झोतभट्टीची कार्यक्षमता हवेचा उष्ण झोत वापरून पुष्कळ वाढविता येते. भट्टीत खालच्या प्रोथांतून हवेचा झोत जाण्यापूर्वी तो १,०००° से.पर्यंत तापविला जातो. तापविण्याची क्रिया शेगड्यांमध्ये केली जाते व प्रत्येक शेगडी जवळजवळ झोतभट्टीइतकीच मोठी असते. ही शेगडी पोलादी कवचाची बनविलेली असून तीत बुद्धिबळाच्या खेळाच्या पटासारखी आकृतिबंध असलेली आगविटांची रचना केलेली असते. झोतभट्टीच्या वरच्या टोकातून बाहेर पडणाऱ्या वायूत कार्बन मोनॉक्साइड आणि इतर वायू असून ते ज्वलनक्षम असतात. हा वायू जमिनीच्या पातळीपर्यंत खाली आणतात व त्यातील धूळ एका प्रयुक्तीद्वारे धरून ठेवून मग तो उष्ण झोताच्या शेगड्यांत जाळतात. ज्वलनामुळे निर्माण झालेले पदार्थ शेगडीतून वरच्या दिशेने जातात व तिच्यातील विटकाम तापवितात. विटकाम पुरेसे तापले म्हणजे इंधन बंद करतात आणि फुंकणाऱ्या एंजिनापासून येणारी हवा झोतभट्टीत जाण्यापूर्वी तापण्यासाठी विटकामातून जोराने घालवितात. प्रत्येक झोतभट्टीबरोबर चार शेगड्या पुरविलेल्या असतात. त्यांतील दोन उष्ण झोत पुरवीत असताना बाकीच्या दोन तापविल्या जातात. योग्य कालावधीनंतर वायू व हवा प्रवाह यांची अदलाबदल करून भट्टीला योग्य तापमानाचा झोत सातत्याने पुरविला जाईल अशी व्यवस्था करतात.
झोतभट्टीची कार्यक्षमता आणखी वाढविण्याच्या दृष्टीने अनेक मार्ग विकसित करण्यात आले आहेत. एक मार्ग म्हणजे झोतभट्टीतील अंतर्गत वायुदाब सभोवतालच्या दाबाच्या वर एक वातावरणीय दाबाइतका वाढविणे. यामुळे सु.१५% उत्पादन वाढते व कोकचा खर्च सु. १०% कमी होतो. वाढलेल्या उत्पादनाचा आर्थिक लाभ आणि वायू फुंकण्याच्या अधिक वजनदार सामग्रीचा खर्च व अस्तराचा अधिक जलद ऱ्हास होण्याची शक्यता यांचा समतोल राखण्याची अर्थातच आवश्यकता आहे.
झोतभट्टीतील एका भोकावाटे द्रव मळी वाहते व द्रव धातू दुसऱ्या भोकावाटे बाहेर पडते. पूर्वी रेल्वेच्या डब्यांवर बसविलेल्या मोठ्या पात्रांत भट्टीतून मळी सरळ वाहू देत व मग ती द्रवरूप असेपर्यंत फेकून देत असत. यामुळे पोलादनर्मिती कारखान्यांनजीक मळीचे मोठे ढीग साचत. आत ही मळी भट्टीजवळच्या प्रक्रिया संयंत्रात नेतात व तेथे ती पाण्याने थंड करून दाणेदार रूपात मिळवितात. ही दाणेदार मळी काँक्रीट तयार करताना मिसळण्यासाठी, रेल्वेत पूरक भार म्हणून, खनिज लोकरीत व महामार्गाच्या पृष्ठभागावर लावण्यात येणाऱ्या घसरणरोधक द्रव्यात वापरण्याकरिता विकण्यात येते.
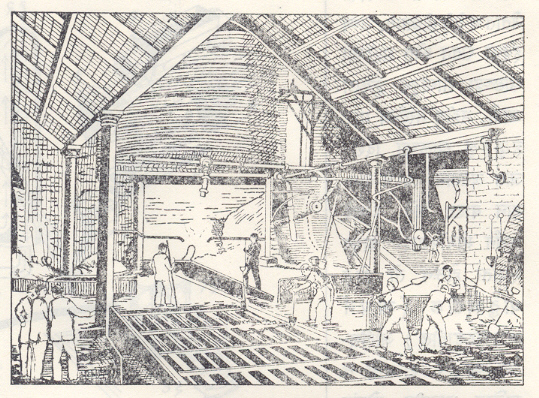
पूर्वीच्या काळात झोतभट्टीत तयार केलेल्या द्रवरूप लोखंडापासून साठविण्याकरिता, वाहतुकीकरिता वा पुन्हा वितळविण्यासाठी ओतिवे तयार करीत. भट्टीच्या भोकातून बाहेर पडणारे द्रवरूप लोखंड भट्टीच्या समोरील वाळूच्या थरातील पन्हाळीत सोडत. पन्हाळीत लोखंडाचा रस वाळूत तयार केलेल्या बाजूच्या लांबट कप्प्यांत शिरे व त्यात त्याचे घनीभवन होऊन स्थूलमानाने जमिनीवर झोपलेल्या डुकराशी साम्य असलेले लोखंडाचे गोळे तयार होत. या वाळूच्या थरातील मुख्य पन्हाळीला ‘साऊ’ (डुकरीण) व तिला छोट्या पन्हाळींनी जोडलेल्या लहान कप्प्यांना ‘पिग्ज’ (डुकरे) म्हणत. म्हणून झोतभट्टीपासून मिळणाऱ्या लोखंडाला पिग आयर्न व या पद्धतीने मिळणाऱ्या लोखंडाच्या ओतिवांना पिग्ज म्हणत. झोतभट्टीपासून मिळणाऱ्या लोखंडाला अद्यापही ‘पिग आयर्न‘ ही संज्ञा वापरात आहे. पिग लोखंडाच्या वाळूतील ओतकामाची जागा मात्र आता मोठ्या प्रमाणावर पिगओतकाम यंत्रांनी घेतलेली आहे. (याचे थोडे अधिक वर्णन पुढे दिले आहे).
सरळ-क्षपण पद्धती : झोतभट्टीत पिग लोखंड तयार करून मग त्याचे पोलादात रूपांतर करणे या पोलादनिर्मितीच्या अप्रत्यक्ष पद्धतीची पर्यायी पद्धत म्हणजे लोह धातुकाचे सरळ शुद्ध लोखंडात क्षपण करणे व मग त्याचे पोलादात रूपांतर करणे. ही सरळ-क्षपण पद्धत होय. लोहखंड तयार करण्याची प्रक्रिया वापरातून गेल्यावर कित्येक वर्षे लोह धातुकाचे सरळ-क्षपण प्रचारात नव्हते परंतु या पद्धतीकडे आता पुन्हा लक्ष वेधले गेल्यामुळे जगात सरळ-क्षपण पद्धतीने सु.४% लोखंडाचे उत्पादन करण्यात येते. सरळ-क्षपण पद्धतीने मिळविलेल्या लोखंडाचा मुख्य उपयोग म्हणजे विद्युत् भट्टीत पोलादनिर्मिती करताना ते मोडीऐवजी वापरता येते. सरळ-क्षपण केलेले लोखंड अतिशय शुद्ध असण्याची शक्यता असल्याने भट्टीत भरावयाच्या मालात त्याचा समावेश केल्यामुळे कमी दर्जाच्या मोडीतील शुष्क द्रव्यांचे विरलीकरण होते. सरळ-क्षपण प्रक्रियांचाउपयोग⇨चूर्ण धतुविज्ञानात वापरण्यात येणाऱ्या दाणेदार लोखंडाच्या निर्मितीसाठीही करण्यात येतो. स्पर्धेत टिकण्यासाठी झोतभट्टी संयंत्र खूप मोठे असावे लागते. सरळ-क्षपण संयंत्राच्या उभारणीसाठी सापेक्षतः कमी भांडवली गुंतवणूक करावी लागते व झोतभट्टीत गुंतवणूक करण्याची खात्री नसेल तेथे या संयंत्राचा पर्याय असतो. या संयंत्रात द्रवरूप लोखंड हाताळण्याची सामग्री उभारावी लागत नाही. सरळ-क्षपण संयंत्राच्या अनेक निरनिराळ्या अभिकल्पांच्या चाचण्या घेण्यात आलेल्या आहेत पण कोणताच अभिक्लप सर्वसाधारण उपयोगात येऊ शकेल इतका सरस आढळलेला नाही.
सरळ-क्षपणासाठी क्षपणकारक म्हणून कार्बन मोनॉक्साइड व हायड्रोजन हे वायू किंवा त्यांचे मिश्रण वापरण्यात येते. क्षपणकारक वायूच्या उपस्थितीत धातुक ८००° ते १२००° से.च्या दरम्यानच्या तापमानापर्यंत तापविण्यात येते. हा वायू लोखंडनिर्मितीच्या भट्टीतच वा बाहेर तयार करता येतो. धातुकाचे खालील विक्रियांनुसार क्षपण होते.
Fe2O3 + 3CO ⟶ 2 Fe + 3CO2
Fe2O3 + 3H2⟶2 Fe + 3H2O
क्षपण ९००° ते १,०००°से. यांच्या दरम्यानच्या तापमानाला केले, तर १ ते २.५% कार्बनाचे प्रमाण असलेले स्पंजी लोखंड मिळते आणि जर क्षपण १,०००° ते १,२००° से.यांच्या दरम्यानच्या तापमानाला केले, तर कार्बनाची प्रमाण कमी असते. तापमान १,२००° से.च्या वर असते तेव्हा लोखंड कार्बनाचे शोषण करते, त्याचा वितळबिंदू कमी होतो व अंशतः वितळलेले लोखंड मिळते.
जर्मनीमध्ये अभिकल्पित केलेल्या क्रप-रेन प्रक्रियेत बारीक दळलेले धातुक कोक किंवा कोळशाच्या चूर्णाबरोबर मिसळतात. हे मिश्रण परिभ्रमी भट्टीत तापवितात व कार्बन, मोनॉक्साइडाने त्याचे क्षपण करतात. चूर्णरूप कोळाशाने पुरविलेली उष्णता लोखंड वितळणार नाही, पण द्रव मळी तयार होईल अशा प्रकारे नियंत्रित करतात. या प्रक्रियेत मिळणारा पदार्थ थंड करतात, त्याचा चुरा करतात व चुंबकीय रीतीने त्याचे विलगीकरण करतात. क्रप-रेन व त्यासारख्या प्रक्रियांनी स्पंजी लोखंड मिळते.
लोखंडाचे धातुवैज्ञानिक प्रकार : पिग लोखंड : झोतभट्टीपासून मिळणारा हा लोखंडाचा अशुद्ध प्रकार असून त्यात लोखंडाखेरीज ३ ते ४% कार्बन, २ ते ३ % सिलिकॉन, ०.५ ते २% मँगॅनीज व सु. ० .० ४% गंधक व फॉस्फरस असतात. प्रारंभीच्या काळात या लोखंडाचे वाळूच्या थरातील कप्प्यांत ओतकाम करून पिग्ज या नावाने ओळखण्यात येणारी ओतिवे तयार करीत असत (याचे वर्णन वर दिलेले आहे). आता बहुतेक लोखंड झोतभट्टीपासून मिळते व ते रेल्वेच्या उष्णता-विरोधित टाकीसारख्या डब्यांतून सरळ पोलाद परिष्करण भट्टीत (खुल्या चुल्याच्या भट्टीत व आता उतरत्या प्रमाणात बेसेमर परिवर्तकात) पाठविले जाते. पिग लोखंडाच्या वाळूतील ओतकामाची जागा आत मोठ्या प्रमाणात पिग-ओतकाम यंत्रांनी घेतलेली आहे. या यंत्रात ओतिवे तयार करण्यासाठी द्रवरूप लोखंड भट्टी शेजारून सतत जाणाऱ्या वाहक पट्ट्यावरील पोलादी साच्यांत ओततात. लोखंडाचे घनीभवन झाल्यावर साचा उलटा होऊन ओतीव बाहेर पडते व साचा नवीन ओतीव बनविण्यासाठी स्वयंचलित रीत्या परत जातो. ओतीव साच्याला चिकटू नये म्हणून साच्याला आतून चुनकळीचा वा डांबराचा थर लावतात. वाळूत तयार केलेल्या पिग्जपेक्षा यंत्राने केलेले पिग्ज अधिक स्वच्छ असतात व त्यांना वाळू चिकटलेली नसल्याने नंतरच्या पुन्हा वितळविण्याच्या प्रक्रिया दूषित होत नाहीत. बीड उद्योगातील ओतशालेच्या उपयोगाकरिता ओतलेले पिग साधारण ५०.८ x २२.८ x १०.१ सेंमी. या आकारमानाचे असतात.
रासायनिक संघटनानुसार पिग लोखंडाचे तीन प्रतींत वर्गीकरण करतात. क्षारकीय (अम्लाशी विक्रिया झाल्यास लवण देण्याचा गुणधर्म असलेले) पिग लोखंड पोलादनिर्मितीसाठी वापरण्यात येते. यात सिलिकॉनाचे प्रमाण कमी (जास्तीत जास्त १.५%) असल्याने परिष्करण भट्ट्यांच्या उच्चतापसह अस्तरावरील आक्रमणाला प्रतिबंध होतो. क्षारकीय पिग लोखंडातील गंधकाचे प्रमाण अगदी कमी (०.०४%) असणे आवश्यक आहे. कारण गंधक ही पोलादातील क्रियाशील अशुद्धी असून परिष्करण भट्टीत ते काढून टाकले जात नाही. फॉस्फरसाचे प्रमाण सामान्यतः १ टक्क्यापेक्षा कमी व मँगॅनीज १ ते २% या मर्यादेत राखण्यात येते. कार्बनाचे प्रमाण ३.५ ते ४.४ टक्क्यांपर्यंत बदलते.
ओतशाला पिग लोखंडात लोखंडी ओतिवे तयार करण्यासाठी वापरण्यात येणाऱ्या सर्व प्रकारांचा समावेश होतो.यात सिलिकॉन ०.५ ते ३.५%, गंधक ०.०५ टक्क्यापर्यंत, फॉस्फरस ०.०३५ ते ०.९%, मँगॅनीज ०.४ ते १.२५% आणि कार्बन ३.० ते ४.५% अशी घटकांची प्रमाणे असतात.
लोहमिश्रके या पिग लोखंडाचा मिश्रधातू असून यांपैकी प्रत्येक मिश्रधातूत एखाद्या विशिष्ट मूलद्रव्याचे प्रमाण जास्त असते. उदा., फेरोमँगॅनीज हे ७४ ते ८२% मँगॅनीज धातुक असलेले पिग लोखंड असते. फेरोसिलिकॉनात ५ ते १७% सिलिकॉन तर फेरोफॉस्फरसात १५ ते २४% फॉस्फरस असतो. लोहमिश्रकांचा उपयोग लोखंड व पोलाद यांतील गुणधर्म नियंत्रित करण्यासाठी व बदलण्यासाठी त्यांत समाविष्ट करावयाची द्रव्ये म्हणून करतात. [⟶ लोहमिश्रके].
स्पंजी लोखंड : याचा उपयोग मुख्यत्वे उच्च शुद्धतेच्या व विद्युत् भट्टीत तयार करण्यात येणाऱ्या मिश्र पोलादांत वितळण्याकरिता आधार, विशिष्ट रासायनिक प्रक्रियांत शोषक व इलेक्ट्रॉनीय उद्योगात उच्च शुद्धतेच्या लोखंडाचा उद्गम यांकरिता करण्यात येतो. याच्या उत्पादनासाठी क्रप-रेन प्रक्रिया वापरतात. तीत घन धातुकाचे घन लोखंडात क्षपण होते. स्पंजी लोखंड सापेक्षतः अशुद्ध असते परंतु त्याच्या उत्पादनासाठी वापरण्यात येणाऱ्या पद्धतीमुळे गंधकाखेरीज इतर मलद्रव्यांचे क्षपण होत नाही आणि ती लोखंडाऐवजी मळीबरोबर संयोग पावतात. झोतभट्टीच्या बाबतीत ही द्रव्ये लोखंडाशी संयोग पावतात. स्पंजी लोखंड वितळविल्यास बहुतांश मलद्रव्ये मळीच्या रूपात मुक्त होतात व सापेक्षतः शुद्ध स्वरूपाचे (९९.९% इतक्या उच्च शुद्धतेचे) लोखंड प्राप्त होते.
हायड्रोजन-क्षपित लोखंड : आयर्न ऑक्साइडाचे हायड्राजनाद्वारे क्षपण करण्याची प्रक्रिया अतिशय जटिल असून तीत प्रत्यक्ष क्षपण, निर्वातातील वितळणक्रिया व पुढे आणखी शुद्धीकरण यांचा अंतर्भाव होतो. या प्रक्रियेने स्पंजी लोखंडासारखे पण धातवीय अशुद्धी ०.००१% इतकी अल्प असलेले लोखंड मिळते. हायड्रोजन-क्षपित लोखंडाचे उत्पादन मूल्य उच्च व उत्पादित राशी कमी असल्याने ते केवळ संशोधन कार्यातच वापरले जाते.
कार्बोनिल लोखंड किंवा लोह कार्बोनिल : याचा उपयोग चुंबकीय द्रव तयार करण्यासाठी इलेक्ट्रॉनीय उद्योगात उच्च कंप्रता (दर सेकंदाला होणारी कंपन संख्या) अंतरकाच्या (गाभ्याच्या) उत्पादनासाठी व संशोधन द्रव्य म्हणून करण्यात येतो. लोह कार्बोनिल सामान्यतः आयर्न पेंटा कार्बोनिल [Fe(CO)5] या स्वरूपात असून त्याचे उष्णतेचे अपघटन केल्यावर असाधारण शुद्ध लोखंड व कार्बन मोनॉक्साइड मिळतात. बारीक चूर्णरूप हायड्रोजन-क्षपित लोखंडाची कार्बन मोनॉक्साइडाशी दाबाखाली अमोनियासारख्या उत्प्रेकरकाच्या (विक्रियेचा वेग बदलणाऱ्या पण तीत प्रत्यक्ष भाग न घेणाऱ्या पदार्थाच्या) उपस्थितीत तापवून विक्रिया घडवून आणून लोह कार्बोनिल मिळविले जाते. यात मिळणारे द्रव्य बाष्पनशील असते व २००° से. तापमानाला त्याचे अपघटन होते.
विद्युत् विच्छेदित लोखंड : हे सुद्धा उच्च शुद्धतेचे लोखंडाचे रूप असून फेरिक क्लोराइडासारख्या संयुगाच्या विद्युत् विच्छेदनाने (विद्युत् प्रवाहाच्या साहाय्याने संयुगातील घटक अलग करण्याच्या क्रियेने) मिळविले जाते. उपयोगात आणलेली विद्युत् अग्रे, विद्युत् प्रवाह घनता व विद्युत् विच्छेद्य पदार्थ यांच्यावर त्याची शुद्धता अवलंबून असते. ही शुद्धता ९९.९% पेक्षा अधिक असते.
पिंडरूप लोखंड : या प्रकारचे लोखंड १९०५ च्या सुमारास विकसित करण्यात आले व ते टनांत मोजण्याइतक्या मोठ्या प्रमाणावर तयार करण्यात येणारे सर्वांत शुद्ध रूप आहे. हे लोखंड मुख्यत्वे पत्र्याच्या रूपात वापरतात व सामान्यतः हे पत्रे⇨गॅल्व्हानीकरण केलेले (जस्त विलेपित) अथवा एनॅमल लावलेले असतात. मोठ्या प्रमाणावर तन्यता (तार काढता येण्याची क्षमता) व गंजराधकता आवश्यक असेल तेथेही या लोखंडाचा उपयोग करतात. छोट्या पुलांखालील जलवाहक नळ, गटारे, प्रशीतक (रेफ्रिजरेटर) व इतर साधनांची बाह्य कवचे यांकरिता पिंडरूप लोखंडाच्या उत्पादनाचा बराच मोठा भाग वापरला जातो.
प्रत्यक्षात पिंडरूप लोखंड तांत्रिक दृष्ट्या लोखंड नसून ते कार्बनाचे अतिशय कमी (सु. ०.०१२%) प्रमाण असलेले व खुल्या चुल्याच्या प्रक्रियेने तयार केलेले पोलाद असते. खुल्या चुल्याने तयार केलेले तितकेच कार्बन प्रमाण असलेले पोलाद व पिंडरूप लोखंड यांतील फरक म्हणजे लोखंडाच्या बाबतीत प्रक्रिया काटेकोरपणे नियंत्रित केली जाते व पोलादापेक्षा शुद्धीकरण (काळ व घटक विक्रिया या दोन्ही बाबतींत) खूप विस्तारपूर्वक केले जाते. अशा प्रकारे मिळालेल्या लोखंडात नेहमीची मलद्रव्ये (कार्बन, मँगॅनीज, सिलिकॉन, गंधक व फॉस्फरस) ०.०६% पेक्षाही कमी असतात.
घडीव लोखंड : लोखंडाचे हे सर्वांत जुने ज्ञात रूप आहे. त्याचा बायबलमध्ये उल्लेख आहे व ईजिप्तमधील एका पिरॅमिडामध्ये ५,००० वर्षांपूर्वीची घडीव लोखंडाची अवजारे सापडली आहेत. या लोखंडाचा मुख्यत्वे नळनिर्मितीत, रेल्वे व जहाजबांधणी यांसारख्या अवजड उद्योगांत आणि मोटारगाडी व कृषी अवजारांच्या उद्योगांत वापर होतो.
घडीव लोखंड हे आयर्न सिलिकेट मळीच्या बारीक व विखुरलेल्या तंतूंचे अतिशुद्ध लोखंडाबरोबरील भौतिक मिश्रणाच्या रूपात असते. ते वेगवेगळ्या विविध प्रक्रियांनी तयार करतात. सर्वांत प्रारंभीचे घडीव लोखंड लोह धातुक, चुनखडी व लोणारी कोळसा यांचे मिश्रण धातुकाचे क्षपण होईपर्यंत तापवून तयार करण्यात आले आणि या प्रक्रियेत मिळणाऱ्या चिक्कीसारख्या गोळ्याला मळी हा संरचनेचा भाग असलेल्या इष्ट आकारात घडविता येत असे. लोह धातुकापासून घडीव लोखंड तयार करण्याच्या सरळ प्रक्रियांची विविध सुधारित रूपे झोतभट्टीचा विकास होईपर्यंत उपयोगात होती. प्रांरभिक भट्ट्यांच्या वरच्या टोकाला माल भरण्यासाठी शंक्काकार भाग जोडून लोखंड प्रत्यक्ष वितळविण्याच्या सुरुवातीच्या प्रयत्नांमधून झोतभट्टीचा विकास झाला.
पुन्हा वितळविलेल्या पिग लोखंडापासून घडीव लोखंड तयार करण्याच्या अप्रत्यक्ष पद्धतीतून ढवळणी प्रक्रिया प्रचारात आली. या प्रक्रियेत दगडी कोळसा इंधन म्हणून वापरून चुल्याच्या प्रकारच्या भट्टीत पिग लोखंड वितळविण्यात येई. पिग लोखंड वितळत असताना जळणाऱ्या इंधनापासून निर्माण होणाऱ्या उष्ण वायूंमुळे लोखंडातील कार्बनाचे ऑक्सिडीभवन होते. या कार्बनाचे मूळ प्रमाण ३.५ ते ४.०% असे. पिग लोखंडातील सिलिकॉनाचेही ऑक्सिडीभवन होऊन तयार होणारी मळी वितळणाऱ्या पिग्जवर तरंगे. पिग्ज वितळण्याची क्रिया पूर्ण होईपर्यंत चालू असताना त्यात चुंबकीय आयर्न ऑक्साइड घालीत. त्यामुळे द्रव लोखंडातील बहुतांश कार्बन, सिलिकॉन, गंधक, फॉस्फरस व मँगॅनीज यांचे ऑक्सिडीभवन होऊन तयार होणारी ऑक्साइडे मळीत अंतर्भूत होत. मलद्रव्यांचे ऑक्सिडीभवन होत असताना वितळलेले लोखंड एक कर्मचारी लांब दांड्याच्या पोलादी पळीने ढवळीत असे. शुद्धीकरणाची ही क्रिया पुढे चालू ठेवल्यावर कर्मचाऱ्याला मधूनमधून द्रव मळीचा अंतर्भाव असलेले चिक्कीसारखे लोखंड ढवळणे अशक्य होईपर्यंत वितळबिंदू वाढत जाई. त्या वेळी लोखंड-मळी मिश्रणाचा गोळा भट्टीतून काढून घेऊन त्यातील जादा मळी दाबून काढून टाकीत व गोळा लाटून त्याच्या लाद्या तयार करीत. एकसारखेपणा राखण्याच्या दृष्टीने लाद्या कापून लहान तुकडे करीत आणि हे तुकडे एकावर एक रचून वितळजोडाच्या तापमानापर्यंत पुन्हा तापवीत व मग त्यांचे इष्ट आकारात पुन्हा लाटण करीत.
घडीव लोखंडनिर्मितीसाठी मानवी बळावर चालणाऱ्या व यांत्रिक अशा विविध रूपांतील ढवळणी प्रक्रिया सु. १९३० पर्यंत वापरात होत्या. त्या वेळी ॲस्टन-बायर्स प्रक्रिया विकसित झाली. ही प्रक्रिया अद्यापही वापरात असून तीत हस्त वा यांत्रिक ढवळणी प्रक्रियेत वापरण्यात येणाऱ्या पायऱ्या अलग करून काहीसा निराळा मार्ग अवलंबिला जातो. पिग लोखंडाचे वितळवून, गंधकरहित करून व मग बेसेमर परिवर्तकात परिष्करण करून जवळजवळ शुद्ध लोखंडात रूपांतर करतात. सु. १,५१०° से.तापमानाला असलेले वितळलेले लोखंड मग द्रवरूप आयर्न सिलिकेट मळी असलेल्या दोलक ओतपात्रात नियंत्रित वेगाने सोडतात. मळीचे तापमान सु. १,३२०°से. इतके राखलेले असते. अधिक तापमानाच्या धातूचा मळीबरोबर संपर्क होतो तेव्हा तिच्यातून काही विरघळलेले वायू बाहेर पडतात. अचानक झालेल्या घनीभवनामुळे तिचा भंग होऊन तुकडे तुकडे होतात आणि ते ओतपात्राच्या तळाशी बसतात व तेथे अद्यापही द्रवरूप असलेली व विखुरलेली मळी अंतर्भूत झालेला स्पंजासारखा लोखंडी गोळा बनतो. हे गोळे ३ते १० टनांपर्यंत वजनाचे असतात. ते दाबून त्यांतील अतिरिक्त मळी काढून टाकतात व त्याच्यावर पूर्वीच्या प्रक्रियांप्रमाणेच लाटणक्रिया करतात.
नमुनेदार घडीव लोखंडाच्या संघटनात ०.०८% कार्बन, ०.०३ % मँगॅनीज, ०.१८% सिलिकॉन, ०.११% फॉस्फरस, ०.०१५% गंधक व वजनाने सु. २.८५% मळी यांचा समावेश असतो. घडीव लोखंडाच्या चांगल्या नमुन्यात दर चौ. सेंमी. मध्ये किमान सु. ३ ९,००० मळीचे तंतू असावयास पाहिजेत. घडीव लोखंडाच्या संरचनेत रासायनिक दृष्ट्या अक्रिय व विखुरलेल्या स्वरूपातील मळीचा अंतर्भाव असल्याने त्याचे शिणवटा रोध [⟶धातूंचा शिणवटा] व गंजरोध चांगले असतात.
बीड : बीड ही एक सर्वसाधारण संज्ञा असून तीत लोह कार्बन-सिलिकॉन मिश्रधातूंची एक मालिकाच अंतर्भूत आहे. वितळलेली मिश्रधातू साच्यात ओतून बीड तयार करतात. पोलादात कार्बनाचा लोखंडाशी रासायनिक रीत्या संयोग झालेला असतो, तर याउलट बिडामध्ये विद्रावात धारण करणे शक्य असलेल्यापेक्षा अधिक कार्बन आढळतो. मिश्रधातूतील कार्बन व सिलिकॉन यांच्या प्रमाणात बदल करून बिडाचे निरनिराळे प्रकार तयार करता येतात. या प्रत्येक प्रकाराचे विभिन्न गुणधर्म व उपयोग आहेत.
बिडाच्या वस्तूंच्या निर्मितीत अनेक पायऱ्या असतात. ओतावयाच्या वस्तूची लाकडी वा धातूची प्रतिकृती किंवा फर्मा तयार करतात. बिडाचे घनीभवन होताना त्याचे होणारे आकुंचन विचारात घेऊन फर्म्याचे आकारमान ठरवितात. साचा तयार करण्यासाठी योग्य धारकपात्रात फर्म्याभोवती ओल्या वाळूमातीचे मिश्रण घट्ट भरतात. फर्मा साच्यापासून काळजीपूर्वक काढून घेतात आणि फर्म्याने निर्माण केलेल्या पोकळीत बीड ओततात. कच्च्या ओतिवाचे गुणधर्म बदलण्यासाठी त्यावर उष्णता संस्करण करावे लागण्याची शक्यता असते पण ह वस्तूच्या पाहिजे असलेल्या संरचनेच्या प्रकारावर अवलंबून असते. [⟶ओतकाम].
ओतकाम उद्योग हा प्रारंभिक मूलभूत उद्योगांपैकी एक आहे. या उद्योगाला मिळालेले यश व दीर्घायुष्य अनेक बाबींमुळे मिळालेले आहे. ओतावयाच्या वस्तूंच्या क्लिष्टतेवर जवळजवळ कोणतीही मर्यादा नाही. ओतकामाची प्रक्रिया कोणत्याही निर्मिती वेगाला (पुन्हा मागणी नसलेल्या एकाच वस्तूपासून ते पूर्णपणे स्वयंचलित व संगणक नियंत्रित प्रमाणापर्यंत) जुळवून घेता येते. हा उद्योग अत्यंत अष्टपैलू स्वरूपाचा असून त्यात काही ग्रॅमपासून ते कित्येक शेकडो टनांपर्यंत वजन असलेली ओतिवे तयार होतात. मिश्रधातूच्या रसायनशास्त्राचे समायोजन करून ओतिवे काचेसारखी कठीण व ठिसूळ ते मृदू व तन्य अशा विविध भौतिक गुणधर्माची तयार करता येतात. धातुरूपणाच्या घडाई व यंत्रण यांसारख्या इतर पद्धतींशी तुलना करता ओतकाम उद्योगाचे स्थान सामान्यतः अनुकूल असल्याचे दिसून येते. कारण त्याला लागणाऱ्या कच्च्या मालाचा खर्च कमी असतो व भांडवली गुंतवणूकही कमी लागते. बिडामधील कार्बन व सिलिकॉन यांच्या समावेशामुळे बीड १,१३०°से.ला वितळावयास लागते व त्याचे बहुतेक प्रकार सु. १,३००°से.ला पूर्णपणे वितळतात. याच कारणामुळे ओतकामासाठी वापरण्यात येणाऱ्या भट्ट्यांचे उच्चतापसह अस्तर दीर्घायुषी असते. वितळलेल्या शुद्ध लोखंडापेक्षा बिडाचा प्रवाहीपणा पुष्कळच जास्त असतो व त्यामुळे गुंतागुंतीच्या आकाराच्या वस्तूंचेही ओतकाम अधिक सुलभतेने करता येते.
बिडाचे विविध प्रकार सामान्यतः उभ्या भट्टीत पिग लोखंड व लोखंडाची निवडक मोड वितळवून तयार करतात. या भट्टीत चुनखडी व इतर अभिवाहांसह कोक इंधन म्हणून वापरतात. उभ्या भट्टीचा अभिकल्प मूलतः झोतभट्टीसारखाच असतो परंतु ती सु. १/४इतकी मोठी असते. वितळलेल्या लोखंडाचे रसायनशास्त्र (मुख्यत्वे त्यातील सिलिकॉन व कार्बन यांचे प्रमाण) नियंत्रित करून बिडाचे विविध प्रकार तयार करता येतात.
करडे बीड : हे बीड म्हणजे एकच मिश्रधातू नसून ज्यांचे संघटन स्पष्टपणे विशिष्ट स्थूल मर्यादांत आहे अशा मिश्रधातूंची एक मालिकाच असते. या मालिकेतील सर्व मिश्रधातूंचे यांत्रिक गुणधर्म सारखे असतात. नमुनेदार करड्या बिडात ३.२% कार्बन, २.२% सिलिकॉन, ०.६५% मँगॅनिज, ०.१५% फॉस्फरस व ०.१०% गंधक असू शकतात. वितळलेली मिश्रधातू सु. १,२५०°सें.पर्यंत थंड झाल्यावर द्रवामध्ये कण तयार होऊ लागतात. हे कण म्हणजे लोखंड व कार्बन यांचा ⇨घन विद्राव असतो आणि त्याला ऑस्टेनाइट म्हणतात. जसजसे तापमान उतरते तसतसे अधिक ऑस्टेनाइट तयार होते. त्याचवेळी द्रव मिश्रधातूतून ग्रॅफाइटाच्या पत्र्यांच्या रूपात कार्बन अवक्षेपित होतो (न विरघळणाऱ्या साक्याच्या रूपात तयार होतो). मिश्रधातू सु. १,१३०°से. तापमानाला पूर्णपणे घनरूप होईपर्यंत शीतलनक्रिया चालू राहते. या तापमानाला घनक्रांतिक समतापमान म्हणतात कारण द्रवाच्या अंतिम भागाचे घनीभवन तापमान विशेष न उतरता होते. १,१,३०°से.च्या खाली शीतलनाचा वेग फार मंद असेल, तर मिश्रधातूत ग्रॅफाइट पत्र्या व ऑस्टेनाइट कण परस्परांत मिसळतात. मंद शीतलन चालू राहिल्यास ग्रॅफाइट रूपातील कार्बन ऑस्टेनाइटातून बाहेर टाकला जातो. ७२३°से.ला ऑस्टेनाइट अस्थिर असते आणि मिश्रधातूचे अतिशय सावकाश शीतलन केले, तर ऑस्टेनाइटाचे फेराइट व ग्रॅफाइट यांत समतापी (त्याच तापमानाला) रूपांतरण होते. त्यानंतर कोठी (सर्वसाधारण) तापमानापर्यंत मिश्रधातू थंड करीत गेल्यास आणखी काहीही बदल होत नाहीत.
अंतिम संरचनेला फेराइटी करडे बीड म्हणतात. हा करड्या बिडाचा सर्वांत मृदू प्रकार आहे. त्यातील ग्रॅफाइट पत्र्यांच्या उपस्थितीमुळे त्याची संरचना खंडित स्वरूपाची झाल्याने त्याचे शरण बल (ताणाखाली ठराविक प्रमाणात प्रतिविकृती निर्माण होण्यासाठी लागणारे प्रतिबल) १,०५५ ते १,७६० किग्रॅ./सेंमी.२ असून तन्यता जवळजवळ नसते. मिश्रधातूचे घनीभवन होत असताना ग्रॅफाइट पत्र्या तयार होण्याचे कारण सिलिकॉनची उपस्थिती व सापेक्षतः कार्बनाचे उच्च प्रमाण हे असून त्यामुळे विद्रावात लोखंडाबरोबर धारण करता येणे शक्य असलेल्यापेक्षा अधिक कार्बनाचा समावेश होतो.
जर हीच मिश्रधातू पुन्हा वितळविली व जराशा जास्त वेगाने शीतलन केले, तर निर्माण होणारी संरचना फेराइटी बिडापेक्षा निराळी असते. या मिश्रधातूचे ७२३° से. तापमानातून शीतलन केले, तर ऑसेनाइटाचे फेराइट व ग्रॅफाइट यांत अपघटन होण्यास पुरेसा वेळ मिळत नाही. याऐवजी त्याचे लोखंड व आयर्न कार्बाइड (Fe3C) यांच्या तांत्रिक मिश्रणात रूपांतर होते. या विक्रियेला घनक्रांतिकाभ विक्रिया म्हणतात व मिश्रणाला पिअरलाइटी करडे बीड म्हणतात. हे मिश्रण फेराइटी बिडापेक्षाही कमी तन्य असते कारण पिअरलाइटी संरचना फेराइटी संरचनेपेक्षा कठीण असते व तीत फेराइटी प्रकाराप्रमाणेच पत्रीरूप ग्रॅफाइट उपस्थित असते. याचे ताणबल (ताणलेल्या स्थितीत न फाटता सहन करू शकणारे महत्त्म प्रतिबल) १,४०५ ते २,८१० किग्रॅ./ सेंमी.२ असते.
करड्या बिडाचे सहजपणे यंत्रण (कापण्याच्या व घासण्याच्या विविध क्रिया) करता येते. त्यातील ग्रॅफाइटामुळे ते सापेक्षतः ‘मृत द्रव्य’ समजले जाते म्हणजे ते कंपनांचे शोषण करते. यामुळे त्याचा उपयोग यांत्रिक हत्यारे, मोटारगाडीतील सिलिंडर संच आणि दृढता, चांगले संपीडन बल (न फाटता सहन करू शकणारे महत्तम संकोचक प्रतिबल) तसेच ओतकाम व यंत्रण यांची सुलभता असलेली मिश्रधातू आवश्यक असलेल्या अनेक विविध बाबी यांच्या निर्मितीत करण्यात येतो.
थंड केलेले बीड : नवीनच घनीभूत झालेले करडे बीड शीघ्र वेगाने थंड केल्यास या प्रकारचे बीड तयार होते. शीघ्र वेगाने थंड केल्यामुळे करड्या बिडाची विविध रूपांतरणे होण्यास पुरेसा वेळ मिळू दिला जात नसल्याने मिळणाऱ्या अंतिम पदार्थाची संरचना पूर्णपणे आयर्न कार्बाइडाची होते. थंड केलेले बीड ठिसूळ व काचेसारखे कठीण असते. ते काही प्रकारच्या रेल्वेच्या डब्यांच्या चाकांचा व काचेसारखे बाह्य पृष्ठभाग, गतिरोधकाचा (ब्रेकचा) घर्षण होणारा भाग, दगडांचा चुराडा करणारे यंत्र व यांसारख्या इतर अपघर्षक उपयोगांकरिता वापरण्यात येते.
पांढरे बीड : बिडातील कार्बन व सिलिकॉन यांचे प्रमाण कमी करून हा प्रकार तयार करण्यात येतो. ग्रॅफाइट तयार होण्यास कमी कार्बन उपलब्ध असल्याने व ते तयार होण्यास उत्तेजन देणाऱ्या सिलिकॉनाचेही प्रमाण कमी असल्याने हे बीड थंड झाल्यावर त्यांचे संघटन पूर्णपणे आयर्न कार्बाइडाचे असते. नमुनेदार पांढऱ्या बिडाचे संघटन २.५% कार्बन, १.०% सिलिकॉन, ४.५% मँगॅनीज, ०.१८% फॉस्फरस व ०.१६% गंधक असे आढळते. पांढऱ्या बिडाची धातुरचना वैज्ञानिक परीक्षा केल्यास त्यात ग्रॅफाइट आढळत नाही परंतु कमी व बदलत्या प्रमाणात पिअरलाइट आणि प्रमुख घटक म्हणून आयर्न कार्बाइड आढळते. पांढरे बीड थंड केलेल्या बिडाप्रमाणेच अपघर्षण उपयोगांकरिता वापरले जाते पण त्याचा मुख्य उपयोग वर्धनशील बिडात रूपांतर करण्यासाठीच होतो.
वर्धनशील बीड : हे बीड मृदू, तन्य व कार्बनाचे प्रमाण कमी असलेल्या पोलादाइतके यंत्रणक्षम असून त्याचे ताणबल ४,२२० ते ७,०३० किग्रॅ./सेंमी.२ यांच्या दरम्यान असते. ते मोटारगाडी व रेल्वे उद्योगांत वापरले जाते तसेच नळांचे जोडकाम, विद्युत् चलित्राचे (मोटरचे) प्रावरण, हार्डवेअर (जोडकामाची साधने, कटलरी, हत्यारे, यंत्रांचे भाग, बांधकामातील धातवीय सामग्री वगैरे), यांत्रिक हत्यारे आणि सुलभ घडाई, बल व बेताची तन्यता लागणाऱ्या वस्तू तयार करण्यासाठी वापरतात.
पांढऱ्या बिडांवर उष्णता संस्करण करून वर्धनशील बीड बनवितात. यांच्या उत्पादनाची सुरुवात वाळूच्या साच्यांत पांढऱ्या बिडाची ओतिवे तयार करून होते. ओतिवांचे घनीभवन होत असताना मुक्त ग्रॅफाइट तयार होणार नाही असे पांढऱ्या बिडाचे संघटन असणे आवश्यक असते. थंड झाल्यावर कठीण, ठिसूळ, पांढऱ्या बिडाची ओतिवे साच्यांतून काढून स्वच्छ करतात व मग योग्य भट्ट्यांत उष्णता संस्करणासाठी भरतात. वर्धनीकरणाच्या अनेक चक्रांपैकी संस्करणासाठी वापरलेल्या चक्रानुसार त्याला लागणारा एकूण कालावधी २५ ते १०० तास असू शकतो. या संस्करणासाठी नैसर्गिक हवेच्या झोताचा उपयोग करणाऱ्या किंवा नियंत्रित वातावरण ठेवलेल्या भट्ट्या वापरतात.
भट्टीत आयर्न कार्बाइड म्हणून घातलेली पांढऱ्या बिडाची ओतिवे सु. ९२५°से. पर्यंत तापवितात आणि वापरलेल्या वर्धनीकरणाच्या चक्रानुसार याच तापमानाला १० ते २० तास ठेवतात. ९२५°से. तापमानावर कार्बनाचे विसरण होऊन आयर्न कार्बाइडाचे हळूहळू ऑस्टेनाइटात व ग्रॅफाइटात रूपांतर होते. वर्धनशील बीड व करडे बीड यांतील मुख्य फरक तयार होण्यास लागणारा काळ व ग्रॅफाइटाचा आकार यांत आहे. करड्या बिडात घनीभवनानंतर ग्रॅफाइट पत्रीरूपात जलद अवक्षेपित होते व त्यामुळे लोखंडाचा ठिसूळ प्रकार तयार होतो. वर्धनीकरणाच्या तापन काळात आयर्न कार्बाइडातील कार्बन अणूंचे विसरण होऊन ते स्वैर वितरण झालेल्या ग्रॅफाइटाच्या ‘गुलाबाच्या फुलां’सारख्या पुंजक्यांच्या रूपात गोळा होतात. यानंतर तापमान ऑस्टेनाइटाचे पिअरलाइटात रूपांतर होणाऱ्या तापमानाच्या (७२३°से.) जरा वर इतक्या तापमानापर्यंत कमी करतात. शीतलन चक्राचे तापमान सामान्यतः सु. ७६०° से.पर्यंत कमी करतात आणि ७२३°से. खालील अंतिम शीतलन क्रियेला १० ते २० तास लागतील अशा प्रकारे ती नियंत्रित करतात.
पिअरलाइट तयार होण्याच्या तापमानातून सावकाश शीतलन केल्यामुळे ऑस्टेनाइटाचे अपघटन पिअरलाइटात होण्याऐवजी फेराइट व ग्रॅफाइट यांत होते. अंतिमतः मिळणाऱ्या धातूला फेराइटी वर्धनशील बीड म्हणतात. त्याचे ताणबल सु. ३,८७० किग्रॅ./सेंमी.२ असते व तन्यता १५% प्रसरण इतकी असते. करड्या बिडातील ग्रॅफाइटाचा आकार पत्रीरूप असतो, तर वर्धनशील बिडातील ग्रॅफाइटाचा आकार साधारण गोलाभ असतो. यामुळे वर्धनशील बिडातील ग्रॅफाइट हे ग्रॅफाइट पत्रीप्रमाणे काम करीत नाही व त्यामुळे बल कमी न होता या बिडाला खूप अधिक तन्यता प्राप्त होते.
जर तशाच पांढऱ्या बिडाच्या ओतिवाचे फेराइट संरचना तयार होणाऱ्या तापन चक्रातूनच पण ७६०°सें.ला अटकाव न करता ७२३° से.च्या खाली अधिक शीघ्र शीतलन केले, तर ऑस्टेनाइटाचे फेराइट व ग्रॅफाइट यांत अपघटन होण्यास पुरेसा वेळ मिळत नाही, त्याऐवजी त्याचे पिअरलाइटात रूपांतर होते. यात मिळणारी अंतिम धातू पिअरलाइट व गुलाब फुलांसारखे पुंजके असलेले ग्रॅफाइट या स्वरूपात असते आणि तिला पिअरलाइटी वर्धनशील बीड म्हणतात. पिअरलाइट हा घटक फेराइटापेक्षा काहीसा कठीण असल्याने या बिडाची तन्यता फेराइटी वर्धनशील बिडाच्या १/३ असते, तर ताणबल ५,२७५ ते ७,०३० किग्रॅ./सेंमी.२ यांच्या दरम्यान असते.
गाठीयुक्त बीड : बिडाचा हा सर्वांत अलीकडे विकसित करण्यात आलेला प्रकार सु. १९४० पासून वाढत्या प्रमाणात वापरला जात आहे. याला तन्य बीड असेही म्हणतात. करड्या बिडापेक्षा यातील कार्बन व सिलिकॉन यांचे प्रमाण थोडेसे अधिक असते पण गंधकाचे प्रमाण कमी असते. वितळलेले गाठीयुक्त बीड सरळ वर्धनशील प्रकारच्या ओतिवात रूपांतरित होते व त्याकरिता उष्णता संस्करणाची आवश्यकता नसते. वर्धनशील बीड ज्या क्षेत्रांत वापरले जाते, त्यांपैकी अनेक क्षेत्रात गाठीयुक्त बीड वापरण्यात येते परंतु तांत्रिक व आर्थिक कारणांमुळे रूढ वर्धनशील बिडाची जागा ते कदाचित घेऊ शकणार नाही.
गाठीयुक्त बिडाचे ओतीव तयार करण्यासाठी करड्या वा वर्धनशील बिडाच्या ओतिवाप्रमाणेच साचा तयार करण्यात येतो आणि मिश्रधातू उभ्या वा इतर प्रकारच्या धातू वितळविण्याच्या भट्टीत वितळवितात. वितळलेली धातू वाळूच्या साच्यात अगदी ओतण्यापूर्वी तीत सिरियम व मॅग्नेशियम या धातू मिश्रधातूच्या रूपात अंतर्भूत केल्या जातात. वितळलेली धातू साच्यात ओतल्यानंतर ओतीव घनीभवनाच्या तापमानाजवळ येऊ लागताना द्रवातून ग्रॅफाइटाचे अवक्षेपण होण्यास प्रारंभ होतो परंतु नेहमीप्रमाणे ग्रॅफाइटाच्या पत्र्या तयार न होता त्याचे केंद्रकीकरण होऊन छोट्या गाठींच्या रूपात त्याची वाढ होते. या गाठी वर्धनशील बिडातील गुलाबपुष्पी पुंजक्यांपेक्षा अधिक गोलाभ आकाराच्या असतात. सिरियम अथवा मॅग्नेशियम मिश्रधातूचा निवडलेल्या धातूत अंतर्भाव केल्याने द्रवात अविद्राव्य असलेले (न विरघळणारे) ऑक्साइड कण तयार होतात व ते ग्रॅफाइटाच्या गाठी तयार होण्यासाठी केंद्रके पुरवितात, असे सामान्यतः मानण्यात येते.
गाठीयुक्त बिडाचे ताणबल सरासरीने सु. ५,६०० किग्रॅ./सेंमी.२ असते व ओतिवाच्या रूपातील तन्यता ३% प्रसरण इतकी असते. याचे अनुशीतन (जरूर तितके तापवून मग सावकाश केलेले शीतन) केल्यास तन्यता तिप्पट वाढते पण ताणबल सु. ४,२०० किग्रॅ./सेंमी.२ इतके कमी होते. करड्या व गाठीयुक्त या दोन्ही प्रकारच्या बिडांचे ताणबल द्रुतशीतनाने व पाणी देऊन वाढविता येते. काही विशिष्ट गुणधर्म वाढविण्यासाठी वा दडपून टाकण्यासाठी बिडाचे सर्व प्रकार मिश्रधातू रूपात वापरलेले आढळतात.
जागतिक उद्योग : लोखंड व पोलाद उद्योगाचा मूलभूत भाग म्हणजे झोतभट्टीत पिग लोखंड तयार करणे हा आहे. झोतभट्टीचा उपयोग करण्यासाठी धातुक, इंधन, चुनखडी व पाणी यांचा विपुल पुरवठा आवश्यक असतो. लोखंडनिर्मितीत वाहून न्यावयाचे प्रचंड वजन व त्यासाठी लागणारा वाहतूक खर्च लक्षात घेता औद्योगिकीकरण करण्याचे उद्दिष्ट असलेल्या कोणत्याही देशात पुरेशी साधनसंपत्ती असणे ही मूलभूत महत्त्वाची गोष्ट आहे. लोह धातुकाचा व इंधनाचा आता जगभर व्यापार केला जातो. जपानमध्ये लोखंड तयार करण्यासाठी ऑस्ट्रेलियातील धातुकाचा व अमेरिकेतील पश्चिम व्हर्जिनियामधील कोळशाचा उपयोग केला जातो. जपान हे या उद्योगात आढळणाऱ्या परिस्थितीचे एक टोकाचे उदाहरण आहे. धातुकाचे व कोळशाचे मोठे साठे बहुधा जवळजवळ आढळत नाहीत. यांपैकी एक किंवा दोन्ही लोखंडनिर्मिती केंद्राकडे वाहून न्यावे लागतात. जलवाहतूक ही बोजड माल वाहून नेण्याची सर्वांत काटकसरीची पद्धत आहे, असे आतापावेतो दिसून आले आहे. एकदा माल तरंगता झाल्यावर वाहून न्यावयाच्या अंतराला तितकेसे महत्त्व राहत नाही. जपानला जागतिक बाजारेपेठेत स्पर्धा करणे शक्य होण्याचे हे एक कारण आहे. अमेरिकेतील लोखंड व पोलाद उद्योग महासरोवरांपाशी केंद्रित होण्याचेही हेच कारण आहे. मिनेसोटा व कॅनडा येथून जहाजाने धातुक खालच्या सरोवरांवरील बंदरात आणले जाते. कोळसा जवळच असून तो रेल्वेने आणला जातो. अमेरिकेच्या संयुक्त संस्थानांतील इतर महत्त्वाची पोलादनिर्मिती केंद्रे आयात धातुक सुलभपणे उतरविता येणाऱ्या व पोलादाची मोड भरपूर प्रमाणात उपलब्ध असलेल्या पूर्व व पश्चिम किनाऱ्यांवरील ठिकाणी आहेत.
औद्योगिक युगात लोह धातुकाचा प्रचंड प्रमाणावर उपयोग करण्यात आलेला असला, तरी ते विपुल प्रमाणात उपलबध असून नजीकच्या भविष्यकाळात धातुकाच्या तुटवड्यामुळे लोखंडाच्या उत्पादनावर मर्यादा येतील, असे दिसत नाही. तथापि जेथील स्थानिक उच्च दर्जाचे लोह धातुक साठे संपलेले आहेत तेथील उत्पादकांना आपले कारखाने अन्यत्र हालवावे लागले आहेत अगर धातुकाच्या पुरवठ्याच्या नवीन उद्गमांची व्यवस्था करणे भाग पडले आहे. १९५० सालाच्या अगोदर अमेरिकेच्या संयुक्त संस्थानांत फारच थोडे धातुक आयात करण्यात येत होते पण त्यानंतर परदेशी धातुकाच्या उपयोगाचे प्रमाण क्रमशः वाढत गेले आणि धातुक पुरवठ्याचा तो एक महत्त्वाचा भाग झालेला आहे. अमेरिकेच्या संयुक्त संस्थानांना धातुकाचा पुरवठा करणारे कॅनडा व व्हेनेझुएला हे महत्त्वाचे देश आहेत. लोह धातुकाच्या विविध देशांतील उत्पादनाची आकडेवारी कोष्टक क्र.१ मध्ये दिली आहे.
लोखंड व पोलाद उद्योगाच्या सातत्याने होणाऱ्या वाढीची मुख्य कारणे जागतिक दृष्टिकोनातून पाहिले असता समृद्धीकरण व संहतीकरण केलेल्या धातुकांचा वाढता उपयोग आणि झोतभट्टीची सातत्याने वाढत असलेली कार्यक्षमता ही आहेत. एकाच झोतभट्टीचा उत्पादन वेग सरतेशेवटी दर दिवशी ४,००० टनांपर्यंत वितळलेले पिग लोखंड येथपर्यंत जाईल असा अंदाज आहे. कोष्टक २ मध्ये जगातील विविध देशांतील लोखंडाचे उत्पादन दिले आहे.
कोष्टक क्र. २ विविध देशांतील पिग लोखंडाचे उत्पादन (हजार टनांत). | ||
देश | १९७० | १९८० |
अमेरिकेची संयुक्त संस्थाने
ऑस्ट्रेलिया इटली कॅनडा चीन चेकोस्लोव्हाकिया जपान जर्मनी, पश्चिम दक्षिण आफ्रिका पोलंड फ्रान्स बेल्जियम ब्राझील भारत रशिया रुमानिया |
८५,३०३
५,७६९ ८,५२९ ८,४२४ २२,००० ७,६१३ ६९,७२८ ३३,८९७ ४,३२८ ७,१११ १९,५७५ १० ,९५० १९,०२७ ७,३३८ ८५,९३३ ४,२१० |
६३ ,७४६
७,२७६ १२,४४१ ११,१८५ ३८,००० १०,०५१ ८८,९० ७ ३४,७५५ ७,८९५ ११,६८२ १९,६३६ ९,८४५ ६,४१३ ८,७७० १,०७,९७३ ९,०१३ |
एकूण जागतिक | ४,४१,७८७ | ५,२५,७७३ |
लोखंड उद्योगाच्या नजीकच्या व दीर्घकालीन भविष्यावर अनेक घटकांचा ठळक परिणाम होतो. दीर्घकाल प्रस्थापित झालेल्या धातुक्षपणक केंद्राच्या क्षेत्रांतील नेहमीच्या धातुकांचे कमी होत चालेलेले साठे आणि अधिक समृद्ध साठे असलेल्या अधिक दूरवरच्या प्रदेशांकडे झालेले उद्योगाचे स्थानांतरण यांमुळे उत्पादकांवर फारसा गंभीर परिणाम झालेला नाही. याचे कारण म्हणजे विकसित करण्यात आलेल्या धातुक समृद्धीकरणाच्या तंत्रांमुळे क्षपणक-केंद्रांकडे धातुक वाहून नेण्याच्या खर्चाची भरपाई होते. कित्येकदा अनेक किमी. दूरच्या ठिकाणाहून वाहून आणलेले व समृद्धीकरण केलेले पिग लोखंड तयार करण्यासाठी वापरावयाचे धातुक जवळपासव्या उद्गमापासून सरळ उपयोगात आणावयाच्या धातुकावर प्रक्रिया करण्यापेक्षा स्वस्त पडते.
लोखंड ज्या परंपरागत क्षेत्रांत वापरले जाते, त्या क्षेत्रांवर इतर पदार्थांनी (विशेषतः ॲल्युमिनियम व काँक्रीट यांनी) आक्रमण केल्याने लोखंडाच्या उत्पादनावर केवळ अल्प परिणाम झालेला आहे. उदा., लोखंडाच्या बाजारपेठेतील ॲल्युमिनियमाचा वाटा इ.स. २००० पर्यंत १७ टक्क्यांपर्यंत वाढेल, असा अंदाज व्यक्त करण्यात आलेला होता, तथापि १९८५ च्या सुमारास हा वाटा फक्त ६% इतकाच होता. रासायनिक उद्योगातील अनेक अधातवीय द्रव्येही (उदा., प्लॅस्टिके) लोखंडाच्या उपयोगावर अतिक्रमण करीत आहेत. इतर पदार्थांनी स्पष्टपणे मिळविलेल्या लाभाचा प्रतिकार करण्यासाठी व लोकसंख्येतील वाढीशी जुळवून घेण्यासाठी लोखंडाचे उत्पादन पुढील १० वर्षात जवळजवळ दुप्पट होणे आवश्यक आहे, असा अर्थतज्ञांचा अंदाज होता.
एके काळी अशी भीती व्यक्त करण्यात येत होती की, लोखंडाची बाजारपेठ संतृप्त परिस्थितीकडे वाटचाल करीत आहे आणि ग्राहकांची मागणी कच्च्या पिग लोखंडाच्या उत्पादनाऐवजी लोखंड व पोलाद पुन्हा वितळवून तयार करण्यात येणाऱ्या प्रकारांच्या वाढत्या उत्पादनाने भागविली जाईल, तथापि सतत होणाऱ्या आर्थिक वृद्धीमुळे आणि लोखंड व पोलाद यांचे नवनवीन उपयोग दिसून आल्यावर ही भीती दूर झाली. लोखंड व पोलाद उद्योगाने कमा उत्पादकतेची अवस्था गाठलेली असून त्याची कार्यक्षमता व उत्पादन वाढविण्यासाठी फारसे काही करता येणे शक्य नाही, असेही वाटत होते परंतु नंतर हाती घेतलेल्या वेगवान संशोधन कार्यक्रमांमुळे असे दिसून आले की, उच्च दर्जाच्या धातुकांत घट झाल्याने लोखंड उद्योगाचा अपकर्ष सूचित होण्याऐवजी वाढत्या उत्पादनाच्या कार्यक्रमांना चालना मिळाली. समृद्धीकरण केलेल्या धातुकाच्या (विशेषतःगुलिका, तापपिंड व पूर्ण-क्षपण केलेल्या धातुकांच्या) वाढत्या उपयोगामुळे झोतभट्टीची उत्पादकता वाढण्याबरोबरच भट्टीला लागणाऱ्या कोकच्या प्रमाणात घट झाली आहे. उच्च भट्टी तापमान, ऑक्सिजनसंपन्न हवेचा झोत व पूरक इंधनांचे अंतःक्षेपण यांच्या उपयोगामुळे उत्पादन वेग दुप्पट झाला. स्वयंचलित व संगणकयुक्त सुविधांमुळे यंत्रसामग्रीच्या कार्यक्षम उपयोगात आणखी वाढ झालेली आहे. पोलादी पट्ट्यांच्या लाटणाचे नियंत्रण, झोतभट्टीचे कार्य, कामाचे वेळापत्रक तयार करणे वगैरे विविध कामांसाठी संगणकाचा उपयोग करण्यात येत असल्याने मजुरीत खूप बचत होते. अखंड प्रक्रियांच्या देखरेखीसाठी उच्च-वेगी संगणक नियंत्रण आवश्यक असते आणि यामुळे अखंड पोलाद उत्पादनाचे एक सर्वांत आशादायक तंत्र क्षारकीय ऑक्सिजन पद्धतींवर आधारलेले आहे.
पोलादाचे उत्पादन सतराहून अधिक देशांत होते. १९८० नंतरच्या दशकाच्या प्रारंभी कच्च्या पोलादाचे जागतिक वार्षिक उत्पादन सु.७८ कोटी टन होते. त्यांपैकी सु. १४.८ कोटी टन रशियाचे, ११ कोटी टन अमेरिकेच्या संयुक्त संस्थानांचे व ११.१ कोटी टन जपानचे होते. यांखेरीज यूरोपीय आर्थिक संघातील देशांचे एकूण उत्पादन १२.७ कोटी टन होते. जागातील काही प्रमुख पोलाद उत्पादक देशांचे १९७० व १९८० या सालांचे उत्पादन कोष्टक क्र. ३ मध्ये दिले आहे.
कोष्टक क्र. ३ काही प्रमुख उत्पादक देशांतील कच्च्या पोलादाचे
(पोलादी पिंड व ओतिवे यांचे) उत्पादन (हजार टनांत). |
||
देश | १९७० | १९८० |
अमेरिकेची संयुक्त संस्थाने
ऑस्ट्रेलिया इटली कॅनडा चीन चेकोस्लोव्हाकिया जपान जर्मनी, पश्चिम दक्षिण आफ्रिका पोलंड फ्रान्स बेल्जियम ब्राझील ब्रिटन भारत रशिया रूमानिया |
१,१९,३०९
६,८७४ १७,२७७ ११,१९८ १८,००० ११,४८० ९३ ,३२८ ४५,०४० ४,६७४ ११,७५० २३ ,७७३ १२,६०९ ५,३९० २८,३१६ ६,२८६ १,१५,८८९ ६,५१७ |
१,०१,४५६
७,८१५ २६,५०१ १५,९०१ ३७,१२० १५,२२५ १,११,३९५ ४३,८३८ ८,९५९ १८,६४८ २३,१७६ १२,३२३ १०,२३२ ११,२७७ ९,३२७ १,४७,९४१ १३,१७५ |
एकूण जागतिक | ५,९४,००१ | ७,०६,४७२ |
प्रमुख पोलाद उत्पादक देशांतील पोलाद उत्पादनाचा कोष्टक क्र. ३ मधील अलीकडील आकडेवारीवरून पोलादाच्या वार्षिक उत्पादनातील कल दिसून येतो. दीर्घकाळ प्रस्थापित झालेला पोलाद उद्योग असलेल्या देशांतील उत्पादन अलीकडच्या काळात फारसे वाढलेले नाही. काहींच्या बाबतीत तर ते कमीही झालेले आहे. अमेरिकेची संयुक्त संस्थाने, पश्चिम जर्मनी व फ्रान्स या देशांतील उत्पादन घटले, तर रशिया व जपान या देशांतील उत्पादनात लक्षणीय वाढ झाली. कोष्टक क्र. ३ मधील पोलाद उत्पादनाची आकडेवाडी व कोष्टक क्र. १ मधील लोहधातुकाच्या उत्पादनाची आकडेवाडी यांची तुलना केल्यास विविध देशांतील पोलाद उद्योगाची वैशिष्ट्ये समजून येतील. रशियातील पोलाद उद्योग स्पष्टपणे स्वावलंबी आहे, तर अमेरिकेच्या संयुक्त संस्थानांतील उद्योग आयात धातुकांवर लक्षणीय मर्यादेपर्यंत अवलंबून आहे. जपानचा धातुक उत्पादकांत समावेशही होत नाही, तर ऑस्ट्रेलियातील धातुक उत्पादन जलद वाढलेले असूनही त्याच्या पोलाद उत्पादनात लक्षणीय वाढ झालेली आढळत नाही. वस्तुत: जपान ऑस्ट्रेलियातून धातुक आणि कोक तयार करण्यायोग्य कोळसा अमेरिकेची संयुक्त संस्थाने व ऑस्ट्रेलिया येथून आयात करतो. जपानी पोलादापैकी बरेचसे नंतर कच्च्या मालाच्या वा तयार मालाच्या रूपात धातुक व कोळसा पुरविणाऱ्या देशांना निर्यात केले जाते.
अमेरिकेच्या संयुक्त संस्थानांतील २०० हून अधिक कंपन्या लोखंड व पोलाद उद्योगात गुंतलेल्या आहेत. यांतील जवळजवळ निम्म्या कंपन्या लाटून वा घडवून वस्तू तयार करण्यासाठी लागणाऱ्या कच्च्या पोलादाचे उत्पादन करतात. इतर कंपन्यांपैकी बहुतांशी कच्च्या पोलादापासून वा अर्धरूपण केलेल्या पोलादापासून (लांबट ठोकळ्याच्या आकाराचे धातुखंड व लाद्या यांपासून) अंत्यरूपण केलेल्या वस्तू तयार करतात. दुसऱ्या महायुद्धाच्या अखेरीस अमेरिकेच्या संयुक्त संस्थानांचा जागतिक पोलाद उत्पादनातील वाटा निम्म्याहून अधिक होता परंतु त्यानंतर हा वाटा पुष्कळच कमी झाला. १९८० नंतरच्या दशकाच्या प्रारंभी या देशाचा जागतिक एकूण उत्पादनातील वाटा केवळ १५ टक्क्यांहून थोडा अधिक होता. या काळात तेथील पोलाद उद्योगाला अनेक अंतर्गत व परकीय प्रश्नांना तोंड द्यावे लागले. खालावत चाललेली संयंत्रे व जुनी होत चाललेली तंत्रविद्या यांच्याबरोबरच संपांची मालिका आणि कामगार, सामग्री व वाहतूक यांच्या खर्चातील जलद वाढ हे त्यांपैकी काही प्रश्न होते. यामुळे परदेशी पोलादाच्या आयातीत वाढ होण्यास मदत झाली. १९८० नंतरच्या दशकाच्या आरंभी तेथे वापरण्यात येत असलेल्या कच्च्या पोलादापैकी जवळजवळ २०% आयात करण्यात येत होते. वरील प्रश्नांना तोंड देण्यसाठी पोलाद उद्योगाने कामगार संघटनांकडून वेतन मागण्या कमी करण्यासंबंधी आणि काँग्रेसकडून व्यापार विषयक कायदे सुधारणे व उत्पादन खर्चापेक्षा कमी किंमती असलेल्या पोलादाच्या आयातीवर नियंत्रण आणणे यांसबंधी प्रयत्न केले. त्याचबरोबरच कालबाह्य यंत्रे व फायदेशीर नसलेली उत्पादने काढून टाकण्यात आली आणि नवीन संयंत्रांत व अधिक तंत्रविद्येत गुंतवणूक वाढविण्यात आली. उदा.,१९६० नंतरच्या दशकाच्या मध्यास जवळजवळ ७५% कच्चे पोलाद खुल्या चुल्याच्या भट्ट्यांत व २० टक्क्यांपेक्षा कमी अधिक आधुनिक असलेल्या क्षारकीय ऑक्सिजन भट्ट्यांत तयार केले जात होते. तथापि १९८० नंतरच्या दशकाच्या आरंभी सु. ६१% क्षारकीय ऑक्सिजन भट्ट्यांत, तर फक्त सु. ११% खुल्या चुल्याच्या भट्ट्यांत कच्चे पोलाद तयार करण्यात येत होते. याखेरीज उद्योगाने आपल्या उत्पादनांत विविधता आणण्याचा व परदेशी तज्ञांचे अधिक तांत्रिक साहाय्य मिळविण्याचा प्रयत्न करण्यास प्रारंभ केला. १९८० नंतरच्या दशकाच्या आरंभी अमेरिकेच्या संयुक्त संस्थानांत दर वर्षी १० कोटी टनांपेक्षा थोड्याशा अधिक वजनाची पोलादाची उत्पादने वापरण्यात येत होती. यांपैकी जपानकडून ६२ लक्ष टन, यूरोपीय आर्थिक संघाकडून ६५ लक्ष टन व कॅनडाहून २९ लक्ष टन आयात करण्यात येत होती. राहिलेल्या ४३लक्ष टन आयातीपैकी बहुतांशी दक्षिण आफ्रिका, स्पेन, ब्राझील, दक्षिण कोरिया, बेल्जियम, लक्सेंबर्ग व पश्चिम जर्मनी या देशांकडून करण्यात येत होती. दुसऱ्या महायुद्धानंतर तेथे पोलादाच्या उत्पादनांना वाढती बाजारपेठे मिळाली असली, तरी बहुतेक वाढीव मागणीचा पुरवठा परदेशांतूनच करण्यात आला.
रशियाचे पोलाद उत्पादन १९५० नंतर जलद गतीने वाढले आणि १९७० नंतरच्या दशकाच्या अखेरीच्या काळात रशिया कच्च्या पोलादाचा अग्रेसर उत्पादक झाला व जागतिक पुरवठ्यातील त्याचा वाटा सु. १७% होता. जपानच्या (अमेरिकेच्या संयुक्त संस्थानांनंतर) पोलाद उत्पादनात तिसरा क्रमांक होता व जागतिक पुरवठ्यातील त्याचा वाटा १२% होता. जपानचा बहुतेक सर्व पोलाद उद्योग दुसऱ्या महायुद्धानंतर उभारण्यात आल्याने त्यातील संयंत्रे व साधनसामग्री आधुनिक व कार्यक्षम आहेत. तसेच त्यांत वापरण्यात येणारा माल व जहाज वाहतूक यांच्या सुविधा संयंत्रांच्या जवळपास असल्याने कर्मचाऱ्यांना जास्त वेतने देऊन सुद्धा जपानला उत्पादकता वाढविणे व खर्च आवाक्यात ठेवणे शक्य झाले.
पश्चिम यूरोपातील फ्रान्स, पश्चिम जर्मनी, इटली, बेल्जियम, नेदर्लंड्स व लक्सेंबर्ग या पोलाद उत्पादक देशांनी १९५० मध्ये यूरोपीय कोळसा व पोलाद संघ स्थापन केला. या संघाचे पुढे १९५७ मध्ये यूरोपीय आर्थिक संघात रूपांतर झाले. या नऊ सदस्य देशांच्या संघाचा जागतिक कच्च्या पोलादाच्या पुरवठ्यातील वाटा आता सु. १६% आहे. चेकोस्लोव्हाकिया, पोलंड, रूमानिया, स्पेन, पूर्व जर्मनी. ऑस्ट्रिया व स्वीडन हे महत्त्वाचे पोलाद उत्पादक देश असून त्यांचे उत्पादन प्रत्येकी ४० लक्ष टनांपेक्षा जास्त आहे.
ब्रिटिश पोलाद उद्योगावर राजकीय निर्णयांचा व श्रम वाचविणाऱ्या पद्धतींचा स्वीकार करण्यास कामगारांनी दर्शविलेल्या नकाराचा वाईट परिणाम झाला. दुसऱ्या महायुद्धानंतर पोलाद उद्योगाचे राष्ट्रीयीकरण, खाजगीकरण व पुन्हा राष्ट्रीयीकरण करण्यात आले. १९६७ च्या लोखंड व पोलाद अधिनियमानुसार कच्च्या पोलादाचे उत्पादन करणाऱ्या १४ मोठ्या कंपन्यांच्या मालकीचे ब्रिटिश स्टील कॉर्पोरेशनकडे हस्तांतरण करण्यात आले. या कॉर्पोरेशनने घेतलेला कोणताही निर्णय संसदेपुढे ठेवावा लागतो.
कम्युनिस्ट देशांतील पोलाद उद्योगाचे व्यवस्थापन सामान्यतः केंद्र सरकारच्या मंत्रालयातर्फे (उदा., रशियातील पोलाद मंत्रालयातर्फे) करण्यात येते.
अतिपूर्वेकडील दक्षिण कोरिया, राष्ट्रीय चीन (तैवान) व सिंगापूर येथील पोलाद उत्पादन महत्त्वाचे बनले आहे. तथापि जपानचा अपवाद सोडल्यास प्रजासत्ताक चीनमध्ये कच्च्या पोलादाचे सर्वांत जास्त उत्पादन (१९८०मध्ये ३.७ कोटी टन) होते. १९८० मध्ये भारतात ९३ लक्ष टन, तर ऑस्ट्रेलियात ७८ लक्ष टन उत्पादन झाले.
अमेरिकेच्या संयुक्त संस्थानांच्या खालोखाल दुसऱ्या क्रमांकाचे कॅनडाचे कच्च्या पोलादाचे उत्पादन असून १९८१ मध्ये ते १.४६ कोटी टन होते. लॅटिन अमेकिरेत १९८१ मध्ये २.७३ कोटी टन कच्च्या पोलादाचे उत्पादन झाले आणि ब्राझील, व्हेनेझुएला व मेक्सिको हे तेथील प्रमुख उत्पादन देश आहेत. आफ्रिकेत आतापावेतो सर्वांत मोठा उत्पादक देश दक्षिण आफ्रिका आहे.
जगातील काही प्रमुख देशांतील पोलादाचा औद्योगिक वापर व दरडोई वापर यांची माहिती कोष्टक क्र.४ मध्ये दिली आहे.
कोष्टक क्र.४ काही प्रमुख देशांतील पोलादाचा औद्योगिक वापर (हजार टनांत) व दरडोई वापर (किग्रॅ.मध्ये). | ||||
देश | देशऔद्योगिक वापर | दरडोई वापर | ||
१९७० | १९८० | १९७० | १९८० | |
अमेरिकेची संयुक्त संस्थाने
इटली कॅनडा कोरिया, उत्तर कोरिया, दक्षिण चीन चेकोस्लोव्हाकिया जपान जर्मनी, पश्चिम जर्मनी, पूर्व दक्षिण आफ्रिका नेदर्लंड्स पोलंड फ्रान्स ब्राझील ब्रिटन भारत मेक्सिको रशिया रुमानिया स्पेन स्वीडन |
१,२७,३०४
२१,११३ ११,०८५ २,३३६ १,०५० २२,५०४ ८,८३८ ६९,८८२ ४०,६०१ ९,०८० ४,७८३ ५,६६८ ११,६८४ २३,२३६ ६,०८८ २५,५३९ ६,४३२ ४,१६८ १,१०,२३४ ६,४३० ८,५४४ ५,९९० |
१,१५,५९१
२६,१०७ १२,२३९ ५,८६९ १०,९४१ ४३,२६२ ११,१५४ ७३,४४२ ३३,७८३ ९,७५२ ६,७४६ ४,६३३ १८,७५० २०,०४८ १६,२४१ १३,७८३ ११,०७२‡ १०,५६७ १,४१,०३१* १२,११५ ८,७३ ४,१३९ |
६२०
३९३ ५२० १६१ ३३ २९ ६११ ६७६ ६६० ५३३ २०९ ४३५ ३५६ ४५७ ६४ ४५८ १२ ८२ ४५४ ३१७ ८,७३१ ७३३ |
५०८
४५८ ५४१ ३२८ २८६ ४५ ७२९ ६२९ ५४९ ५८३ २११ ३२८ ५२७ ३७३ १३२ २४७ १९‡ १४७ ५५४* ५४४ २३३ ४९७ |
[‡ १९७५ चे आकडे * १९७९ चे आकडे] |
भारतीय उद्योग : भारतात एकेकाळी लोखंडाचे प्रगलन विस्तृत प्रदेशात करण्यात येत होते. वेदोत्तर काळात लोखंडाच्या निरनिराळ्या हत्यारांचा व साधनांचा उपयोग वाढत्या प्रमाणात व विस्तीर्ण भूप्रदेशात करण्यात येत होता. या काळात भात्याचा उपयोग करण्यास प्रारंभ झाल्याने लोहारांना अनेक लोखंडी हत्यारे व साधने तयार करणे शक्य झाले. कांबी, चाकू, सुरे, आकडे, विळे, बाणांची टोके, कुदळी, फावडी, कडी, खिळे वगैरे विविध लोखंडी वस्तू अनेक पुरातत्त्वीय स्थळी सापडल्याचे नमूद करण्यात आले आहे आणि आणि त्यांतील बहुतेकांचा काळ इ.स.पू.६०० ते २०० असल्याचे आढळून आले आहे. पोलादनिर्मिती व मृदू पोलादाची बहुस्तरीय रचना करण्याची पद्धत (दमासीनिंग) इ.स.पू.३०० मध्ये प्रचारात होती. मध्ययुगात पर्शिया भारतातून पोलाद आयात करीत असे व सुप्रसिद्ध दमास्कस पाती भारतीय पोलादापासून बनवीत असत. दिल्ली येथील सुप्रसिद्ध घडीव लोखंडाचा स्तंभ सु. १,५०० वर्षांइतका जुना असून इतक्या काळानंतरही त्यावर गंजल्याच्या खुणा आढळलेल्या नाहीत. पुरी येथील प्रचंड लोखंडी तुळ्या, सोमनाथ येथील नक्षीदार दारे, नूरवार येथील ७.३ मी. लांबीची घडीव लोखंडाची तोफ व माळव्यातील धार येथील १३ मी. उंचीचा स्तंभ ही गतकाळात भारताने मिळविलेल्या धातुवैज्ञानिक कौशल्याचीस्मारके आहेत. मध्य प्रदेश, बिहार व ओरिसा या राज्यांतील अनेक जिल्ह्यांतील, कुमाऊँ टेकड्यांतील, तसेच कर्नाटक, तमिळनाडू व राजस्थान या राज्यांच्या काही भागांतील आदिवासी जमाती १९६० च्या सुमारासही लोणारी कोळशाच्या साहाय्याने आणि शेकडो वर्षापूर्वी वापरात असलेल्या साधनांत व पद्धतींत फारसा बदल न करता लोखंडाचे प्रगलन करीत होत्या.
भारतात व्यापारी प्रमाणावर लोखंड व पोलाद यांचे उत्पादन करण्याचा प्रारंभ १८३० मध्ये पोर्तोनोव्हो (दक्षिण अर्काट जिल्हा) येथे उभारलेल्या एका संयंत्राने झाला पण हा प्रकल्प निष्फळ ठरला. हे संयंत्र पुढे पोर्तोनोव्हो स्टील अँड आयर्न कंपनीने ताब्यात घेतले. या कंपनीचे मलबार किनाऱ्यावर बेपोर येथेही एक संयंत्र उभारले. १८५३ मध्ये ईस्ट इंडिया कंपनीने दक्षिण अर्काट जिल्ह्यात दोन व कोईमतूर जिल्ह्यात एक अशा एकूण तीन झोतभट्ट्या उभारल्या. या भट्ट्या १८५८ मध्ये बंद पडल्या. पोर्तोनोव्हो येथील उत्पादन १८६६ मध्ये व बेपोर येथील १८६७ मध्ये बंद पडले. १८५४-६४ या काळात बीरभूम जिल्हा (बंगाल) व कलाढुंगी (कुमाऊँ) येथे लोखंड उत्पादनाचे प्रयत्न करण्यात आले पण तेही निष्फळ ठरले.
पिग लोखंड कुल्टी (बंगाल) येथील बाराकार आयर्न वर्क्सने १८७५ मध्ये यशस्वीपणे तयार केले. हा कारखाना नंतर क्रमाक्रमाने बाराकार आयर्न अँड स्टील कंपनी (१८८७), बेंगॉल आयर्न अँड स्टील कंपनी (१८८९) व बेंगॉल आयर्न कंपनी यांनी ताब्यात घेतला. आता तो इंडियन आयर्न अँड स्टील कंपनीचा एक भाग आहे. पोलादाचे उत्पान १८९२ मध्ये कलकत्त्याजवळील कोसीपूर येथील मेटल अँड स्टील फॅक्टरीत सुरू झाले. हा कारखाना पुढे इशापूर येथे हलविण्यात आला.
भारतातील लोखंड व पोलाद उत्पादनाला १९०७ मध्ये बिहारमधील साकची (आता जमशेटपूर) येथे टाटा आयर्न अँड स्टील कंपनी (टिस्को) स्थापन झाल्यावर निर्णायक वळण मिळाले. जमशेटपूर येथील कारखान्यात पिग लोखंड प्रथम १९११ मध्ये व पोलाद १९१२ मध्ये तयार झाले. पहिल्या महायुद्धानंतरच्या पाच वर्षात बर्नपूर (आसनसोलजवळ) येथे इंडियन आयर्न अँड स्टील कंपनी (इस्को) १९१८ मध्ये व भद्रावती येथे म्हैसूर सरकारची म्हैसूर आयर्न अँड स्टील कंपनी (हिचे नाव आता विश्वेश्वरय्या आयर्न अँड स्टील वर्क्स असे बदलण्यात आले आहे) १९२३ मध्ये अशा दोन कंपन्या स्थापन झाल्या.
टिस्कोच्या मूळ संयंत्रात दर दिवशी प्रत्येकी २५० टन क्षमतेच्या दोन झोतभट्ट्या, प्रत्येकी ५० टन क्षमतेच्या चार खुल्या चुल्याच्या भट्ट्या व ८०,००० टन वार्षिक क्षमता असलेली लाटण यंत्रे यांचा समावेश होता. दर महिन्याला १५,०००टन कोक तयार करणारे संयंत्रही उभारण्यात आले होते. १९१९ मध्ये दर दिवशी १९५ टन क्षमता असलेली झोतभट्टी फेरोमँगॅनीज तयार करण्यासाठी उभारण्यात आली. १९५६ मध्ये टिस्कोने १२,५०,००० टन पिग लोखंडाचे व ७,५०,००० टन पोलादाचे उत्पादन केले. इस्कोने प्रथम दर दिवशी प्रत्येक ५०० टन क्षमतेच्या दोन झोतभट्ट्या व दर दिवशी १,००० टन क्षमतेच्या कोक भट्ट्या उभारल्या. १९३६ मध्ये या कंपनीने कुल्टी येथील वार्षिक ८०,००० टन पिग लोखंडनिर्मितीची क्षमता असलेली बेंगॉल आयर्न अँड स्टील कंपनी ताब्यात घेतली. १९३७ मध्ये स्थापन झालेली स्टील कॉर्पोरेशन ऑफ बेंगॉल ही कंपनी १९५३ साली इस्कोमध्ये विलीन करण्यात आली. १९५६ मध्ये इस्कोचे उत्पादन ७,५०,००० टन पिग लोखंड आणि ४,००,००० टन अंत्यरूपण केलेले पोलाद इतके होते. भद्रावती येथील संयंत्राकरिता प्रती दिवशी ५०-६० टन क्षमता असलेली झोतभट्टी आणि धातुक क्षपणासाठी व भट्टी तापविण्यासाठी लोणारी कोळसा तयार करण्याकरिता दर दिवशी २०० टन लाकूड हाताळू शकेल असे लाकूड ऊर्ध्वपातन (हवेशिवाय तापवून घटक अलग करण्याची क्रिया) करणारे संयंत्र उभारण्यता आले. पुढे झोतपट्टीची क्षमता ८० टनांपर्यंत वाढविण्यात आली. पिग लोखंडाच्या दोन विद्युत् भट्ट्या उभारण्यात आल्या. या संयंत्रात १९५६ मध्ये २९,२०० टन पिग लोखंडाचे व ३०,००० टन पोलादाचे उत्पादन झाले.
स्वातंत्र्यप्राप्तीनंतर लोखंड व पोलाद उद्योगाच्या विकासासंबंधी पहिल्या पंचवार्षिक योजनेत विचार करण्यात आला परंतु दुसऱ्या योजनेत भिलाई , दुर्गापूर व राउरकेला येथे प्रत्येकी वार्षिक १० लक्ष टन क्षमतेचे संकलित पोलाद प्रकल्प उभारण्याच्या कामास सुरुवात झाली. टिस्को व इस्को या खाजगी क्षेत्रातील दोन संयंत्रांची क्षमता दुप्पट म्हणजे अनुक्रमे २० लक्ष टन आणि १० लक्ष टन करण्याचे कामही हाती घेण्यात आले. सार्वजनिक क्षेत्रातील वरील तीन संयंत्रे १९५६-६२ या काळात टप्प्याटप्प्याने कार्यान्वित झाली व खाजगी क्षेत्रातील संयंत्रांचा विस्तार १९५९ मध्ये पूर्ण करण्यात आला. राउरकेला येथील दर दिवशी प्रत्येकी १,००० टन क्षमता असलेल्या तीन झोतभट्ट्या असलेले संयंत्र जर्मनीतील क्रप्स अँड डेमाग या कंपनीच्या मदतीने उभारण्यात आले. या संयंत्रांतील ७५% पोलाद लिंट्स-डोनाव्हिट्स ऑक्सिजन प्रक्रियेने [⟶ पोलाद] व राहिलेले रूढ क्षारकीय खुल्या चुल्याच्या प्रक्रियेने तयार केले जात होते. याखेरीज ओतशाला दर्जाचे ५०,००० टन पिग लोखंडाचे उत्पादन करण्याची या संयंत्राची क्षमता होती. भिलाई येथील संयंत्र रशियाच्या तांत्रिक व आर्थिक सहकार्याने उभारलेले आहे. या संयंत्रात दर दिवशी प्रत्येकी कमाल १,१३५ टन पिग लोखंडाची क्षमता असलेल्या तीन झोतभट्ट्या, २५० टन क्षमतेच्या सहा खुल्या चुल्याच्या भट्ट्या व इतर सामग्री बसविण्यात आली आणि त्याचे वार्षिक उत्पादन ३,००,००० टन ओतशाला दर्जाचे पिग लोखंड आणि १०,००,००० टन पिंडरूप पोलाद आणि त्यापासून ७,७०,००० टन विक्रीयोग्य पोलाद इतके अपेक्षित होते. दुर्गापूर येथील संयंत्र ब्रिटिश अभियांत्रिकी व्यवसाय संस्थांच्या समूहाच्या मदतीने उभारण्यात आले. या संयंत्रात दर दिवशी प्रत्येकी१,२५० टन पिग लोखंडाची क्षमता असलेल्या तीन झोतभट्ट्या, प्रत्येकी २०० टन क्षमतेच्या स्थिर चुल्याच्या सात भट्ट्या व १०० टन क्षमतेची एक खुल्या चुल्याची भट्टी आणि इतर सामग्री होती. या संयंत्राची वार्षिक क्षमता ३,६०,००० टन ओतशाला दर्जाचे पिग लोखंड व १०,०० ,००० टन पिंडरूप पोलाद इतकी होती.
तिसऱ्या योजनेत सार्वजनिक क्षेत्रातील तीन पोलाद संयंत्रांचा विस्तार करणे व बोकारो येथे नवीन संयंत्र उभारणे यांवर भर देण्यता आला होता. १९६०-७३ या काळात भिलाई संयंत्राची २५ लक्ष टनांपर्यत, दुर्गापूर संयंत्राची १६ लक्ष टनांपर्यंत व राउरकेला संयंत्राची १८ लक्ष टनांपर्यंत क्षमता वाढविण्यात आल्यावर सार्वजनिक क्षेत्रातील संकलित पोलाद संयंत्राची एकूण क्षमता ८९ लक्ष टनांपर्यंत वाढली. चौथ्या योजनेच्या कार्यक्रमात अस्तित्वात असलेल्या पोलाद क्षमतेचा जास्तीत जास्त उपयोग करणे आणि तामिळनाडूतील सालेम, कर्नाटकातील विजयानगर व आंध्र प्रदेशातील विशाखापट्टनम् येथे तीन पोलाद संयंत्रे उभारण्याच्या योजना तयार करून पाचव्या योजनेतील गरजा भागविण्यासाठी अधिक पोलाद उत्पादनक्षमता निर्माण करेण यांचा समावेश होता. तथापि ३१ मार्च १९७८ रोजी संपावयाच्या पण एक वर्ष अगोदरच संपलेल्या पाचव्या योजनेच्या अखेरीस बोकारो संयंत्राचा पहिला टप्पा पूर्ण झाल्यावरच १७ लक्ष टन अधिक पोलाद उत्पादन क्षमता वाढली. ३१ मार्च १९७४ रोजी ८९ लक्ष टन असलेली उत्पादन क्षमता ३१ मार्च १९७८ रोजी १०६ लक्ष टनांपर्यंत वाढली.
इंडियन आयर्न अँड स्टील कंपनीचे (इस्कोचे) कार्य सुधारण्याच्या दृष्टीने सरकारने या कंपनीचे व्यवस्थापन १४ जुलै १९७२ रोजी ताब्यात घेतले व पुढे १७ जुलै १९७६ रोजी कंपनीची मालकी संपादन केली. बोकारो व भिलाई येथील पोलाद संयंत्रांची क्षमता प्रत्येकी ४० लक्ष टनांपर्यंत वाढविण्यात येत आहे. दुर्गापूर येथील मिश्र पोलाद संयंत्राची मिश्र व विशेष प्रकारच्या पोलादांचे पिंडरूप पोलाद तयार करण्याची क्षमता १,६०,००० टन आहे. अधिक सुविकसित प्रक्रियांचा आणि अखंड ओतकामाचा उपयोग करून ही क्षमता २,६०,००० टनापर्यंत वाढविण्यात येत आहे. सालेम पोलाद संयंत्रात ३२,००० टन अगंज (स्टनेलेस) पोलादाचे पत्रे व वेटोळी तयार करण्याची क्षमता आहे. या संयंत्रात मार्च १९८२ मध्ये व्यापारी उत्पादनास प्रारंभ झाला. औद्योगिक क्षेत्रात व स्वयंपाकाच्या भांड्यांसाठी लागणाऱ्या अगंज पोलादाचे सुविकसित दर्जाचे विविध प्रकारांचे पत्रे व वेटोळी तयार करण्याची या संयंत्राची क्षमता आहे. भिलाई, बोकारो व मिश्र पोलाद संयंत्र (दुर्गापूर) यांचा चालू विस्तार पूर्ण झाल्यावर सार्वजनिक क्षेत्रातील संयंत्रांच्या होणाऱ्या क्षमता कोष्टक क्र.५ मध्ये दाखविल्या आहेत. १९८४ च्या सुमारास भारताची पोलाद उत्पादनाची वार्षिक क्षमता १.४६ कोटी टन होती. यांपैकी संकलित पोलादा संयंत्रांची १.१४ कोटी टन व लघू पोलाद संयंत्रांची (मिनी स्टील प्लँट्सची) ३६ लक्ष टन होती. १९८१ मध्ये जगातील पोलाद उत्पादक देशांच्या क्रमवारीत भारताचा सोळावा क्रमांक होता.
कोष्टक क्र. ५ सार्वजनिक क्षेत्रातील संयंत्रांची विस्तारानंतरची अंदाजित क्षमता (हजार टनांत). | ||
संयंत्र | अंदाजित क्षमता | |
कच्चे पोलाद | विक्रीयोग्य पोलाद | |
भिलाई
दुर्गापूर राउरकेला बोकारो इस्को संकलित पोलाद संयंत्राची एकूण क्षमता मिश्र पोलाद संयंत्र (दुर्गापूर) सालेम पोलाद संयंत्र |
४,०००
१,६०० १,८०० ४,००० १,००० १२,४०० २६० — |
३,१५३
१,२३९ १,२२५ ३,१५६ ८०० ९,५७३ १८५ ३२ |
द स्टील ॲथॉरिटी ऑफ इंडिया लि. (सेल SAIL भारतीय पोलाद प्राधिकरण) हा पूर्णतः सरकारी मालकीचा उपक्रम आहे. जानेवारी १९७३ मध्ये याची सार्वजनिक क्षेत्रातील पोलाद व निविष्ट उद्योगांची सूत्रधार कंपनी म्हणून स्थापना झाली. १९७८ मध्ये याची कार्यकारी कंपनी म्हणून पुनर्रचना करण्यात आली. राउरकेला, भिलाई, दुर्गापूर, बोकारो व बर्नपूर येथील संकलित पोलाद संयंत्रे, दुर्गापूर येथील मिश्र पोलाद संयंत्र व सालेम पोलाद संयंत्र यांच्या व्यवस्थापनाची जबाबदारी या उपक्रमावर आहे. इस्को ही या उपक्रमाची दुय्यम कंपनी असून बर्नपूर स्टील वर्क्स इस्कोच्या अखत्यारीखाली आहे. विश्वेश्वरय्या आयर्न अँड स्टील वर्क्स या कर्नाटक सरकारच्या उपक्रमात सेलचे ४०% भाग भांडवल आहे. याखेरीज महाराष्ट्र इलेक्ट्रोस्मेल्ट या फेरोमँगॅनीज व पोलाद यांचे उत्पादन करणाऱ्या लघू पोलाद संयंत्राचा सेलने ताबा घेतलेला आहे. सार्वजनिक क्षेत्रातील पोलाद संयंत्राचे नियंत्रण, कार्य संचालन व त्यांच्या उत्पादनांचे विपनण करण्याबरोबरच भारतातील पोलाद उद्योगाचा योजनाबद्ध विकास करण्यासाठी भारत सरकारला मदत करण्याचीही जबाबदारी सेलवर आहे. या उपक्रमाचे कलकत्ता येथील केंद्रीय विपणन संघटना, रांची येथील लोखंड व पोलाद संशोधन व विकास केंद्र आणि दिल्ली येथील अभियांत्रिकी व तंत्रविद्या केंद्र हे विभाग आहेत. रांची येथे सेलची स्वतंत्र व्यवस्थापन प्रशिक्षण संस्था असून प्रत्येक संकलित पोलाद संयंत्रातही वेगळ्या प्रशिक्षण संस्था आहेत.
सेल या उपक्रमातर्फे चालविल्या जाणाऱ्या संयंत्रांत पिग लोखंड, लोहपिंड व त्यांचे रूपांतरण करून बनविलेले विक्रीयोग्य पोलाद, उष्ण लाटण केलेली वेटोळी, पत्रे व पट्ट, गॅल्व्हानीकरण केलेले सपाट व पन्हळीदार पत्रे, कथिलाच्छादित करण्याच्या दर्जाचे पत्रे, थंड लाटण केलेले पत्रे व पट्ट्या, ओतकामासाठी व पुनर्लाटणासाठी योग्य असलेले लोहखंड, रेल्वेसाठी पोलादी पट्ट (फिश प्लेट्स) व शिळेपाट (स्लीपर्स), हलके व मध्यम बांधकाम घटक, चाके व आस, लाटून व वितळजोडकामाने नळ्या तयार करण्यास योग्य असलेले पोलादी पत्रे व पट्ट्या, विद्युत् पोलादी पत्रे, सर्पिल पद्धतीने वितळजोडकाम केलेले नळ, चिलखती पट्टाच्या दर्जाचे पोलाद, अगंज पोलाद, जोडरहित नळ्या, अणुकेंद्रीय इंधनासाठी घडीव पोलादाचे गोल वगैरे अनेक प्रकारच्या लोखंडी व पोलादी वस्तू तयार करण्यात येतात. यांखेरीज कच्चे डांबर, डांबर ऊर्ध्वपातिते (डांबराच्या ऊर्ध्वपातनाने मिळणारी संयुगे), बेंझीन, टोल्यूइन, अँथ्रॅसीन, विद्रावक (विरघळविणारा) नॅप्था, अमोनियम सल्फेट, कॅल्शियम अमोनियम नायट्रेट (२५% नायट्रोजन), दाणेदार मळी वगैरे उप-उत्पादने मिळविण्यात येतात. यांपैकी अमोनियम सल्फेट महत्त्वाचे असून त्याचे सर्व संयंत्रांत मिळून सु. १,५७,००० टन वार्षिक उत्पादन होते. राउरकेला पोलाद संयंत्रात ४,५९,००० टन आहे. अमोनियम सल्फेट व कॅल्शियम अमोनियम नायट्रेट यांचा महत्त्वाची खते म्हणून उपयोग होतो. वरीलपैकी काही उप-उत्पादने रबर, स्फोटक द्रव्ये, औषधे, बाष्पनशील तेले, रंगलेप इ. उद्योगात कच्चा माल म्हणून उपयुक्त आहेत.
खाजगी क्षेत्रात टाटा आयर्न अँड स्टील कंपनी ही सर्वांत मोठी लोखंड व पोलाद उत्पादक आहे. जमशेटपूर येथील संकलित पोलाद संयंत्राखेरीज या कंपनीच्या बिहारमध्ये कोळशाच्या खाणी व एक लोह धातुकाची खाण तसेच ओरिसामध्ये लोह धातुक, मँगॅनीज धातुक, चुनखडी, डोलोमाइट व इतर खाणी मालकीच्या आहेत. जमशेटपूर येथील संकलित पोलाद संयंत्र भारतातील सर्वांत जुने आहे. या संयंत्राची क्षमता २१.६ लक्ष टन द्रव पोलाद (किंवा १७.४ लक्ष टन विक्रीयोग्य पोलाद) आहे. ही कंपनी कांबी, बांधकाम घटक, पट्ट्या, पट्ट, काळे व गॅल्व्हानीकरण केलेले पत्रे, विद्युत् पोलादी पत्रे, रेल्वे सामग्री, लाटलेली कडी वगैरे पोलादी वस्तूंचे तसेच फेरोमँगॅनीज, शेतीची अवजारे, अमोनियम सल्फेट व बेंझॉल उत्पादने यांचे उत्पादन करते. भारतातील प्रमुख संयंत्राचे पोलाद व पिग लोखंड यांचे उत्पादन कोष्टक क्र.६ मध्ये दिले आहे.
भारतातून १९७९-८० मध्ये रु. १०५.२ कोटींचे व १९८१-८२ मध्ये रु. ७०.१ कोटींचे लोखंड व पोलाद निर्यात झाले. याच काळात भारतात अनुक्रमे रु. ८६८.६ कोटींचे व रु. १,१३६.४ कोटींचे लोखंड व पोलाद आयात करण्यात आले. १९८६-८७ व १९८७-८८ मध्येही आयात अनुक्रमे रु. १,४४९.७ कोटींची व रु. १,२७३.२ कोटींची होती.
लघू पोलाद संयंत्रे ही पोलादाच्या मोडीपासून अथवा स्पंजी लोखंडापासून विद्युत् प्रज्योत भट्टीच्या साहाय्याने पोलाद तयार करतात. ही संयंत्रे भारतातील पोलाद उद्योगाचे एक महत्त्वाचे अंग आहे. संकलित पोलाद संयंत्रे मुख्यत्वे मृदू पोलाद मोठ्या प्रमाणावर तयार करतात, तर लघू पोलाद संयंत्रे मृदू पोलादाचे, तसेच संकलित पोलाद संयंत्रांना आर्थिक दृष्ट्या परवडणार नाहीत अशा मिश्र पोलादांचे उत्पादन करतात. १९८७-८८ मध्ये भारतात १९६ लघू पोलाद संयंत्रे होती व त्यांची परवाना असलेली एकूण वार्षिक क्षमता ६५ लक्ष टन होती. यांपैकी १६१ संयंत्राचे प्रत्यक्ष कार्य सुरू झालेले होते. या संयंत्राखेरीज विद्युत् प्रज्योती भट्टी असलेली इतर काही संयंत्रे ओतिवे तयार करतात व त्यांना फेरबदल करून पोलादी पिंडांचे उत्पादन करण्याचीही परवानगी देण्यात आलेली होती.
विशाखापटनम् पोलाद प्रकल्प हा दक्षिण भारतात उभारण्यात येणारा पहिला प्रकल्प आहे. या प्रकल्पाच्या अभिकल्पात अनेक आधुनिक तांत्रिक वैशिष्ट्यांचा (उदा., ७ मी. उंचीच्या व द्रुतशीतनाची सोय असलेल्या कोक भट्ट्यांच्या मालिका, ३,२००घ.मी. इतक्या मोठ्या आकारमानाच्या झोतभट्ट्या, पूर्णतः अखंड ओतकामाची सुविधा वगैरे) समावेश करण्यात आलेला आहे. या प्रकल्पाची वार्षिक क्षमता द्रवरूप पोलादाच्या रूपात ३० लक्ष टन अंदाजित आहे.
कोष्टक क्र.६ भारतातील प्रमुख संयंत्रांचे पोलाद व पिग लोखंड यांचे उत्पादन (हजार टनांत) |
|||||||||
संयंत्र |
कच्चे पोलाद |
विक्रीयोग्य पोलाद |
विक्रीयोग्य पिग लोखंड |
||||||
१९८५-८६ |
१९८६-८७ |
१९८७-८८ |
१९८५-८६ |
१९८६-८७ |
१९८७-८८ |
१९८५-८६ |
१९८६-८७ |
१९८७-८८ |
|
भिलाई |
२,३४५ |
२,२३० |
२,४७१ |
२,०५५ |
२,१५० |
२,१७३ |
३८८ |
३१४ |
२०२ |
दुर्गापूर |
८७५ |
९२२ |
९३६ |
७२४ |
७५१ |
८३५ |
१४३ |
१५३ |
१७९ |
राउरकेला |
१,१७७ |
१,१०० |
१,११४ |
१,००५ |
१,१४० |
१,१५६ |
३० |
६० |
९७ |
बोकारो |
२,००३ |
२,०५६ |
२,४१८ |
१,७२० |
१,७४४ |
१,९६८ |
५०२ |
६४२ |
६४१ |
इंडियन आयर्न अँड स्टील कंपनी |
५६५
|
५२८ |
५४६ |
५०० |
५२६ |
५४२ |
९६ |
९२ |
९४ |
टाटा आयर्न अँड स्टील कंपनी |
२,०९५
|
२,२५०
|
२,२७६ |
१,७७१ |
१,९०८ |
१,९१४ |
— |
— |
— |
मिश्र पोलाद संयंत्र (दुर्गापूर) |
१०१*
|
१४०.४*
|
१५१.४* |
६० |
८० .०२ |
८९.२४ |
— |
— |
— |
सालेम पोलाद संयंत्र |
— |
— |
— |
२४ |
२६.६३ |
३१.४३ |
— |
— |
— |
* द्रवरूप पोलाद |
स्पंजी लोखंडाचा उपयोग मुख्यत्वे लघू पोलाद संयंत्रांत पोलादाच्या मोडीऐवजी करतात. ज्यापासून कोक बनविता येत नाही अशा कोळशाचे भारतात मोठे साठे आहेत. त्यांचा पोलाद उद्योगात उपयोग करून कोकक्षम कोळशाचे साठे राखून ठेवण्यासाठी आंध्र प्रदेशातील कोठागुडम् येथे स्पंजी लोखंड उत्पादनाचा एक विशेष प्रकल्प हाती घेण्यात आला. या प्रकल्पात उभारलेल्या संयंत्रात देशातील लोह धातुक व कोकक्षम नसलेला कोळसा यांचा उपयोग करून स्पंजी लोखंडाचे उत्पादन करण्यात येते. या संयंत्राच्या मूळच्या ३०,००० टन वार्षिक क्षमतेचा विस्तार करून ती वार्षिक ६०,००० टनांपर्यंत नेण्यात आलेली आहे. याखेरीज ओरिसामध्ये ओरिसा स्पाँज आयर्न लि. आणि टिस्को व इंडस्ट्रियल प्रमोशन अँड इन्व्हेस्टमेंट कॉर्पोरेशन ऑफ ओरिसा यांच्या सहकार्याने उभारलेला इपिटाटा असे दोन स्पंजी लोखंडाचे प्रकल्प आहेत. यांपैकी इपिटाटा संयंत्राची वार्षिक क्षमता ९०,००० टन आहे.
सरळ-क्षपण पद्धतीने पोलाद तयार करणारे एक संयंत्र जपानकडून विकत घेऊन ते मुंबईच्या बाहेर उभारण्याची भारताची योजना आहे. हे संयंत्र १९९४ मध्ये पूर्णपणे कार्यान्वित होऊन त्यात दरवर्षी १० लक्ष टन पोलादाचे उत्पादन होईल, असा अंदाज आहे.
पोलाद व खाणी मंत्रालयाच्या अखत्यारीखालील मेटॅलर्जिकल अँड एंजिनियरिंग कन्स्टल्टंट्स (इंडिया) लि. (मेकॉन) ही स्वायत्त कंपनी लोखंड व पोलाद उद्योगाला संपूर्ण सल्ला व अभियांत्रिकी सेवा, तसेच संकल्पनेपासून ते क्रियान्वित करेपर्यंतच्या प्रकल्प व्यवस्थापन सेवा पुरविते. यांखेरीज ही कंपनी सामग्री व प्रणाली अभिकल्प क्षेत्रात जागेवरच अभियांत्रिकी व संशोधन विकास करून उष्ण व थंड लाटण यंत्रे, लोखंडी व पोलादी वस्तूंवरील अंत्यरूपणाकरिता वाहक मार्ग, कोकभट्ट्या, झोतभट्टी सामग्री, वायू सफाई संयंत्र इत्यादीसंबंधीच्या संपूर्णसेवा पुरविते.
भारतात लोखंड व पोलद यांपासून मिश्र पोलादे, पूर्वरचित संरचना, विविध यंत्रांना व वाहनांना लागणारे लहान मोठे भाग, शेतीची अवजारे, फर्निचर, अगंज पोलादाची भांडी, पट्ट्या, पट्ट, नळ व नळ्या, दारे, खिडक्या, जाळ्या, गुंडाळणाऱ्या झडपा (रोलिंग शटर्स), तारा व तारदोर वगैरे विविध वस्तू तयार करणारे अनेक खाजगी लहानमोठे कारखाने आहेत. हे कारखाने कलकत्ता, जमशेटपूर, नवी दिल्ली, फरीदाबाद, लुधियाना, जलंदर, इंदूर, अहमदाबाद, बडोदे, नवसारी, हैदराबाद, सिकंदराबाद, मद्रास, बंगलोर, मुंबई, ठाणे, पुणे, कोल्हापूर, नासिक, सांगली वगैरे ठिकाणी आहेत.
संस्था व नियतकालिकके : बेल्जियममधील ब्रूसेल्स येथे इंटरनॅशनल आयर्न अँड स्टील इन्स्टिट्यूट १९६७ मध्ये स्थापन झाली. या संस्थेचे४३ देश सदस्य आहेत. जगातील पोलाद उद्योगाचे कल्याण व हितसंबंध यांना उत्तेजन देणे, पोलाद उद्योगाच्या सर्व बाजूंसंबंधी संशोधन करणे, पोलाद उद्योगाच्या समस्यांसंबंधी चर्चा करण्यासाठी व माहितीच्या विनिमयासाठी चर्चामंडळ म्हणून काम करणे, आकडेवारी व माहिती गोळा करून तिचा प्रसार करणे, राष्ट्रीय व आंतरराष्ट्रीय संघटनांसाठी संपर्क संस्था म्हणून काम करणे ही या संस्थेची उद्दिष्टे आहेत. या संस्थेतर्फे कॉन्फरन्स प्रोसिडिंग्ज, स्टॅटिस्टिकल अँड इकॉनॉमिक रिपोर्ट्स, टेक्निकल सर्व्हेज, बुलेटिन्स आणि वर्ल्ड स्टील हन फिगर्स ही नियतकालिके प्रसिद्ध होतात.
भारतात फेरस अँड नॉनफेरस मॅन्युफॅक्चरर्स ॲसोशिएशन (मुंबई), ऑल इंडिया आयर्न अँड स्टील एक्स्पोर्ट ॲसोशिएशन (मुंबई), स्टील फर्नेस ॲसोशिएशन ऑफ इंडिया (कलकत्ता), ॲसोशिएशन ऑफ स्टील फॅब्रिकेटर्स अँड डिस्ट्रुब्यटर्स (कलकत्ता) वगैरे लोखंड व पोलाद उत्पादकांच्या व व्यावसायिकांच्या संघटना आहेत.
लोखंड व पोलाद उद्योगासंबंधी अमेरिकेच्या संयुक्त संस्थानांत आयर्न अँड स्टील एंजिनिअर (मासिक), यू.एस. स्टील क्वार्टर्ली व यू.एस्. स्टील न्यूज (वर्षातून चार वेळा) ही नियतकालिके प्रसिद्ध होतात. ब्रिटनमध्ये आयर्न अँड स्टील मंथली स्टॅटिस्टिक्स, आयर्न अँड स्टील इंडस्ट्री प्रोफाइल्स (साप्ताहिक), आयर्न अँड स्टील इंटरनॅशनल (द्वैमासिक) आणि आयर्नमेकिंग अँड स्टीलमेकिंग(द्वैमासिक) ही नियतकालिके प्रसिद्ध होतात. भारतात आयर्न अँड स्टील जर्नल ऑफ इंडिया (मासिक, मुंबई), आयर्न अँड स्टील रिव्ह्यू (मासिक, कलकत्ता), टिस्को टेक्निकल जर्नल (त्रैमासिक, जमशेटपूर) व स्टील बुलेटिन (मासिक, भिलाई) ही महत्त्वाची नियतकालिके प्रसिद्ध होतात.
पहा : अभियांत्रिकी उद्योग पोलाद लोखंड लोहयुग.
संदर्भ : 1. Assocition of Iron and Steel Engineers (AISE), The Making, Shaping and Treating of Steel, 1985.
2. Bashforth, G. R. The Manufacture of Iron and Steel, London, 1964.
3. Bates, A. A. Fundamentals of Ferrous Metallurgy, Metals Park, Ohio.
4. Bose, D.M. and others, Eds., A Concise History of Science in India, New Delhi, 1971.
5. Cockerill, A. F. Silberton, A. The Steel Industry, Cambridge, 1974.
6. C.S.I.R. The Wealth of India, Industrial Products, Part V, New Delhi, 1960.
7. Dennis, W.H. Foundation of Iron and Steel Metallurgy, Amsterdam, 1967.
8. Fisher, D.A. The Epic of Steel, New York, 1963.
9. Gale, W. K. V. Iron and Steel, London, 1969.
10. Kirkaldy, J. S. Ward, R.G. Aspects of Modern Ferrous Metallurgy, Toronto, 1964.
11. Peacey, J.G. Davenport W.G. The Iron Blast Furnace, Oxford, 1979.
12. Pounds, N.J. Geography of Iron and Steel, London, 1968.
13. Strassburger, J.H. Ed., Blast Furnace :Theory and Practice, New York, 1969.
14. Swank, J.N. History of the Manufacture of Iron in All Ages, New York, 1969.
15. United State Steel Corporation, The Making Shaping and Treating of Steel, 1985.
16. Walker, R.D. Modern, Ironmaking Methods, 1986.
१७.खानगावकर, प.र. मिश्रा, वि.ना. लोखंड व पोलादाचे उत्पादन, नागपूर, १९७४.
गोडबोले, प्र.स. भदे, व.ग. ठाकूर,अ.ना.
“